Design is a process of continuing revision that doesn’t stop until you have finished architectural drawings, if then. The closer you get to a design that works, the more information you need. Once you have a floor plan that satisfies most of your program requirements, double-check the assumptions underlying your design. Then revisit your local planning department with your proposed floor plan superimposed on your lot and with elevations or a model. Make sure you ask detailed questions about anything that seems unclear.
Remember, the more specific information you bring to the planner, the better feedback you’ll
get. You can save yourself a lot of backtracking if you confirm that officials will allow you to do the renovations as designed and that you can afford to continue. Make sure you understand the approval process. Many communities require design review or other approvals before you can even apply for a building permit. If you will be living in the house while working on it, get a temporary certificate of occupancy (C. O.).
The same principle applies when discussing construction costs with a contractor. Though you may not yet have the working drawings required for a detailed estimate, you’ll have enough to confirm ballpark costs with a reputable contractor. If you have floor plans and elevations or a model, you are about one-third of the way through the design process.
WORKING DRAWINGS
Once you’ve reconsidered layouts in light of the constraints noted above, proceed to working drawings, which should include accurately drawn floor plans and elevations. Details required for these drawings depend on several variables, the most important being how big the job is and who’s doing the work. A conscientious, experienced builder who practices sound construction and knows code requirements can usually intuit what needs doing even if drawings lack occasional details.
In addition, final drawings are essential because (1) the contractor needs them to give you a solid estimate; (2) they help the contractor anticipate problems and suggest changes before scheduling subcontractors; (3) lenders require them; and (4) many municipalities require tight drawings before issuing work permits—that is, in most communities, both planning and building departments review plans.
How detailed should finished drawings be?
As a minimum, building departments require a cross section from foundation to roof so they can see how the building is framed, insulated, sheathed, and finished. Thus if the job is complex—say, a major kitchen remodeling or more than one room—hire an architect to create a set of working drawings. Because construction documents are usually 40 percent to 50 percent of an architect’s total fee, and that fee is customarily 10 percent to 15 percent of total costs, figure that working drawings with floor plans, elevations, and cross sections will be roughly 5 percent of your total budget.
An Overview of Renovation
For handy reference, here’s a step-by-step review of important planning considerations. It begins by reiterating planning steps and then presents a typical sequence for construction.
A PLANNING OVERVIEW
1. Make wish lists, and analyze what works and what doesn’t in the existing house. Keep a renovation notebook. Then consider how well your designs will satisfy your wish list.
2. Measure rooms, noting the location and condition of the structure and utility systems. Map the site, and consider how well exterior design changes fit the neighborhood.
3. Consider physical and financial constraints. Talk to a contractor about renovation costs. Get preliminary approval on financing.
Visit your local planning department.
4. Generate design variations. As favorites emerge, compare them to your wish list and to any constraints. Rework designs until you settle on one.
5. Double-check your design. Revisit the planning department with floor plans and either elevation drawings or a cardboard model.
6. Prepare permit plans and obtain permits. In most communities, the permit process consists of two steps (planning permits and building permits). If you will be living in the house while working on it, get a temporary C. O.
7. Prepare working drawings. List in detail all building components, assemblies, materials, and finishes.
8. Obtain bids from contractors, and select one. The more detail you give bidders, the more realistic and accurate the bids will be.
A RENOVATION SEQUENCE
Be prepared to continue making design decisions as work proceeds. No matter how detailed your plans, you’ll need to make adjustments as you renovate. The order in which you complete tasks also depends on the coordination of subcontractors. Here’s a typical sequence, if such a thing exists.
1. Clean up. Clean out debris and add rough weather-proofing to gaping holes. Organize the site for efficient work flow.
2. Secure the building so you can store materials and, if necessary, live there.
3. Install temporary facilities such as electrical field receptacles and chemical toilets; hook up temporary utilities.
4. Handle major structural work in the basement or crawl space, repairing damage and flaws that could cause further settling. Correct water problems that could threaten the structure.
5. Replace or replumb posts, columns, girders, and joists that have deteriorated.
6. Demolish walls, ceilings, and floors, and remove debris as it accumulates. If you’re not living in the house, install temporary facilities before you start demolition.
7. Do necessary structural carpentry, such as altering load-bearing walls, joists, headers, and collar ties.
8. Attend to the roof as soon as practical.
(But make structural changes first, because they could undermine the integrity of a finished roof.)
9. Install windows, doors, and exteriors.
10. Erect interior partitions, the nonbearing walls not framed earlier.
11. Rough out heating, plumbing, gas, and electrical systems (no fixtures yet). Install insulation.
12. Hang wall and ceiling surfaces such as drywall.
13. Install underlayment for finish floors; apply tile floors.
14. Set plumbing fixtures and radiators for baseboard heat, wire electrical receptacles, and so on.
15. Finish taping drywall.
16. 

Install cabinetwork and countertops.
