Most locales have an energy code that defines how well insulated your house must be. Check with the building inspector in your community for this information. Rather than requiring so many inches of fiberglass or rigid foam, these codes define insulation requirements in terms of R-value, or resistance to heat flow. The higher the R-value, the greater the insulating value. For example, code may require that exterior walls be R-11 or R-19. As it turns out, a 2×4 wall with fiberglass insulation designed for a 31/2-in. wall has an R-value of 11. Denser batts that increase the R-value to 15 for a 2×4 wall are available. A 2×6 wall with 5V2-in.-thick fiberglass has an R-value of 19. Don’t try to stuff R-19 fiberglass batts into a 2×4 wall, though. Carpenters say that’s like trying to stuff a 1,000-lb. gorilla into a 500-lb. bag. It just doesn’t work.
Remember—code requirements set minimum standards. As far as building materials go, insulation is relatively inexpensive, so it’s often cost effective to install more insulation than what is required by code. A house with lots of insulation (in the attic, for example) will not only reduce your heating bill for years to come but may also save you money up front by reducing the size of the heating or cooling system you need to install!
to apply two beads of silicone sealant beneath their bottom plates. If this was not done for some reason, you can run a heavy bead of sealant where the inside edge of the bottom plate meets the subfloor.
Once the walls are framed, it’s important to install insulation in the sections that will be inaccessible after the wall sheathing is applied. As discussed in Chapter 4, these areas include the voids or spaces in the framing for corners, channels, and headers. Likewise, pay attention to areas where tubs and shower units will be installed in exterior walls. You don’t want the stud cavities in these areas to be blocked off before you have a chance to insulate them.
Part of a sealing strategy may include house – wrap. Modern housewraps, such as Tyvek and Typar, are wrapped around the framed exterior
|
walls and stapled over the exterior sheathing or (if exterior sheathing is not used) directly over studs and plates (see the photo on p. 197). Housewrap is effective at stopping cold air infiltration during winter months. And at all times of the year, it serves as a drainage plane behind the exterior siding, directing water that gets behind the siding downward, instead of into the wall cavity (see Chapter 6 for details on installing housewrap).
When installing windows and doors, first you need to apply a generous bead of sealant on the flange or the back of the exterior trim. Do this just prior to installation, as explained in Chapter 6. Make sure that kitchen soffits and dropped ceilings (especially those with heating or cooling ducts inside) are completely sealed off from wall and attic spaces. Use drywall or OSB, and do it now, if you haven’t already. These steps help prevent moisture-laden indoor air from moving into wall or attic areas, where it can condense and create major moisture problems.
Spray-foam insulation can handle a multitude of sealing tasks
Packaged in a pressurized can, foam insulation is extremely useful when it comes to filling gaps; sealing openings; and insulating narrow, confined spaces where fiberglass insulation doesn’t easily fit (see the photo at left).
Although it’s not cheap, spray-foam insulation is so helpful that I don’t build a house without it. It’s available in expanding and nonexpanding versions. I prefer the expanding type, because it does a better job of spreading out to fill voids. If you apply too much and the foam starts to expand beyond the intended area, don’t worry. Come back later, after the foam has hardened, and trim off the excess with a utility knife. Don’t try to wipe off excess foam when the material is still sticky; you’ll just create a mess. Here are some of the areas in the house where spray foam can be used:
IN HOLES IN BOTTOM PLATES. Use foam to fill the spaces around plumbing pipes, electrical or cable wires, and ducts that
|
|
CARBON MONOXIDE MONITORS SAVE LIVES
Although tight houses improve energy efficiency, they also increase the danger of carbon monoxide (CO) poisoning. CO is a byproduct of combustion from numerous sources. Woodstoves, oil furnaces, gas-fired stoves, water heaters, and fireplaces can produce hazardous levels of CO. The problem with CO is that you can’t see it, taste it, or smell it—and it’s poisonous. For this reason, CO detectors should be installed in any home that uses a fuel-burning appliance. Detectors are relatively inexpensive; you can buy plug-in units or modules that are permanently wired into the electrical system. Install them in kitchens, utility rooms, and wherever a CO-producing appliance is located. CO detectors should be placed at least 5 ft. from the floor or on the ceiling.
|
|
Spray foam is sticky stuff.
When applying spray-foam insulation, wear plastic gloves so the foam doesn’t get on your hands. The foam is sticky and can stain your skin.
|
|
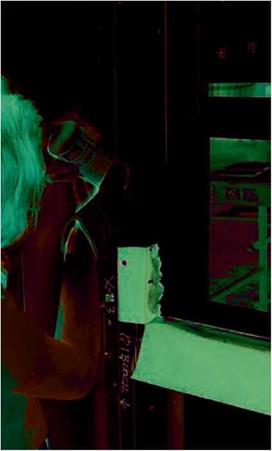
Expanding foam is excellent for sealing and insulating small spaces. A little foam goes a long way, so it’s best not to apply too much at one time.
|
|
|
|
|
CH08_HAUN_pgs.194-211.indd 198
|
|
|
when it is compressed. It’s better to insulate narrow spaces with foam insulation. The spaces between the window or door jamb and the rough opening can also be “foamed,” but be careful not to apply too much expanding foam in those areas. Because jambs are usually only 3/4 in. thick, the foam’s expansive action can cause them to bow inward.
AROUND PLUMBING AND ELECTRICAL LINES THAT PASS THROUGH EXTERIOR WALLS. If your house has exterior faucets, seal the hole around each one with foam insulation. Holes for outdoor electrical lines and outlet boxes in exterior walls should also be sealed.
Leave a reply