
ir-to-air heat pumps use pressurized Freon® gas to absorb heat from the air outside and transfer it to your home. When the thermostat calls for heating, Freon is pressurized, it condenses, and then it turns
is distributed through registers in the floors, walls, and ceiling. At the same time, a fan in the condenser sends cold air outside. You can reverse the cycle for cooling in the summer. (Ground-source heat pumps
to hot liquid. A blower forces air across warm Freon-
use a water/glycol mixture to exchange heat energy
filled coils and through a system of ducts; warm air
|
|
|
|
|
|
|
|
|
 |
|
DAMPERS ADJUST AIRFLOW.
In a forced hot-air system, you sometimes can adjust the inline dampers to increase or decrease airflow to a specific part of the house. When the lever is in line with the duct, the damper is fully open. When the lever is perpendicular, it’s closed.
|
|
|
|
|
|
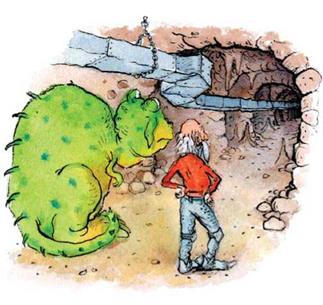
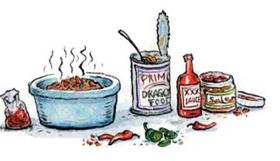
Q: The temperatures upstairs and downstairs are uneven; some rooms are colder or hotter than others. What’s causing this problem? Can it be fixed?
A: You’re likely describing an out-ofbalance duct system. If a forced-air system isn’t ducted properly, the flow of supply and return air is unbalanced, resulting, for example, in a ground floor that doesn’t stay warm in heating season or a second floor that’s not sufficiently cooled in AC season. Sometimes it’s due to poor duct design; other times it occurs when airconditioning is added to a heating system without re-evaluating and possibly resizing the ductwork.
If you have problems with individual rooms and you’ve made sure all the ducts are connected properly (believe me, I’ve seen my share of ducts to nowhere), you might be able to adjust the dampers and guide a little more (or less) air to those areas. Dampers are normally located within the first few feet of each branch, or takeoff, and are adjusted by turning an external lever. Generally, when the lever is in line with the duct, the damper is fully open. Airflow also can be regulated somewhat at the register if it’s an adjustable model; however, that can create an objectionable noise as air rushes past the louvers.
While adjusting airflow this way could improve comfort, it doesn’t help the system to perform better. To do that, you need to call in a pro. A good HVAC contractor uses a nationally approved design program to size an entire duct system properly. Ask the contractor to show you how he or she does the design work, and ask questions. The fix can range from a few simple adjustments to installing a mini-split inverter heat pump in the affected areas to ripping out everything and starting over, costing from a couple of hundred dollars to several thousand.
Q: I hear a lot about tuning up furnaces, but how can I boost the efficiency of my heat pump?
A: Like furnaces and boilers, your heat pump should be serviced annually. Cleaning the coils and changing the filter can increase the heat pump’s efficiency by up to 10%. Heat pumps are rated in SEER for cooling efficiency and HSPF or COP for heating efficiency. (See "Say What?" on p. 124.)
The higher the numbers, the higher the efficiency and the lower the operating costs.
If your heat pump operates below 13 SEER and 6.5 HSPF (the current minimum standards set by the federal government), you should plan to replace it. When you do, ask for a 410A refrigerant-based system (Carrier® calls it Puron®). The 410A-based systems are a bit more efficient and a bit more expensive, but the R-22 refrigerant currently in use is being phased out. As a result, it’s unlikely to be available when new equipment wears out.
With today’s fuel costs escalating, you might also want to consider a hybrid heating system, wherein a fossil-fuel furnace is coupled with a high-efficiency heat pump, allowing you to choose whichever system is least expensive to operate at specific times.
These setups often use automatic controls that seamlessly switch from one system to the other based on the internal programming.
Q: I keep hearing about "modulating’ technology in furnaces and boilers. What’s that?
A: Traditionally, heating equipment operates on one speed: Either it’s on, or it’s off. The minute a furnace or boiler fires up, it produces the same amount of Btu whether it’s trying to raise the temperature of a house 2°F or 20°F, and whether the air outside is -5°F or 50°F. But a number of new, high-efficiency stepped-input ("hi-lo fire") furnaces can operate at two levels: low input or high input, with a lower or higher fan speed.
Because the low-input level can be used when outdoor air temperatures are relatively moderate (roughly 70% of the heating season for many of us), modulating equipment promises fuel savings of 30% or more. When the heat-demand load exceeds the "lo-fire" output, the furnace control steps on the gas to meet demand.
Modulation technology has been limited to boilers—until now. York International’s recently released Affinity 33 is the industry’s first truly modulating gas furnace that uses outdoor reset, which adjusts the system based on the air temperature outside, to determine how hard it needs to run to meet a home’s heat loss (from 35% to 100% in 1% increments). Both the burner and the blower modulate as a team to maximize Btu, and the manufacturer claims 98% thermal efficiency.
A furnace first.
The York® Affinity™ 33 is the industry’s first modulating gas furnace and boasts 98% efficiency (www. york. com).
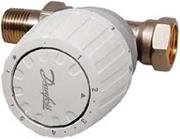
Modulation is an almost universal feature found on high-efficiency condensing boilers. Here, too, you’ll find products that can achieve 98% thermal efficiency. Virtually all these high-efficiency products use outdoor reset to achieve superior comfort and efficiency.