17. Paint and wallpaper. (Some renovators do this after trim is in place.)
18. Repair and replace trim around windows and doors. Hang doors, and finish all interior woodwork.
19. Finish floors.
20. Install final details, such as baseboard trim, interior doors, electrical outlet plates, hardware, and floor registers.
Case Histories
Renovation is rarely an easy road. Even the happy endings can take more time and money than owners thought they had. Renovation also requires the courage to start and then the stamina to stay with it.
RUTHERFORD HOUSE
The renovators: Martha Rutherford, an educator, loved traveling and collecting indigenous art. Her husband, Dean, a contractor, had lived for six years in Latin America before deciding that the priesthood was not for him.
The house: Two-story, owner-built box was erected in 1929. The builder’s widow finally moved on in 1992, after spending most of the previous decade in the living room with four Dobermans, a goat, and a duck. The animals rarely went outside. Dean and Marty stepped carefully into the gloomy interior (the ceiling was painted black), looked at the living room, looked at each other, looked at their real estate agent, and said, "We’ll take it.”
What worked: Location, location, location. Marty is a city gal, Dean a country boy. The wooded site in the Berkeley hills allowed them to live near a major metropolitan area and yet be in the country. But the decision to buy was more mystical than rational.
What didn’t work: The widow had abandoned the bottom floor because it had a year-round stream running through it. The northwest corner of the house was completely gone. The kitchen floor joists were so sodden they were spongy, and the bathroom had rotted out. Between every pair of rafters was a rat’s nest. A beehive blocked the furnace flue. Dean: "I guess the house brought out my seminarian training—you know, salvation and all.”
Constraints:
► Dean had just 3 months to get the house habitable before resuming his construction business full-time.
► The Rutherfords were determined to live within their means, so the renovation would need to stretch over several years.
► Although neighbors were delighted that the property would finally be fixed up, they were wary of the job’s scope and impact.
The plan:
► Stabilize the structure.
► Add a third story to gain views of the setting and give the house street appeal.
► Open it up: "We wanted a house totally open to the outdoors, with a deck off almost every room."
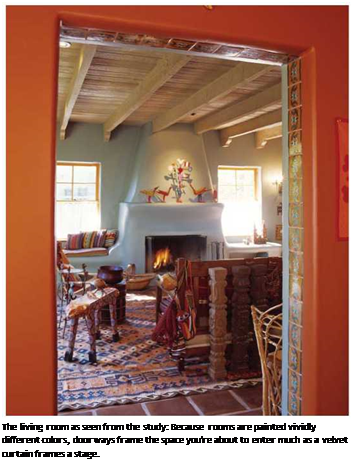
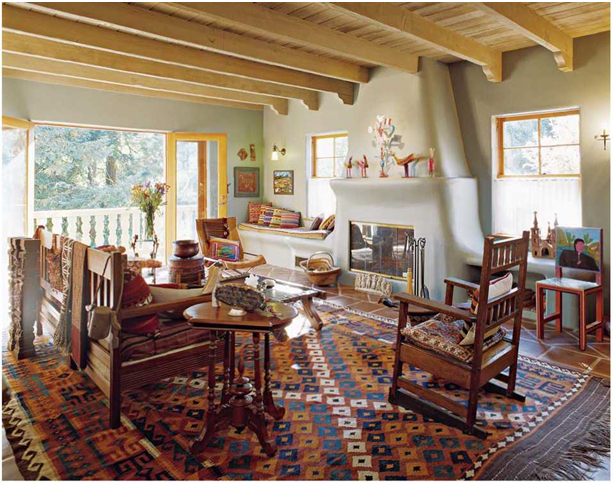
Compromises: Initially, color was a source of conflict. Because her mother had been a painter, Marty grew up surrounded with vibrant colors. Having spent years in monastic settings, Dean had grown up, as he terms it, "in a white world” and feared that Marty’s saturated colors would absorb light and darken the interior, but agreed to them anyway.
Surprises: Because Marty and Dean entered no farther than the living room when they committed to buying the house, the structural problems were a shock. Yet, for Dean the biggest pleasant surprise may have been the colors Marty felt so passionate about. As the two added skylights, opened walls, and installed French doors, they
Posted by admin on 12/ 11/ 15
In some countries a substantial amount of research has been dedicated to baghouse fines, considering them as potential material for use in mixtures. Their use has an economical aspect since the high efficiency of dust collectors in up-to-date asphalt plants collects considerable amounts of dust that are then available for use essentially free of charge. Using some of the dust from dust removal is an everyday practice in many countries. It has been applied to SMA, along with other types of fillers.
The results of studies on the practicality of using baghouse fines are quite divergent. One might conclude that the appropriateness of their use cannot be generalized. Properties of extracted dusts may differ widely, depending on their origin (i. e., source rock type). It is common knowledge that large amounts of collected dust added to mixtures may substantially stiffen them, making them susceptible to cracking and water damage, and asphalt mixes that contain them are not easy to place and compact. Despite that, baghouse fines can be a very good filler (Asphalt Review, December 2004).
