Residential neighborhoods often have overdesigned, underutilized sewer systems which local officials must review for cost reduction possibilities. Various sanitary sewer system alternatives are available today to communities using traditional, outmoded procedures, designs, and materials.
Following are guidelines for sanitary sewers:
• Use curvilinear sewers where feasible.
• Increase maximum manhole spacing.
• Use cleanouts as an alternative to manholes for maintenance.
• Use plastic pipe instead of concrete or metallic pipe.
• When appropriate, use inside drop connections.
• Design sewer pipe size and slope to meet the need.
• Use "state-of-the-art" inspection procedures.
• Use common laterals.
Requiring fewer manholes than the norm, encouraging curvilinear sewer designs, and allowing use of cleanouts can save money for developers, local governments, and home buyers. Curvilinear sewers reduce the total length of sewer pipe, but the greater savings are from a reduction of manholes at $1,000 to $1,500 each. Hydraulic performance within a sewer is not adversely affected by the curved sections.
Although many communities require that manholes be spaced at a maximum of 200 to 400 feet, many more places now permit spacings in excess of 600 feet, due to improved methods of maintenance and construction and equipment development. For example, flush trucks capable of cleaning sewer lines 600 to 800 feet in length are now standard equipment for many public works departments.
Cleanouts can be provided in lieu of manholes both in curvilinear and straight runs. Cleanouts can also be installed at a much lower cost than a manhole at the terminal end of the sewer line. They offer a cost effective alternative in flood prone areas or in areas of high water tables because of installation, lower material costs, and better protection against infiltration.
Although cleanouts are a proven cost – effective alternative, manholes may still be required at a slope change or where multiple pipes converge.
Plastic pipe is being used in an increasing number of communities, offering reductions in material, installation, and replacement/main – tenance costs when compared to total costs of more "traditional" materials.
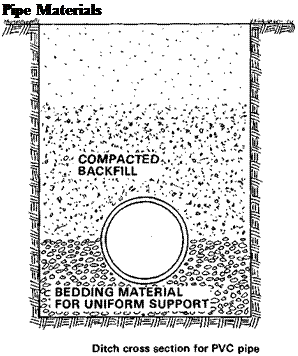
Polyvinyl chloride (PVC) is strong, lightweight, and considerably less expensive than concrete and metallic piping and has proven its durability and reliability over several decades of use in sanitary systems. Many of the early problems associated with PVC can be traced to improper bedding procedures. If the entire length of the pipe, including joints, is supported by the bedding materials, the pipe is secure. A clean, carefully placed backfill is also recommended.
Sewer designers and construction crews installing sanitary sewers must insure the continuous flow of wastewater through manholes, especially when significant elevation differences exist between the influent and effluent pipes. Most areas require an outside drop connection to convey wastewater across an elevation drop, a costly solution requiring added piping and concrete blocking. An inside drop connection is less costly because it requires less materials, is easier to install, reduces stress at the connection and needs less excavation and backfill.
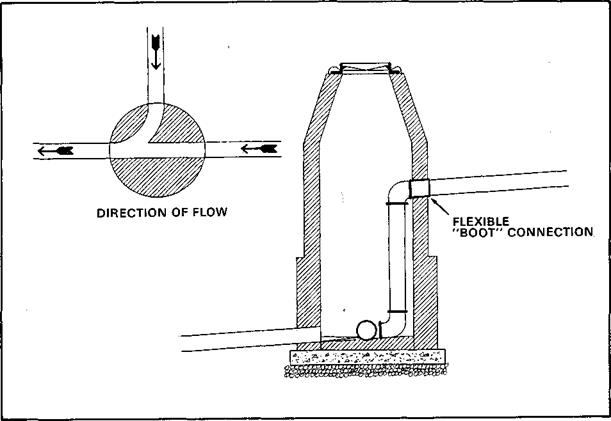
Inside drop manhole
|
|
A sanitary sewer must be designed to coordinate with a master plan for sewer extensions, which all communities should have to ensure efficient integrated systems. Often, in lieu of a master plan, community standards arbitrarily require a minimum 8-inch diameter pipe. In many instances, especially on cul-de-sacs, deadends, and other areas where the sewer serves only a few houses, smaller pipes of 4 or 6 inch diameter actually provide better service because of faster flow. Larger pipe sizes may be detrimental since they could promote deposition of solids at low flows. A З-inch house lateral is generally sufficient for a single dwelling unit.
Sizing criteria should be evaluated to reflect actual conditions. In the past, 100 gpcd was considered the standard design flow from a dwelling. However, researchers have shown that 40 to 50 gpcd more accurately reflects typical average flows.
An "across the board" minimum slope cannot be applied to all pipe. The minimum slope required for a sanitary sewer should not be an arbitrary standard, but should be determined for a specific site. Flatter sloped sewers reduce trenching depth, a critical factor where bedrock or other obstacles exist.
|
SUMMARY OF AVERAGE
|
DAILY RESIDENTIAL
|
WASTEWATER FLOWS
|
|
|
|
|
Duration
|
Wastewater Flow
|
|
|
No. of
|
of
|
Stucjy
|
Range of
|
Indi vi dual
|
Study
|
Resi dences
|
Study
|
Average
|
Residence Averages
|
|
months
|
gpcd
|
9PCd
|
Linaweaver, et al.
|
22
|
–
|
49
|
36
|
– 66
|
Anderson and Watson
|
18
|
4
|
44 (
|
18
|
– 69
|
Watson, et al. ‘
|
3
|
2-12
|
53
|
25
|
– 65
|
Cohen and Wallman
|
8
|
6
|
52
|
37.8
|
– 101.6
|
Laak
|
5
|
24
|
41.4
|
26.3
|
– 65.4
|
Bennett and Li nstedt
|
5
|
0.5
|
44.5
|
31.8
|
– 82.5
|
Siegrist, et al.
