Before commenting on the inexpensive chainsaw milling guides, I figured I’d better test them. Friends Bruce Kilgore and Doug Kerr, both of whom play a part in Chapter 5, were interested in helping to conduct the test. I already had a Beam Machine (www. beam machine. com) and Bruce had recently purchased a Granberg Mini-Mill (www. granberg. com). On the advice of Ted Mather, the inventor of my Beam Machine, I used an ordinary crosscut chain, not the special ripping chain recommended by most other chainsaw mill manufacturers. The regular chain, Mather says, gives a much smoother cut.
Granberg International says on their website: "Your regular stock chain on your saw works okay when it is sharpened correctly. All top angles must be the same uniform angle (25, 30, 35 degrees) and your depth gauges must be at the same height, no more than thirty – five thousandths inch below the cutting edge of the tooth. For better ripping results, resharpen your stock chain to a zero-degree top plate angle from the 25-, 30-, or 35-degree angle mentioned before. The zero degree top plate angle reduces the power needed to rip and produces smoother lumber than regular stock chain." However, Granberg goes on to say that ordinary chain, even with the specialty sharpening, does not work as well as their own Granberg Ripping Chain.
Bruce and I did not have any ripping chain and conducted our test with a machine-sharpened crosscut saw — regular crosscut sharpening — as per Mather’s advice. Our test logs were balsam fir, about 12 inches in diameter and eight feet in length. First, we tried the Beam Machine, which requires that an ordinary (finished) two-by-four be screwed along the length of the log as a guide for the first cut. We propped the log up on a couple of shorter logs so that the tip of the 18-inch bar on my Stihl 029 chainsaw was well clear of the ground.
The Beam Machine is simply a 12-inch-long (30.5 centimeter) piece of channel iron welded to a pivoting mechanism which clamps onto the chainsaw’s bar with two strong setscrews. The channel iron fits neatly to the two-by-four that has been fastened along the log’s length. The mechanism allows the operator to import a vertical and straight cut as the unit is slid along the two – by-four guide track. All three of us tried the Beam Machine, and we found that we could rip the first slab off the edge of the log in about three minutes. We also tried Bruce’s saw, but it was not sharpened as well, and took considerably longer, pointing out the importance of a well-sharpened chain. We were all impressed with the smoothness of the cut using a regular chain.
After the first slab was cut away, we had a nice flat surface for remounting the two-by-four guide. Always, the Beam Machine must travel along the guide. We simply rotated the log by 90 degrees, so that we could work vertically once again on the adjacent (second) cut. We marked the small end of the log with a pencil, showing the square eight-by-eight cross-section of the beam that we wanted to make. Just before beginning a cut, we would barely tickle the end of the log with the saw to find out if we would, indeed, be cutting on the correct — outside — side of our line. On the second cut, I failed to keep the metal guide firmly on the two-by-four track and the saw came out of the other end of the log almost an inch out of plumb.
On this first test log, we also tried Bruce’s Granberg Mini-Mill, which operated on the same principle, but used a two-by-six guide instead of a two-by-four. Combined with a superior bearing for a pivot mechanism, we found the Granberg on its wider track was easier to keep on a straight vertical line. As we used the same saw, there was no difference in the time it took to make a cut.
In four cuts, we had a passable eight-by-eight post or beam, except that — thanks to my inexperience on the second cut — the last three feet of one end took a decided turn, so the cross section of that end is an inch out of square. Well, it would do as a post!
We made a nearly perfect eight-by-nine beam out of the next log, again using both machines. All dimensions were within a quarter-inch. Again, the $80 Granberg was easier to control than the $40 Beam Machine. In fairness, I think that with practice, an operator can do an adequate job with the less expensive tool, but if I were cutting a number of heavy timbers for a job, I’d say it’s probably worth the extra money for the Mini-Mill. Doug and Bruce concurred. All told, with experience, a sharp chain, and an adequately powerful saw, an eight – to ten- foot heavy timber should be possible to make every half hour with either of these simple chainsaw attachments.
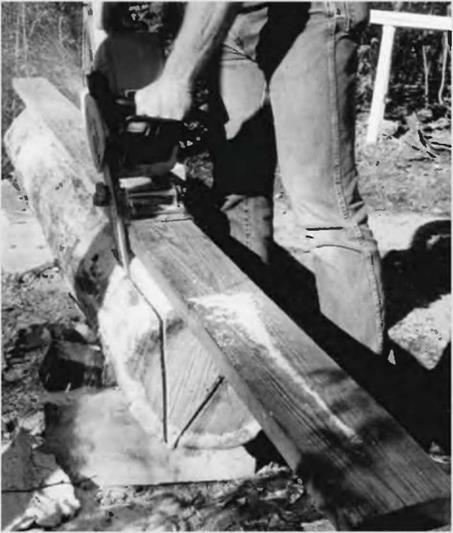
Fig. 3.3a: The Granberg Mini-Mill uses a wide two-by-six trackway for improved stability.
