An important means of achieving affordable housing is by running an efficient business. Good business planning, organization, and control are essential to keeping costs as low as possible.
Because affordable housing construction may require regulatory changes and relief from the community, it becomes very important that resultant
cost reductions are not offset by business and job site inefficiencies.
Production planning and control combine, in the best possible way, the resources available. This will assure that management, money, manpower, machines, materials, and marketing are integrated in the best way possible to produce affordable housing when the market wants it.
Hitting the right market at the right time, with the right product, can save thousands of dollars in carrying costs on land, infrastructure, sales centers, model homes, advertising, office overhead, etc. So careful market research is important.
All JVAH builders realized that the primary reason for building affordable homes was that they were priced for the largest unserved market segment in their respective communities. Some found they grossly underestimated the demand. Their buyers included those who could afford more expensive homes but preferred the JVAH units.
But, even if market potential for affordable housing may appear to be obvious, there are still many decisions that must be made and, when possible, contingencies planned for. Therefore, long – and short-range goals should be developed. Questions that may be
helpful in formulating company goals include:
• What markets are not being served today?
• What can be done if inflation increases building costs?
• What features will produce significant market advantage?
• What expensive features are unnecessary for the target market?
• What if interest rates increase? ..decrease?
• What related business could be entered successfully?
• If the firm were to redesign its construction methods from scratch, what techniques would be adopted?
In an affordable housing market, faster turnover will reduce land and infrastructure finance carrying costs. Land should be zoned for higher densities than in upper-end housing. Designs will be smaller, simpler, and more production-oriented with fewer options. High-speed production equipment and techniques are appropriate. Less skilled, less knowledgeable employees of all types can perform high-quality work on the simpler tasks required in lower-cost houses. Mass media advertising, open houses, and sales centers may be appropriate to this market.
Substantial savings can be gained by organization and control of direct costs – material, land, labor – and indirect costs – marketing and sales, finance, equipment depreciation and maintenance, and management.
Labor costs can be controlled by preplanning and scheduling of work,
using properly-sized crews, good supervision, and instilling high-quality standards in workers. See the "Production Planning and Control" and "Labor Cost Control and Reduction" sections in Construction Cost Control, available from NAHB, 15th and M Streets, NW, Washington, DC 20005.
Methodical preplanning of work reduces lost time. For example, a carpentry crew can frame a wall faster if the crew leader has detailed pull lists, cutting lists, component lists, and wall layout drawings, than if the leader has to do all the thinking on the site while his crew awaits orders.
Efficient scheduling saves time, and "time is money." The longer it takes to build a house, the greater the time-related costs which are incurred – construction loan interest, insurance, security, overhead per unit, maintenance and rate of capital utilization.
The optimum schedule is one that is reasonably attainable with some effort. The complexity of the scheduling system should not exceed that required for adequate control.
The most efficient construction crews usually have three members, although larger crews can be efficient if they form smaller work groups to do the majority of their tasks. One skilled worker on each small crew is usually enough. Having too many skilled people usually means the crew is being overpaid. Specialization improves productivity; workers who are assigned a specific task to do over and over become much more efficient at that task than a general "all-around" worker who might do the task only once every few weeks.
This is why in many cases a subcontractor, although he adds overhead and profit to his labor cost, still costs the builder less for a particular task than the builder’s own crew; the subcontractor is faster because he specializes in one task.
Good supervision saves money. A crew leader must be able to provide clear directions and keep his men working when he himself is planning, thinking, or doing his own task.
Higher level supervisors should make scheduled inspections from inspection checklists.
At each level, a supervisor should be knowledgeable enough to instruct his workers on how to accomplish any of his assigned tasks. He should consistently demand the highest quality work so that workers learn to "do it right the first time" in order to reduce expensive callbacks and rework, and to enhance the company’s reputation. He should praise good work and effort, but make the employees redo all substandard work.
Material costs can be controlled by accurate estimating, source selection, ordering, expediting, receiving, handling, and inventory control.
Careful estimating reduces waste and delays due to material shortages. Effective source selection techniques are important, such as requests for bids which evaluate payment terms, lead times, and delivery service, as well as price.
Maintaining histories of supplier performance – price, quality, service, willingness to expedite late shipments, and response to claims for shortages and damages — is useful.
Purchase orders should be used to ensure that the price, terms, and conditions are explicit so that suppliers can be held to every condition later. Invoices received from suppliers and subs should be checked against purchase orders.
To evaluate suppliers for future purchases, records should be kept of all past purchases, including quantities, prices, delivery time, quality, and any problems encountered. Suppliers should load material in such a way that when unloaded, that which is to be used first is on top. They should place it on the construction site where it will minimize handling labor. They should deliver the right amount of material to the right place at the right time. They should protect the material from weather, and, at the builder’s request, band it together for security.
On stocked items, economic order quantities and reorder points based on past usage and predicted future demand, should be calculated to minimize inventory carrying cost.
Estimated quantities and prices should be compared with actual quantities used and prices charged with variances calculated for quantities, prices, and total material costs. Positive quantity variances may mean too much material is being sent to the site which frequently results in extra waste, pilferage, and handling costs. Negative quantity variances mean there have been shortages which may have delayed production and required expensive emergency orders.