Q: We’re not ready to replace our heating equipment right now. What can we do to improve our comfort and reduce fuel bills?
A: If you’ ve performed the fixes I already mentioned and you’re still uncomfortable (or breaking open the piggy bank to meet fuel costs), you might consider fine-tuning your system with an auxiliary appliance.
One option is spot-treating one or more rooms with high-efficiency mini-split heat pumps. With efficiencies topping out at 26 SEER and 12 HSPF, these ultraquiet heat pumps give you the option of conditioning just the space you’re occupying while letting the rest of the home’s mechanical systems hibernate. They’re basically self-contained units with supply tubes for refrigerant running through the wall. The best ones use inverter (variable-speed) technology, allowing the units to sip only as much electricity as they need to maintain comfort.
If you have a hot-air system, adding humidification can increase comfort while letting you reduce the temperature by several degrees. You can plug in a freestanding unit or have a pro connect one to your furnace for $600 or more.
If you have a central system that’s not zoned, a motorized damper system can deliver heat where you need it most. Multiple dampers can be daisy-chained so that several rooms operate as one zone. One caution: It’s important to have a good professional do this work.
If you have a hydronic system, you can fine-tune the zones with thermostatic radiator valves, which can be installed in every room except where the thermostat is located. Once you set the dial, the valves open or close automatically based on the room’s temperature. They’re a good solution in rooms that are chronically overheated or that are seldom used.
In an uncertain economy, investing in energy—that is, the energy you use in your own home—could be your wisest move.
Your ROI (return on investment) begins the second you start using the equipment and can well exceed anything the stock market can yield. You’ll add value to your largest investment (your home), you’ll be more comfortable, and you’ll get to keep more of your hard-earned money.

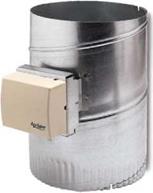
A damper with horsepower.
Motorized dampers allow for controlled airflow through ducts from remote locations and can create heating zones in a formerly one-zone house (www. aprilaire .com).
Q: What separates low-efficiency heating systems from high-efficiency models?
A: One difference is the way the unit is vented. A 78%-efficient furnace (or boiler) vents into a chimney and uses the home’s interior air for combustion. New 92%-efficient models are designed for sealed combustion. A direct venting setup draws outdoor combustion air.
|
Boilers heat water with gas, propane, oil, or electricity, and the water heats the home through a hydronic delivery system that can include baseboard fin-and-tube radiators, steam radiators, or in-floor radiant heating. When the thermostat fires the boiler, fuel burns in a combustion chamber, and warm water is pumped through a closed circuit of tubing. (Electric boilers have direct-immersion heating elements.) The water can get as warm as 180°F, depending on the system’s design. Because hot water expands, a pressure gauge and a relief valve prevent the system from failing due to excess water pressure. Combustion gases exit the house through a chimney or a direct-vent system.
|
|
|
|
|
|
|
|
|
|
|
|
|
|
|
|
Combustion-air supply—————
|
|
|
|
|
|
|
|

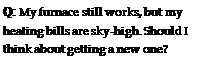
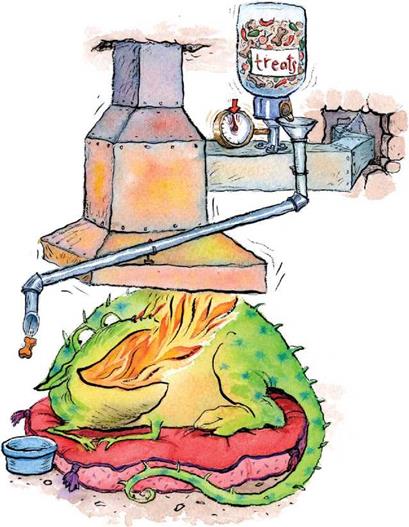
Chimney-vented heating equipment continuously drafts heated air out of the house and strips away some of the Btu produced when the furnace is operating. There’s also a hidden energy cost: air infiltration. Whenever its burner fires, the chimney-vented unit draws in warm room air to support combustion—air that must be replaced by cold outside air drawn through cracks and gaps in the home’s shell. Eliminate that draw with a sealed-combustion model, and your fuel bills could fall by 30% or more.
Cost also separates the top performers from the rest. But the difference in price between 78%- and 95%-efficient gas-fired furnaces has narrowed considerably, to about $1,500 for the equipment and installation costs. If your system burns oil, you have fewer choices, and the price gap is wider (about $4,000). But with ever-shifting oil prices, it’s easier to justify the extra expenditure.
A: Given today’s rapidly escalating fuel prices, you really can’t afford not to consider upgrading to a new high-efficiency furnace. Older furnaces were constructed with durability, not efficiency, in mind. Trimming 20% to 70% off your fuel bills is a realistic expectation when you upgrade to high – performance equipment.
Your existing furnace most likely has a 60% to 78% efficiency rating, which was once considered respectable. The current federally mandated minimum efficiency for furnaces is 80%, but there are models— hundreds of them—that operate above 92% and qualify for Energy Star rebates. There are even a few that can achieve 98% efficiency by using a feature called "outdoor reset," which modulates both the blower speed and the burner’s fuel input. As you might expect, the better the efficiency, the higher the up
front costs. But with the rise in fuel prices and the anticipated 20- to 30-year life span of a furnace, the increased purchase price pales by comparison to the fuel costs saved over time.
Dave Yates owns and operates F. W. Behler Inc., a mechanical-contracting firm in York, Pa.