Finally it is worth noting one more application aspect of collected baghouse dust. If we want to use baghouse fines as filler, they have to satisfy the standard requirements for fillers, including those concerning the repeatability and uniformity of obtained results. Frequent changes of aggregate types (i. e., rock types) may result in fluctuations in the mineralogical composition of the collected dust and its properties.
The European standard EN 13043 accepts baghouse fines as filler aggregate if they meet the standard requirements for fillers.
Posted by admin on 12/ 11/ 15
Many accessible publications (Iwahski, 2003; Judycki and Jaskula, 1999, Little and Epps, 2001) on the use of hydrated lime as an additive to asphalt mixtures have pointed out its positive effect. Apart from a substantial increase in water and frost resistance arising from an improvement in the binder adhesion to the aggregate, an increase in resistance to permanent deformation may also be noticed.
Hydrated lime is distinguished by its strong mixture-stiffening properties at high temperatures. It should be kept in mind that, according to Rigden, voids in hydrated lime can be very large. In connection with that, one should not exceed the standard content of lime in an asphalt mixture, usually accepted as 1.0-1.5% of the aggregate mass. Such an addition of lime will benefit the mixture without the risk of overstiffening.
According to EN 13034, ready-made filler containing hydrated lime is called a mixed filler.
Posted by admin on 12/ 11/ 15
How many gallons does that tank hold? Do you know how to determine the capacity of a tank? Well if you don’t, you’re about to see an easy way to find out. Before you can start to do your math, you have to know if you will be working with measurements in inches or in feet. You also have to know that the tank diameter is known as D and the tank height is H. We are looking for the tank capacity in gallons, which we will identify in our formula with the letter G.
When the measurements for a tank are expressed in inches, you will use a factor of 0.0034 in your formula. Tanks that are measured in terms of feet require a factor of 7.5. For our example, we are going to measure our tank in inches. This particular tank is 18 inches in diameter and 60 inches in height. The generic formula for this type of problem is as follows: G = d2 X h X 0.0034. We know some of the variables, so we have to put them into our equation.
The diameter of our tank is 18 inches and the height is 60 inches, so our formula will look like this: G = 182 X 60 X 0.0034. What is 182? It’s 324. This is found by multiplying 18 by itself or 18 X 18. Now we know that we are going to multiply 324 by 60 as we follow our formula. This will give us a number of 19440. The last step of our formula is to multiply 19440 by the 0.0034 factor. This will result in an answer of 66.10. We are looking for the maximum capacity of the tank, so we adjust the 66.10 to an even 66 gallons. That wasn’t too bad, was it?
CYLINDER-SHAPED CONTAINERS
cylinder-shaped containers could be tanks, pipes, or any other number of devices. What happens if you want to know the holding capacity of such an object? You are going to need to use a formula that involves the radius (R) of the object, the diameter of the object (D), the height (H) of the object, and the value assigned to л, which is 3.1416. Our goal is to find the volume (V) capacity of a cylinder. There are two types of formulas that can be used to determine the capacity of a cylinder, so let’s take them one at a time.
The first formula that we are going to use looks like this: V = л r2 h. Another way to find the answer is to have V = л divided by 4 d2 h. Either formula will give you the same answer, it’s just a matter of choosing one formula over another, based on your known elements of the question.
Posted by admin on 12/ 11/ 15
Bridges are public structures. Lead poisoning caused by lead-based paint has come to the forefront of public awareness. Any inconvenience to the public due to bridge maintenance calls attention to the structure and ongoing operations. If not handled well, lead – based paint removal from bridges can become a volatile community issue. Some states have passed regulations requiring public notice. The highway agency should be prepared to provide complete, accurate, and current documentation on the safety procedures that are implemented to protect the public health and the environment.
Gaining regulatory agreement with the removal and containment methods will also be valuable in reducing public concern. Adjusting the timing for paint removal activities to be conducted during off-peak hours also serves to diminish the attention that the operation receives.
Posted by admin on 11/ 11/ 15
Another shaping tool that comes in handy is a chisel. A chisel is often used to cut notches in wood (such as for a lockset) or to shave a bit off a joint to ensure a perfect fit.
Chisels come in various sizes. Most carpenters can get by with a set of chisels ranging in size from 1A in. to 1 in.