|
11
|
1
|
42^6
|
‘ 25.4
|
– 56.9
|
Oti s
|
21
|
12
|
36
|
8
|
– 71
|
Duffy, et al.
|
16
|
12
|
42.3
|
|
–
|
|
.Weighted Average
|
44
|
|
|
Source: On-Site Wastewater Treatment and Disposal Systems, U. S. EPA – 1980
|

Television cameras can locate leaks with a higher degree of accuracy than a visual inspection conducted by a maintenance crew because they actually travel the distance of the pipe. If combined with an effective maintenance program, T. V. inspections help to insure quality construction and indirectly result in savings in future repairs or replacement.
Common laterals can be used to connect the public sewer to more than one house, reducing total trench
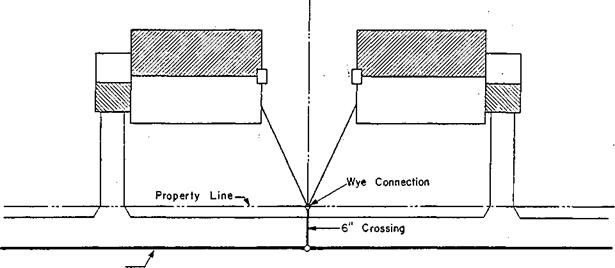
length and quantity of materials.
Since many communities charge fees based on the number of connections, additional savings come from the reduction in the number of connections to the main.
Two adjoining lots can be serviced by one lateral installed along the common property line with an easement dedicated to insure access for maintenance and/or replacement. A standard wye fitting is installed at the junction of the individual building drains. Pipe length is decreased by almost 50 percent since every other lateral is eliminated.
Clusters and townhouses also adapt well to common laterals by connecting three or more units to a single line.
In any application of common sewer connections, benefits increase as the distance from buildings to public sewer increases.
Public Sewers An alternative to the traditional Alternatives high-cost public sewer system is the various on-site technologies currently available; the most typical is the conventional septic tank/soil absorption system.
Considered an excellent system if functioning properly, the septic system has several advantages: the need for a treatment plant is eliminated, sewer mains and pumping stations are eliminated, sewer tap fees are eliminated, and groundwater recharge is encouraged.
There is also a major disadvantage with septic systems: a large percentage of soils in the U. S. are not suitable for this purpose.
On-site mound or fill systems are gaining acceptance across the nation in areas where soil conditions were previously considered "unsuitable."
Evapotranspiration systems, effective in semi-arid climates, "treat" septic tank effluent by discharging it into an evapotranspiration bed. The effluent is disposed of through evaporation and plant uptake. In community on-site systems, the land best suited for a soil
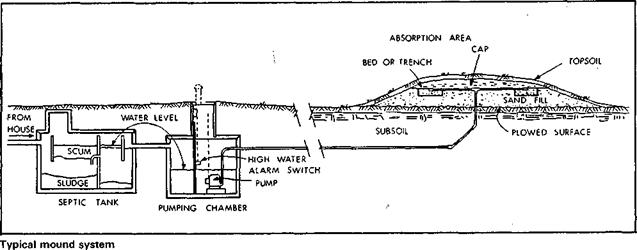
Source: Residential Wastewater Systems, NAHB – 1980
|
|
absorption system is reserved for the drain field. Effluent from each dwelling is pumped from (or flows from) an individual septic tank to the community drain field. Although the absorption area required for the system would be much larger than an individual drain field, it can be used for other purposes such as open space requirements.
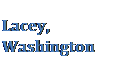
At "The Park," John Phillips was allowed to use 6-inch diameter PVC branch sewer mains to serve 15 to 25 dwellings. The city normally requires 8-inch sewer mains.
Curvilinear sewer lines were used, allowing Phillips flexibility in serving more units with one lateral or branch feeder. Phillips used the PVC pipe manufacturer’s data for curving the pipe, and Lacey accepted the curved lines based upon the pipe manufacturer’s recommendations.
Four-inch diameter PVC sanitary sewer laterals with 4-inch wyes to serve several detached and attached units were requested and approved. Major trenches and laterals were reduced by about 75 percent over conventional use. Although this was a one-time only approval, Phillips believes that with a good maintenance track record the method will be approved for general use. Total sanitary sewer costs were reduced by almost $61,000.
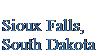

Ronning Enterprises, Inc., builder/developer of the Sioux Falls demonstration site, installed curvilinear sewers instead of straight-run sewers. Manholes were spaced approximately 460 feet apart, an increase over the Sioux Falls norm. Six additional manholes would have been necessary had the more traditional sewer system been used. This resulted in a savings of $6,000 or $80 per unit.
Standard spacing between manholes in Everett is 300 feet. City officials permitted a maximum distance of 600 feet at the Sunridge project, developed and built by Rich Boyden. Three manholes were eliminated for a total savings of about $3,500.
Increased manhole spacing was also permitted in Charlotte, North Carolina.
Cleanouts were allowed in place of normally required manholes in: Crittenden County, Arkansas; Christian County, Kentucky; and Portland,
Oregon.
Plastic pipe was permitted in: Charlotte, North Carolina; Oklahoma City, Oklahoma; White Marsh, Maryland; and Phoenix, Arizona.
One sewer was allowed for two or more units in: Burlington, Vermont, and Charlotte, North Carolina.