Wood construction connectors are commonly called Simpson™ Strong-Ties™ after the company that popularized them. For a complete overview of available connectors from Simpson, go to www. strongtie. com. Professionals swear by these ingenious connectors for three main reasons.
►They offer wood-to-wood connections superior to most traditional construction methods. For example, unlike toenailing, metal connectors are unlikely to split lumber ends or loosen under stress. These galvanized steel connectors are strong and durable.
►They greatly strengthen joints against earthquakes, high winds, and other racking forces. They can tie rafters to walls, walls to floor platforms, and the substructure to its foundation.
►Most can be attached to existing framing, a great boon to renovators, and in many cases steel connectors are the only cost-effective way to bolster the existing structure and tie additions to the original structure.
Joist hangers are indispensable in renovation when you want to add joists but can’t end-nail, either because access is limited or because you’re using engineered lumber, which is too thin in cross section to end-nail successfully. (Sawn-lumber joists and I-joists require different hangers.) There are joist-hangers for single joists, double joists, 4×10 beams, joists intersecting at a 45° angle, and so on. You also have the choice of face-mount or top-flange hangers. Top flanges are popular because they effortlessly align the tops of I-joists with the top of a header or beam.
Strap ties come in myriad shapes—tees, right angles, twists—but all help keep joints from pulling apart. Install flat strap ties where wall
|
Wood construction connectors. (Contractors generally refer to them by their Simpson catalog numbers.) I, H2.5, H4, and H8 hurricane ties; 2, L90 reinforcing angle; 3, LS70 skewable angle (bend one time only); 4, A35, A35F, and A34 framing angles; 5, U410 face-mount hanger for 4×10 beam (or double 2x10s);
6, LU28 face-mount hanger for 2×8 joist; 7, H10 and H1 hurricane ties.
|
|
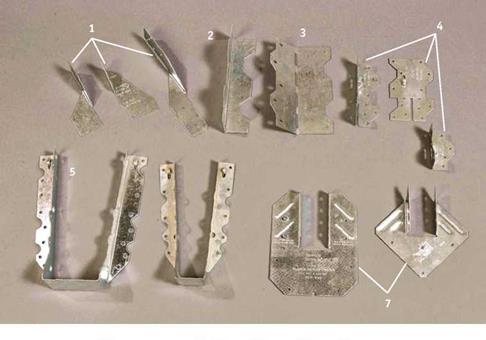
Straps, ties and angles. Clockwise, from lowerleff;T-strap (post-to – beam connector), SST22 light-gauge strap, ST6224 (24-in.) strap, MST24 heavy-gauge strap, twist strap, and heavy-gauge L-straps.
|
|
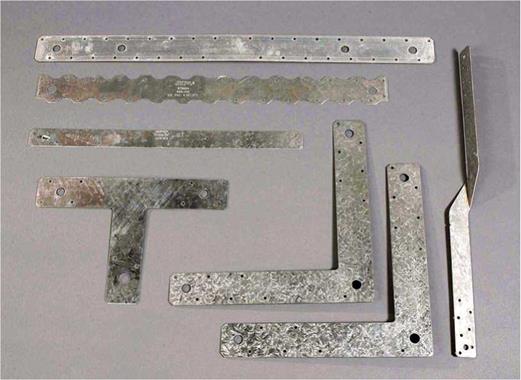
plates are discontinuous or where rafter pairs meet at the ridge. Strap ties also keep floor platforms from separating, much as shear walling does. Hurricane ties, or twist straps, have a 90° twist to join rafters to top plates, thereby fighting the tendency of roofs to lift during a strong crosswind. T-straps and L-straps are face-nailed to members joining in a right angle.
Clips vary by function. H-clips are an alternative to solid blocking when installing roof sheathing. They also act as JL-in. spacers so roof sheathing can expand. Drywallclips allow you to eliminate some blocking in corners, but it’s best to use these clips sparingly; solid blocking is much stronger. Deck clips are nailed to deck joists, and then 2×4 decking is driven onto the sharpened
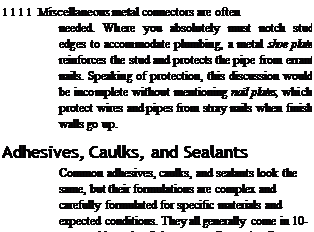
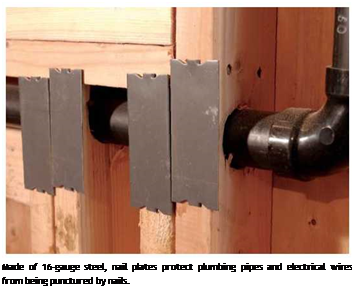

ing gun). You then simply cut the cartridge nozzle to the desired diameter and squeeze the long pistol-grip trigger to lay down beads of the stuff.
