Prep work done, it’s almost time to paint. Even if you’ve read this entire chapter, you might want to scan it one last time for tips about paint quality, tools, basic techniques, spray-painting, and so on.
Here’s a quick review of factors mentioned in greater detail earlier in this chapter: Regarding exterior coatings, the more opaque the finish, the better it will protect wood siding. Clear, oil-based sealers help siding shed water without obscuring the wood grain, but they must to be reapplied every 2 years to 4 years because they offer relatively little protection from UV rays. A second
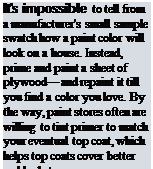

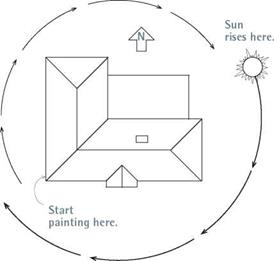
option, semitransparent stains resemble thinned down-paints and represent a compromise that adds UV protection but reduces siding visibility, That is, you can see wood texture but not its grain. Third, there’s paint that completely hides and so protects wood the best, if correctly applied. Which brings us to acrylic latex.
Acrylic latex is king. What’s not to like? Simply called latex, it’s durable, flexible, virtually odorless, and cleans up with soap and water. Use good-quality latex primer-sealer and paint on all exteriors, whether covering existing paint or unfinished siding. Oil-based primers are justified only if your siding is raw redwood or cedar, or if you’ve had problems with tannin bleed-through and so need to block stains before repainting. Latex is also best for masonry, stucco, aluminum, and vinyl siding because it’s the only coating flexible enough to expand and contract as siding heats and cools.
Optimal conditions. Check the weather before you start painting. Ideally, wait until several dry days are forecast. If possible, wait a week after a rain. Also allow morning mists to evaporate before painting. Humidity near 90 is risky, because it doesn’t allow the paint to cure. The best temperatures for curing range between 60°F and 85°F. Don’t paint when temperatures are 90°F or above, because surfaces that are too hot can cause paint to blister. Finally, stop painting 2 hours before sundown if nighttime temperatures could drop below 40°F.
If possible, don’t paint in strong sun. Paint the west and south faces of the house early in the morning; the north face at noon; and the east face and any part of the south face still remaining in the afternoon.
Latex paint should flow on easily and dry slowly enough that brush marks level (disappear). To slow the rate of drying, add a dash of Flood’s Floetrol to latex, as indicated on the container.
To slow the rate of drying of oil-based paint, add Flood’s Penetrol.
A painting sequence. Paint the house from top to bottom. To minimize overlap marks on clapboards, paint horizontal sections all the way across, till they end at window or door trim or at the end of a wall. After painting large sections, go back and paint the trim, windows, and doors, top to bottom. Last, paint gutters, porches, and decks. If you can remove shutters, doors, screens, and the like, do so; they are much easier to paint if placed across sawhorses. Don’t bother to mask trim or windows unless you’re spray-painting. Again, you can later scrap stray paint from window glass with a razor tool.
Using a brush, paint the bottom edges of horizontal siding before applying paint to the flat face of each board. To distribute paint evenly along siding, after loading the brush with fresh paint, partially unload the brush by dabbing every foot or so; then spread out the dabs, brushing the paint in and smoothing it with the wood grain. For exteriors, a 4-in. brush is the workhorse for the big spaces. A 3-in. angled sash brush is handy for cutting in trim edges and corners. For a sequence of painting window parts, see p. 450.
If the house has a stucco exterior or some other flat expanse, roll the paint on—after using a brush to cut in the edges—or spray it. Exterior rolling is much the same as interior rolling: Roll on fat paint in a zigzag pattern, before rolling it out evenly. To minimize spatter, roll the first stroke up. In general, the smoother the exterior surface, the shorter the roller cover nap.
Apply primers and top coats full strength,
except when the paint seems to be drying too quickly. Latex dries quickly and adheres well, so you don’t need to sand between coats unless you wait several days or more. Consult the label on the paint container for drying times and maximum intervals between coats. For a lasting paint job, apply one coat of primer and at least two top coats. Though it’s probably not imperative to
I Avoiding Direct Sun
Avoid the sun around the house as you paint, so that you apply paint in the shade if possible. Paint applied in full sunlight is more likely to blister later.
prime existing paint that’s in good shape and well prepped, it’s advisable. However, prime all siding that has been sanded or begun weathering down to bare wood.
Oil-based stains and semitransparent stains do not need thinning. Apply them full strength to bare wood. If you’ve stripped the house of its original paint and want to switch to stain, test a
small section first. Because a clear stain will probably look uneven, a semitransparent stain is likely the better bet. To apply stain, a paint pad will hold more stain than a brush but requires a little practice to avoid runs.
As with paint, apply stain to the undersides of the shingle or clapboard courses first. To avoid getting stain on your skin, wear a long-sleeved shirt, rubber gloves, a hat, and safety glasses.
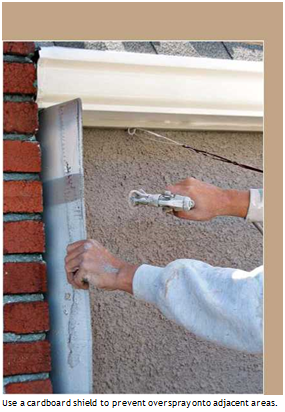