|
|
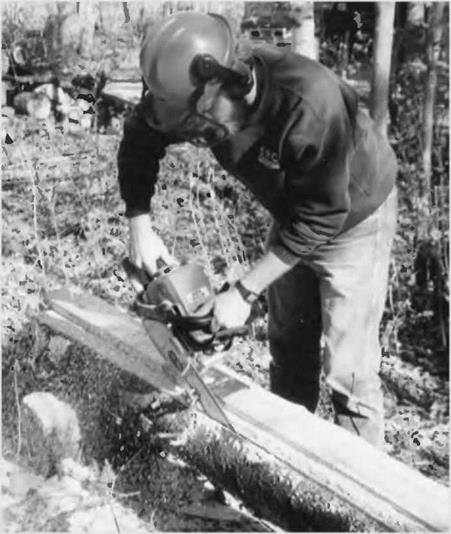
Fig. 3.3b: Doug Kerr cuts a slab off a fir log with the Beam Machine.
vertically-mounted chainsaw along the rail. About $80. Again, please see the Sidebar on pages 54-55.
• Alaskan Small Log Mill. This is the smallest of the Alaskan series of chainsaw mills, “perfect for the homeowner, woodworker or carpenter who owns a 3.8 cubic inch saw with a 20-inch bar,” according to the manufacturer. The Alaskan mills employ a different sort of guide from the Beam Machine or the Mini-Mill. The saw runs horizontally along the log, not vertically. The first cut is made using a plank guide, and additional cuts run along the first cut. About $120 in 2003.
• Basic Alaskan Mill. These mills range from the 24-inch Alaskan Mill, which will make a 20-inch (51 centimeter) cut ($150), all the way to the big 56-inch Alaskan Mill which will cut a 54-inch (137 centimeter) swath through the log ($220), although I can’t imagine why you would need any more than the 20-inch cut for making heavy timbers. None of the prices, of course, include the saw, special bar, or the special chainsaw milling chain, also called a “ripping chain.” It is not recommended to try to run any Alaskan Mill with a saw of less than 3.8 cubic inches of displacement, and larger is better.
• Complete Alaskan Mills. These are big, heavy-duty items and will allow you to cut wide thick slabs easily. You can hook up two chainsaw power heads to one bar and chain, which more than doubles the effective power. These mills run from $470 to $600, and the chainsaws, bars, and chains would add a great deal to these figures. [5]
narrow-kerf ripping chain supplied by Logosol, Richard was able to cut through white pine at a rate of about 3.2 feet per minute. Richard concludes, “For the hobby woodcutter, the Timber Jig is a $155 investment that will probably pay for itself in short order. In touting the tool as an economy lumber maker, the manufacturer may be hiding the fact that its actually an excellent timber maker as well.
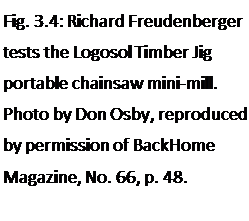
Even limited by its 8V^-inch (21.6 centimeter) depth, ripping out your own eight-by-twelve beams for a timber-frame project would save a bundle over buying them.” Richard’s complete article, with details of how to use the Timber Jig, is available in BackHome back issue No. 66. Write BackHome Back Issues, RO. Box 70, Hendersonville, NC 28793, call: (800) 992*2546 or log on to: www. BackHomeMagazine. com.
Both the Logosol and the various Alaskan Mills are a step up from the simple chainsaw guides like the Beam Machine and the Granberg Mini – Mill, and are recommended for larger projects. Yet another step up, and reflected in the cost, is the… [6]
An excellent source for purchasing many of these mills is Baileys, a woodsman’s supply house. Much of the information above comes from their 2003 Master Catalog. See Appendix C: Resources.
Making your own lumber with a chainsaw mill or bar guide is hard work, and great care must be taken both for safety and to maintain an acceptable standard of quality. Still, with a little practice, even the simplest guide attachments will yield good and useful heavy timbers.
Making timbers with a chainsaw presupposes that you are handy in the woods with the tool, as the first task will be felling the trees and maneuvering them to a clearing where you can work on the trunks. If you are not already an experienced woodsman, have someone who is teach you how to operate the saw safely and how to take down trees. Even better, take a chainsaw operation and safety course, as I should have done. I learned from experience and by necessity, but once, after about ten years of experience, I cut through a log and the tip of the saw kicked back on some hard object below. The bar, with the chain still moving, kicked back and bounced off my nose. It took a skilled plastic surgeon to make me into the good-looking guy I am today.
This book will not attempt to teach chainsaw skills. There are books and articles that do — you can search the internet — but a certified course is better. I will say that you should always wear safety chaps to protect your legs and body, and safety helmets for eye, ear and head protection. My son and I share a set of chaps, and, yes, they have been grazed on occasion. The reality is that chainsaws, handled incorrectly, can maim or kill, and so they must be treated with respect and vigilant concentration.
Having said all that, people comfortable with a chainsaw and not afraid of work can use these chainsaw mills to provide all the lumber they need, if they’ve got the trees. In a wooded building site, just clearing the house site itself, and a driveway to it, will often yield enough material to build a house. Just be careful out there!