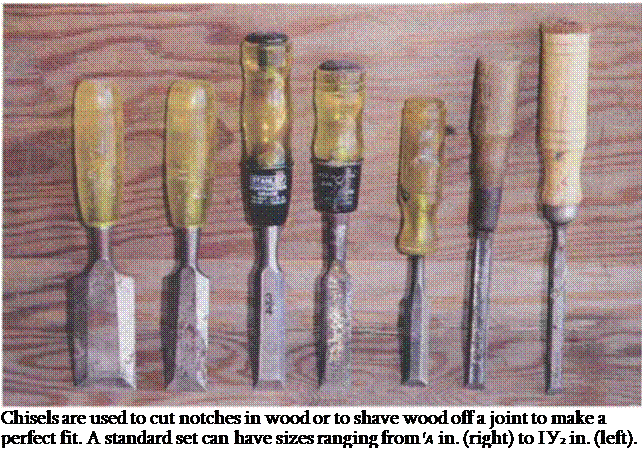
Using a chisel As with a handplane, sharpness is essential when working with a chisel. A dull blade is dangerous and makes it difficult to achieve a smooth, clean cut. To keep the chisel sharp, don’t use it as a screwdriver or as a pry bar.
A chisel has a straight side and a beveled side. When cutting, keep the beveled side facedown into the cut. Point the blade of the chisel away from your body to help prevent injury in case of a slip.
To protect the chisel handle, many carpenters use a mallet rather than a hammer to hit the chisel (see the top photo on p. 20). For best results, cut with the grain—otherwise, you’ll tear out chunks of wood.
When not in use, protect the chisel’s cutting edge with a couple of loops of electrical tape or wrap it in a clean cloth.
Files and rasps
Files and rasps are also handy items to keep around the job site. Files come in many different sizes (from smaller than a pencil to longer than a hammer), shapes, lengths, and cutting ability (roughness). Originally designed to shape metal, files can be used to smooth and form other materials as well, including plastics (such as Formica) and wood. Their teeth are shaped to cut on the push stroke. A good beginning set should include a three-cornered file, a flat one, and a round one.
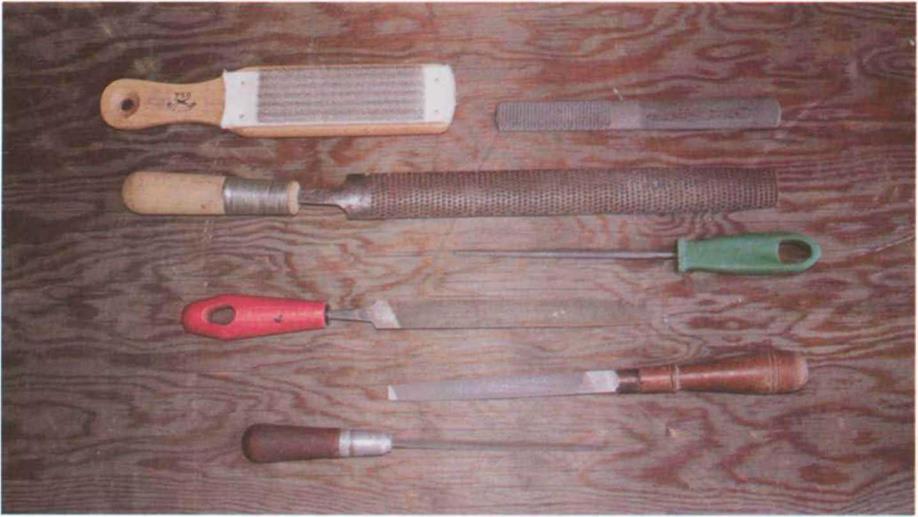
Files and rasps are handy shaping tools. The four tools at the bottom are files. The top right tool and the long one near the top are rasps. The wood-handled tool at the top left is a file card, which is used to clean both files and rasps.
|
|
Rasps have larger teeth than files do and are designed to remove a lot of wood. They, too, come in various sizes and shapes. A good rasp for a carpenter to own is the four-in-hand rasp. It has one flat side and one oval side, with four different cutting surfaces.
The cutting teeth of a file or rasp will eventually get plugged with metal or wood. When this happens, clean the teeth with a file card, which is a tool with short, stiff bristles that can remove any gunk with a few strokes.
Posted by admin on 11/ 11/ 15
The easiest way to envision change is to draw it. For this, tape tracing paper over the floor plans you drew earlier and start rearranging rooms. Because you drew your floor plans to scale, your overlay drawings will likely be reasonably accurate. If you’re unsure about the dimensions of a room, a fixture, or a piece of furniture, measure again. Also measure the space you’ll need to open and pass through doors, pull chairs away from a
|
|
Large kitchen open to backyard
|
|
Hall for improved circulation
|
|
Enlarged living room open to front yard
|
|
 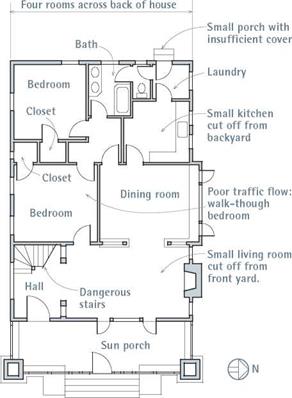 
FLOOR PLAN: BEFORE FLOOR PLAN: AFTER
The original floor plan presented a pleasant face to the After weighing a number of floor plans, the architect
street, but the back of the house was a hodge-podge of settled on the design that solved the most problems.
doors, dead spaces, and tiny rooms.