Land costs should be controlled as carefully as those of labor and material. A "quantity discount" — low price per lot – often can be gained by purchasing a large tract of land, and if not used immediately, the land may increase in value. On the other hand, it may depreciate if adjacent land is used for an industrial or commercial purpose. In addition, the longer the land is held, the greater the interest carrying cost, especially if some investment has been made in roads and utilities, etc.
Similarly, if a developer installs the infrastructure for an entire development at one time, he may receive lower prices from his subcontractors. However, he will also have to carry the interest on a large investment during the entire construction period. For this reason, and to reduce the investment required, many developers phase infrastructure installation. Also, if conditions stall sales, the developer is more likely to survive until sales pickup. Because of this risk, many builders stay out of land development entirely and buy developed lots as they need them.
Control of indirect expenses can reduce the overhead allocation applied to each housing unit.
Marketing and sales expenses must be carefully budgeted and controlled. Advertising must be aimed at the particular market segment that fits the product, and the proper advertising channels used to reach potential buyers. In some developments, a sales center which later becomes a community building is an effective marketing tool. In other developments, low unit prices are most important, and amenities such as pools, community buildings, parks, etc., raise costs beyond the reach of the target market. Often there are too few units in the development over which to spread the cost.
For some developments, demand is strong enough to justify large newspaper display ads, open houses, and full-time sales personnel. In others, classified ads and the subcontracting of sales to realtors makes sense.
Computers are making an increasing impact on the efficient flow of information used to control sales and production. For more information on computer systems, see Data Processing for Builders. National Association of Home Builders, 15th and M Streets, NW, Washington, DC 20005.
As much integration as feasible should be achieved. It should be possible to use quantities developed in the estimating procedure to automatically print requests for bids and purchase orders when accepted prices and terms are entered. Labor, material, and subcontract estimates should feed into the standard job cost system as budgeted costs against which actual costs are compared in variance reports.
For greatest timeliness, posting to the job cost system should be done when purchase orders are placed; any changes can be recorded later with change orders.
When payroll, subcontractor and material invoices are paid, the system should automatically post the general ledger and update other accounting reports.
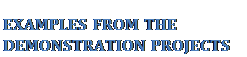
Although no systematic effort was made to determine or document cost savings due to business and market efficiency, some examples came to light
John Crosland Company sought land zoned for low-density development which they thought they could get zoned for higher-density development. They were successful in this strategy at Lynton Place and were able to increase density and reduce their land cost per unit.
Crosland did extensive market research which indicated that a mixed development with condos and medium-priced single-family homes would be successful. They generated early traffic by putting a sales trailer on the site. TV and newspaper display advertising invited people to put on their "muddy boots" and come see the plans and site.
Later, they built a sales center -future community building with two swimming pools — and seven model homes. Company personnel performed the sales duties at both the trailer and sales center. Crosland subcontracted all construction and bought wall panels for the condominium portion of the construction; the remainder was "stick-built."
In contrast, "Pup" Robertson of Robertson-Tomberlin Homes used a low-budget strategy to market his low-cost high-value brick ramblers.
His only advertising was one-column one-inch newspaper classified ads. He built two homes "on spec" and sold them. Thereafter, he and a realtor sold the remaining homes from plans.
Robertson bought all material himself, since in his area, subcontractors were small, and his buying power exceeded theirs. In his rural locale where subs were few and not as highly specialized as in urban areas, he found it cheaper to hire employees by the hour than to pay subcontractor markup and profit.
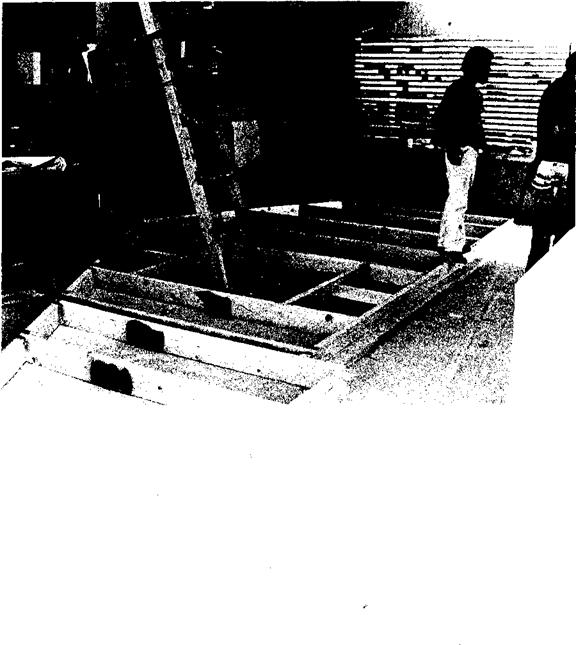
Santa Fe, Mike Chapman used the exterior shell New Mexico of the first home built as an on-site shop, which was used for fabricating balcony and stair railings, cutting and finishing trim, and general storage of high-value materials. When the project neared completion, he closed down the shop, installed partitions and fixtures, and sold the home.