Spray
► Spray exterior trim first. Mask the siding, spray the trim, and let it dry before removing the first masking. Then mask over (cover) the trim so you can paint the siding.
► To mask-off windows, apply double-sided masking tape around the perimeter of the window. Press sheet plastic to the tape and trim off the excess plastic.
► To keep paint off features such as chimneys and roofing, use a cardboard shield to block the spray, as shown at left.
► Don’t spray when it’s windy. Even if the air is calm, move cars and lawn furniture away from the house, or cover them. If your house is close to a neighbor’s—ask the neighbors to do the same or, better, do it for them.
► After you spray a section, immediately brush the paint into the surface. Back-brushing helps sprayed paint adhere better, look great, and last longer.
But because latex dries so quickly, back-brush before spraying the next section.
After spraying a section of siding, immediately brush the paint into the wood—and into the building seams— using a 4-in. brush.
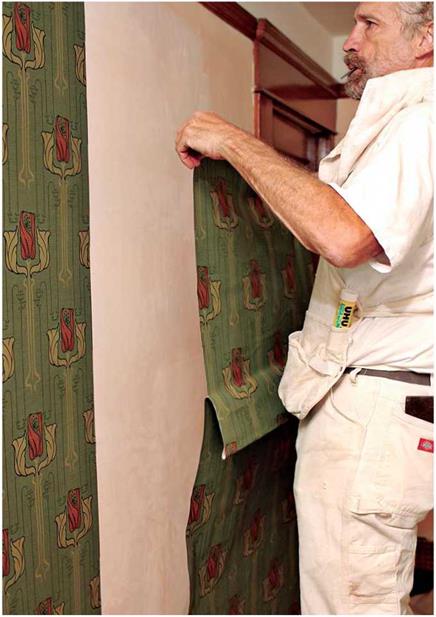
Wallpaper has been popular for centuries, particularly in formal rooms where there’s less danger from little ones’ grimy fingers and rowdy ways. Paint has long been favored for rooms that get the most use and abuse because it’s durable and easy to clean and apply.
Today “wallpapers” are available in so many materials—including grasses, bamboo, rice paper, foil, and cork—that they are collectively called wallcoverings, and some of them are stronger, more durable, and easier to maintain than wallpapers and some paints. Many are backed with paper or cloth, with cloth being stronger. But by far the most popular are vinyl- coated wallcoverings, which are washable and grease resistant.
Today, most wallcoverings come prepasted. This makes them easier to apply and—years later—to strip from the wall. Because the manufacturer has already pasted the covering, all you need do is unroll it, and soak it briefly in a water tray. But, as you’ll see in this chapter, many pros avoid the drips and mess of a water tray by rolling a prepaste activator onto the backing.
Selecting Materials
Choose a wallcovering whose pattern and color are appropriate for the room. There are no hard and fast rules on what works. But in general, lighter colors make rooms look larger, and darker colors make rooms look smaller. Smaller, subdued patterns are better for quiet rooms. Splashy floral prints tend to serve better in places such as front halls that bustle with activity. Delicate textiles or grasses are best reserved for rooms with little traffic and little risk of bruising. Also, consider the age and energy level of the people in the room. For example, vinyl-coated murals of rock stars or sports themes will appeal to kids and endure abuse.
To hang wallcovering, first unfold the top half of a pasted strip and carefully align it to a plumbed line, or to the plumbed edge of the preceding strip.
Washable wallcoverings can be sponged clean occasionally with a mild soap or cleaning solution. Scrubbable coverings can take a vigorous scouring with a nylon-bristled brush or a pad, as well as stronger cleaning agents. There are also strippable and peelable wallcoverings, discussed



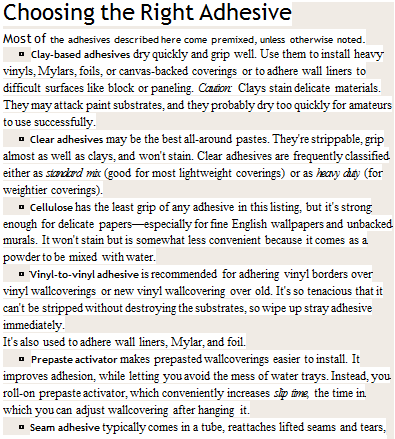
at greater length in “Stripping Wallpaper,” on p. 470.
For do-it-yourselfers, it’s smart to choose a covering that’s easy to hang. That is, textured coverings can be fragile and difficult to handle. The condition of existing walls should also affect your decision. For example, heavy coverings can conceal minor wall flaws; whereas lightweight papers will accentuate flaws and won’t conceal underlying bold paints or vivid patterns. If walls or trim are badly out of square, avoid coverings with large, bold patterns because slight mismatches along their edges will be more obvious than if patterns are subdued.