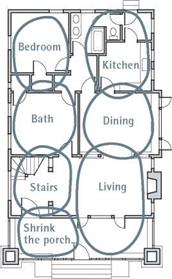 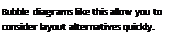
table, or remove food from the oven. Have fun, but be realistic: Don’t try to fit too much into a small space.
Whether you draw "bubble diagrams” to indicate room usage or arrows to show traffic flow between areas, create optional arrangements, including some you at first might not think you’ll like, for they might suggest possibilities you otherwise might not have considered. Think creatively, "outside the box,” as they say. On paper, it’s easy to move rooms to different locations. Analyze the trade-offs between one floor plan and another. In general, the more problems a design solves, the better. Feel free to borrow features from one plan and graft them onto another. Considering different designs also helps you decide your priorities.
Some layouts will dictate themselves—such as dining rooms next to kitchens with lavatory nearby—but most are fluid and all should be based on common sense. Put bedrooms away from noisy rooms and busy streets, if possible.
When visiting the bathroom in the middle of the night, you shouldn’t need to pass through another bedroom or a public room. Don’t forget to include closets in or near each bedroom, and a closet by the front door.
Design with nature. If your kitchen faces east, you can enjoy morning sun with breakfast. A living room on a westerly wall gives a view of the sunset. North-facing bedrooms will be cooler at night.
Glazing along a south wall can provide a substantial amount of free solar heat in colder months but may require awnings or heat-reducing window films in warmer months. If you live in the Sun Belt, where heat gain is less desirable, try to exploit prevailing breezes and to provide sufficient overhangs along south-facing walls.
In this regard, many states regulate the energy budget for houses and additions by controlling the amount and type of glazing allowed and by requiring energy-performance standards for other building components.
Other ways to look at things. In order to see how your floor plan will translate into a threedimensional structure, either draw elevations or build a model of the existing house with the proposed changes. Until you have drawn elevations or built a model, you can’t be sure your design will work, especially if you are expanding the envelope of the house.
If you’re dexterous, make a model of cardboard; most art-supply stores stock the necessary materials. Using a scale of ’/2 in. = 1 ft., draw floor plans and an elevation for each face onto the cardboard, cut them out with a utility knife, tape them together, and install a roof.
Posted by admin on 11/ 11/ 15
Design of proper containment requires the participation of specialists in structural engineering, coatings, ventilation, and exhaust. The following considerations should be
addressed in the development of a containment system:
• The environmental media (air, water, soil) that are vulnerable and the containment methods that will provide the best protection
• Durability
• Compatibility with the selected removal method, and potential for interference with the productive removal of the paint, mill scale, and rust and the application of a new coat of paint
• Ease of construction, disassembly, and moving from one area of the structure to another
• Local climate conditions
• Continued usability of the structure and proximity of nearby structures and people
• Cost-effectiveness
• Compliance with applicable regulations
Materials used to construct containments include rigid panels or flexible materials such as tarpaulins. The selected materials should be fire-retardant, given the sparking hazard, high dust, and high ventilation aspects of the procedure.
The checklist provided in Table 1.16 may be followed in designing an appropriate containment system. Various debris-recovery assessment methods are underdevelopment. Some, such as air monitoring and analysis of soil and water samples to evaluate whether
TABLE 1.16 Containment Design Checklist
1. Review drawings and specifications for project familiarity.
2. Investigate OSHA and EPA regulations affecting worker protection and control over emissions.
3. Determine method of surface preparation to be employed.
4. Examine the structure to be prepared:
• Confirm that the selected method of preparation is suitable.
• Determine if any coats of paint will be applied in containment.
• Assess the load-bearing capacity of the structure to support containment.
• Examine the structure for attachment points for the containment.
• Divide large structures into logical containment units according to size and configuration. Consider the air movement requirements and the need to have a large enough area for productive surface preparation and painting.
• Determine if a working platform should be used on elevated projects. Determine how far ground covers should extend beneath or around the removal operation.
• When working over water, determine if a barge is going to be used for spent abrasive collection or staging, and assess the need for water booms to minimize problems due to inadvertent spills. Determine the need for U. S. Coast Guard approval and navigation restrictions.
• Determine methods for conveying the debris for recycling or disposal.
5. Determine project-specific ventilation requirements.
• Consult Industrial Ventilation: A Manual of Recommended Practice (Committee on Industrial Ventilation, American Conference of Government Industrial Hygienists, Cincinnati; 20th ed., 1988) for engineering guidance.
• Select the air velocity (air speed) throughout the work area and exhaust volume required.
• Determine the necessary transport velocity through the exhaust ductwork required to avoid dropout of debris.
• Lay out the ductwork as short as practical with as few bends as possible. Do not use bends with a centerline radius less than 2 times the duct diameter. Include the use of exhaust hoods or plenums within containment.
• Select the air-cleaning device (dust collector) on the basis of the volume of air and dust loading of the airstream (air-to-cloth ratio).
• Select the fan that will provide an adequate volume of air, and that is able to overcome the resistance throughout the system.
• Provide adequate makeup air (supply air), properly distributed to provide a uniform airflow. Include properly balanced forced air if required.
• Confirm that all of the above will provide ample airflow throughout the work area. If not, consider the use of localized ventilation and exhaust.
6. Obtain and review equipment manufacturers’ technical information.
7. Complete the design package. Utilize the expertise of structural and mechanical engineers,
industrial hygienists, coatings specialists, and equipment specialists.
Source: From K. A. Trimbler, Industrial Lead Paint Removal Handbook, 2d ed., Steel Structures Painting
Council/KTA-Tator, Inc., Pittsburgh, 1993, with permission.
lead content has increased as a result of paint removal activities, have been codified in regulations.
A method for calculating debris recovery that has been used by the South Carolina Department of Transportation is found in the Struchual Steel Painting Council (SSPC) Guide 61, Guide for Containing Debris Generated during Paint Removal Operations (SSPC 92-07, March 1992). The following equation is used in the SSPC guideline for estimating debris recovery:
where RE = efficiency of recovery
Wd = dry weight of abrasive and paint debris collected
Wa = dry weight of abrasive used
Wp = calculated weight of paint to be removed
This estimation procedure has the limitation of not incorporating the weight of the various release media (air, soil, water), which influence the effectiveness of a containment. A 1 percent debris loss into the soil is not as significant as a 1 percent debris loss into the air. Care must be taken when using this method to measure only the abrasive and paint from the project and not to measure soil that may have come into contact with the debris.
The project designer should incorporate an environmental monitoring plan to evaluate the effectiveness of the containment methods. Reporting and record keeping within the plan should include the following data:
• Name and location of the site, along with a site plot plan
• Identification of the individual or company that is conducting the monitoring
• Name and qualifications of the analytical laboratory used
• Criteria and rationale for selecting monitoring and sampling sites and duration of sampling
• Descriptions of sampling and monitoring methods
• Quality assurance and quality control plans
• Examples of reporting forms
• Acceptance criteria
• Reporting procedures and corrective actions if acceptance criteria are not met
Posted by admin on 11/ 11/ 15
E. Merriam is a 59-year-old woman who complained of frequent flu-ІІке symptoms after beginning employment at a new location. Symptoms seemed to recur every month and were especially severe over the winter. Conventional medications were of no benefit. After two years of watching her health decline, she discovered that the building in which she worked was being treated prophy – lactically one weekend a month with a pesticide that contained an organophosphate called Durs – ban. Associating her flu-ІІке symptoms with the monthly pesticide applications, she felt she could no longer continue to jeopardize her health and left her job. Three years later, she finally regained her health but she remains sensitive to petrochemicals.
Discussion
In December 2001, the EPA partially banned the organophosphate Dursban for indoor use because of overwhelming evidence of harm to humans and wildlife. But, in spite of its acknowledged extreme toxicity, it can legally be used until stockpiles run out. Outdoor use, including agricultural applications, is still permitted.
Chlorpyrifos is the active ingredient in many pesticide products, including Dursban. Organo- phosphates are known to be neurotoxic and can cause damage to the brain and central nervous system, resulting in learning, memory, and behavior problems. They can also damage the immune system, increasing the risk of severe allergies, chemical sensitivities, and cancer.
10 includes a discussion of pest management that emphasizes preventing pest invasions through the use of physical barriers and the control of moisture, which eliminates potential food sources.
Electromagnetic Fields
Electromagnetic energy is ubiquitous. Some electromagnetic waves, such as sunlight, are natural. Other fields, such as radio and television waves, microwaves, and power line frequencies, are generated by human activity. Scientists classify electromagnetic waves according to frequency, which corresponds to the wavelength. At one end of the spectrum are the infinitesimally short, high-frequency gamma rays. At the other end are long, extremely low-frequency vibrating waves that may stretch for thousands of miles and are used by submarines for underwater communication.
The magnetic field that envelops the Earth produces a steady, nonoscillating direct current at 7.83 cycles per second, or 7.83 hertz, similar to that of the human body. This current pulsates on and off, but the electrons producing the electricity always move in a single direction. Each cell in the body has a pulsating vibration with an associated electromagnetic field (EMF). Communication between cells in the body is a function of electrical charges. These charges generate electrical currents that govern many of the body’s major functions, such as heartbeat, nerve conduction, and transport across cell membranes. These natural fields pulse on and off but do not oscillate.
Manufactured fields oscillate back and forth. Unlike natural current, the electrons
creating the fields change direction and thus are called alternating current (AC). The electrical power grid operates at 60 hertz and simultaneously produces an electric and a magnetic field. Each field has distinct properties and is measured separately using different meters. Common sources of 60 hertz electromagnetic fields include power lines, electrical wires, electric blankets, fluorescent lights, televisions, and other household appliances.
Radio waves are a form of electromagnetic field. On a typical radio receiver set you will find a dial, known as a frequency tuner, used to change stations. As you move the dial to the higher numbers, you are increasing the frequency of the radio electromagnetic field you are seeking; when you move the dial to lower numbers, you are reducing the frequency. AM radio stations are found between 550 and 1600 kilohertz (550,000 and 1,600,000 hertz). If the radio could be tuned all the way down the dial to 60 hertz, you would be listening to the (very noisy) sound of electrical equipment.
There are major differences between radio waves and the electrical waves used to power equipment. One difference is that radio waves are broadcast through the air; they are wireless and can travel for extended distances. Electricity, on the other hand, is transported through wires. It would be ideal if the fields from wiring systems stayed in the wires while the electricity is transported from one place to another. The problem is that wires “leak.” They broadcast electromagnetic fields, with the distance dependent on amperage. Amperage is analogous to the volume at which electric fields are being transmitted through the wires.
Assume that a radio receiver could be tuned to radio stations operating between 40 and 80 hertz. As mentioned previously, if you were to tune the dial to 60 hertz, you would hear a lot of noise because electricity in the United States operates at 60 hertz. Next, assume that you take the same radio receiver to Europe. Upon tuning the radio to 60 hertz, you would hear nothing because the European power system operates at 50 hertz.
To experiment with the sound of electricity, take a cheap AM transistor radio and tune it between stations at the low end of the dial. By holding the radio near an operating electrical appliance or a dimmer switch, you will pick up static. The buzzing noise you hear is not the 60 hertz frequency but rather higher frequency interference created by the 60 hertz frequency. Before meters for measuring elevated electromagnetic fields were readily available, some people would use an AM radio to obtain a rough idea of whether an area contained elevated manufactured electromagnetic fields. The method is far from foolproof, but it was certainly better than nothing. Several models of inexpensive meters are available today that provide more accurate assessments.
Many scientists agree that electromagnetic fields have biological effects, but they disagree on the exact effects and whether they are harmful. Research has indicated that magnetic fields can induce a small electrical field inside the body, which in turn creates an electric current in and around the cells.14 This current has been thought to alter the function of cell chemistry and to inhibit or enhance cell growth. Although there is no consistent dose/ response relationship between magnetic fields and cancer, experiments on laboratory animals have shown that magnetic fields cause changes in protein synthesis and hormone levels.
Studies in Europe have indicated that exposure to varying levels of electric fields can contribute to nervous disorders such as insomnia, depression, and anxiety. One US study found an increase in aggressive behavior among baboons exposed to electric fields.15 Other studies have indicated that there maybe a synergistic influence between magnetic and electric field exposures, making the combination more harmful than exposure to either field alone.
Over the past 50 years, people have been exposed to ever increasing amounts of manufactured radiation. The long-term consequences of this exposure are not clearly understood. Millions of Americans are now unwittingly engaged in long-term experiments on themselves. Whereas Sweden and Switzerland have set national limits for certain types of electric and magnetic field exposure, the US government has not. From time to time our government has officially recommended “prudent avoidance” (without defining the levels it would be prudent to avoid). Yet epidemiological studies have linked elevated child leukemia risks to exposures as low as 4 milligauss.16 Given the potentially dangerous (albeit controversial) consequences of EMF exposures, coupled with the ease of reducing these exposures in new construction, it may make sense to explore strategies for EMF reduction when planning and building a new home. Several simple and inexpensive measures to reduce EMF exposures are explained in Division 11 (in the sections on appliances and electric and magnetic fields) and in Division 16.
Curiously, the magnetic portion of the electromagnetic field is indirectly prohibited by the National Electrical Code. The code specifically prohibits net current, or current that is uncanceled, because it creates heat and is a potential fire hazard. Net current is also what creates magnetic fields, although most electricians are not aware of this. When magnetic fields are found in wiring, this usually is the result of a wiring error that violates code. Preventing magnetic fields caused by wiring is simply a matter of introducing protocol on the jobsite that ensures a building has been wired to code.
Naturally Occurring Pollutants
Not all toxins are manufactured. Some naturally occurring substances in homes can have harmful effects on humans. Some of these pollutants include radon and radioactive contaminants, trace metals, house dust, molds, and pollens.
Radioactive Contaminants
Radioactive contaminants such as radium and uranium occur naturally within the Earths crust. During the decay or breakdown of uranium, radon is produced. Radon is an invisible, odorless radioactive gas that seeps from the ground into homes, commonly through cracks in the foundation or basement slab or through mechanical openings. Radon can also enter the groundwater and affect water supplies.
Closed spaces present a hazard because radon levels can build up to values thousands of times higher than outdoor levels. High radon levels can cause radiation exposure equivalent to thousands of chest x-rays per person on an annual basis. Information on detecting and preventing radon contamination in homes is provided in Division 7.
Heavy Metals
Heavy metals are natural components of the Earths crust. They cannot be degraded or destroyed. Heavy metals are trace elements with a density at least five times that of water. Living organisms require trace amounts of some heavy metals, including iron, copper, manganese, molybdenum, and zinc, but even these beneficial trace minerals can cause toxic reactions in excessive amounts.
Other heavy metals, such as mercury, lead, aluminum, and cadmium, have no known beneficial effect on living organisms, and their accumulation over time can cause serious illnesses. Each metal targets different areas of the body. An area commonly affected is the brain and nervous system, resulting in learning, behavior, and memory problems, mood disorders, tremors, and early dementia. But any organ of the body can be targeted and symptoms can be as wide ranging as high blood pressure, anemia, rashes, and cancer.
Heavy metals are present in the air, food, water, and countless human-made chemicals and products.
Heavy metals in trace amounts can often be found in drinking water. Metals such as aluminum, copper, and lead can accumulate over time in human tissues and are known to cause damage to the brain, liver, and kidneys. Having drinking water tested for contaminants is advisable in order to determine if a water purification device will be necessary. Refer to Division 11 for further information.
Other sources of heavy-metal exposure in the indoor environment include insecticides and herbicides, fungicides and rat poison (arsenic and cadmium), cigarette smoke, paint pigments (cadmium and lead), contaminated air and soil around the home, dust particles,
cookware (aluminum), pipes (lead and copper), and flame retardants (antimony).
Biological Pollutants
Biological pollutants include pollen, house dust, and mold spores. Pollens from weeds, grasses, flowers, bushes, and trees enter the house through the doors and windows. They can be problematic for people with allergies. Air filtration methods are addressed in Division 15.
House dust is composed of much more than simply soil. It is a complex mixture of dust mites, animal dander, mold spores, textile particles, heavy metals from car exhaust, skin cells, and more. Mites are a major culprit in causing allergies from house dust. They feed on skin cells and breed in mattresses, pillows, carpets, and upholstered furniture. Although generally harmless, their skeletal parts and fecal matter, which stick to dust, can elicit allergic reactions in sensitive people. Dust mites require humidity ranges greater than 50 percent to thrive.
Mold plays a significant role in triggering allergies, asthma, and chemical sensitivities. Mold can produce byproducts as toxic as some of the most hazardous manufactured chemicals that affect the nervous and immune systems. Though commonly assumed
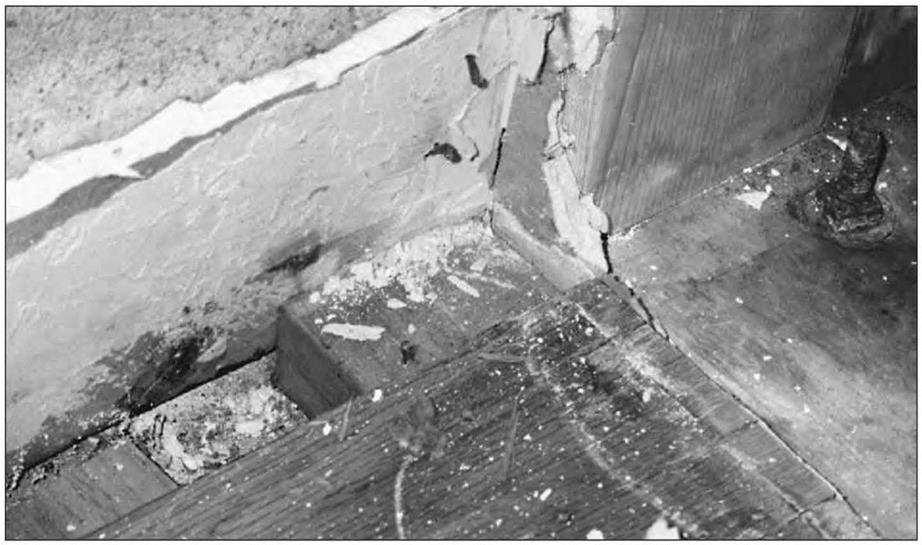
The Problem: Gypsum board was glued directly to concrete block below floor level. Ground moisture passing through the block wall and condensation has resulted in mold growth on the gypsum board. Recommendation: Proper drainage design would have prevented moisture movement through the wall. Gypsum board is particularly vulnerable to mold growth when damp. If the block had been furred out prior to installation of gypboard then there would have been more opportunity for drying to occur.
Photo: Restoration Consultants.
|
|
| |