CONSTRUCTION ADHESIVES
Construction adhesives bond to a remarkable variety of materials, including standard lumber, treated lumber, plywood and OSB panels, dry – wall, wall paneling, rigid insulation, concrete and masonry, tile, metal, and glass.
Construction adhesives are a boon to builders. Instead of nailing sheathing every 6 in. around panel edges and every 10 in. "in the field,” builders using adhesives need nail only every 12 in. Being flexible, adhesives fill surface irregularities and double as sealants. Structurally, panels bonded with adhesive are stiffer and capable of bearing greater loads than panels that are only nailed. Floor sheathing and stair treads so bonded are far less likely to flex, pop nails, or squeak. Drywall ceilings bonded with adhesives do a better job of deadening sound and cutting air infiltration.
A number of considerations should determine your choice of adhesives: the materials being joined, strength, durability, flexibility, shrinkage, conditions on the work site (especially temperature and humidity), workability, curing time, ease of cleanup, and odor.
Most solvent-based adhesives create waterproof bonds and clean up with mineral spirits. Most water-based adhesives create water-resistant bonds and clean up with water. Because solvent-based adhesives often have strong odors that are problematic for people with chemical sensi
tivities, there’s a growing selection of solvent – and odor-free adhesives—and whole lines of environment-friendly adhesives.
Fortunately, you don’t need to be a chemist to find a suitable adhesive. Many manufacturers now offer on-line interactive product selectors on their Web sites, such as the Titebond™ company (www. titebond. com). Choose the adhesive features you want, and the on-line selector will choose the most appropriate product. Once you pick an adhesive, download product specs and study them: particularly application, curing times, cleanup, and safety advice.
A POTPOURRI OF ADHESIVES
Here’s a primer on common adhesives you may encounter.
Polyurethanes are often touted as all-purpose waterproof adhesives, capable of bonding wood, stone, metal, ceramics, Corian®, and so on. Strong, versatile, and easy to use, polyurethanes are favorites with builders and woodworkers. Since they require some moisture to set up, it’s possible to glue up wet wood with polyurethanes. In fact, you should moisten extremely dry wood joints before application.
Acrylics are good for outdoor use. They’re quick drying, strong, and completely waterproof.
Epoxy resins are famous for their strength. Typically mixed from two components, epoxies can bond to materials on which almost nothing else will—that is, when the surface areas to be bonded are small or when dampness is extreme. Epoxy products are especially important in foundation repairs and seismic strengthening (for more information, see Chapter 10).
Resorcinol is a strong, waterproof glue used by boatbuilders, among others. Like epoxy, it is a two-part glue that is very difficult to remove once it has set. Wood parts fastened with resorcinol will probably shear before the glue itself does.
Styrene-butadiene is a good all-purpose exterior and interior glue for joining materials of low porosity, such as tile and masonry.
Contact cement is commonly used to bond veneers and laminates to a base material, often particleboard. Once the sheets come in contact with each other, separation or realignment is all but impossible.
Hot-melt glues are applied with an electric glue gun and are excellent for tacking surfaces quickly. However, strength and water resistance are only so-so, because hot glues are applied only as spots. Still, they’re great for building templates out of thin plywood strips (see Chapter 13).
SEALANTS AND CAULKS
As noted in "Sticky Names,” above, sealants and caulks do pretty much the same thing: fill gaps, keep moisture at bay, and reduce air infiltration. Sealants tend to last longer, perform better, and cost more. In this brief section, we’ll look at the strengths and weaknesses of three major types of caulk.
Although caulks aren’t quite so diverse as construction adhesives, they do have varying formulations and properties. For specifics, go on-line or visit your lumberyard.
Silicones are arguably the most durable and most water resistant of any caulk. They are especially suitable for window glazing and slick bathroom and kitchen surfaces.
► Advantages: Silicones are incredibly tenacious on nonporous materials like glass, glazed ceramic tiles, and metal. There’s little shrinkage, and they can be applied at -40°F. Silicone sealants specified for metal flue pipe function at 500°F. And silicones have the best long-term flexibility, UV resistance, and weather – ability. Also, molds won’t grow on them.
► Disadvantages: Silicones are messy to work with; wear rubber gloves to protect your skin. Once silicones have cured, it’s almost impossible to remove them. Plus, they are bond breakers—that is, because nothing will stick to an area they’ve tainted, think twice about trying them on wood, concrete, or other porous surfaces they don’t adhere well to. Avoid inhaling acetoxy silicones, and don’t use them on metal because they’ll corrode it. Pure silicones can’t be painted, although siliconized acrylics can.
Polyurethanes are versatile multipurpose caulks but are not as tenacious as silicones.
► Advantages: Because they attach equally well to wood, masonry, and metal, they’re good for caulking joints where dissimilar
materials meet. Polyurethanes won’t corrode metal. They’re easy to work, though polys get pretty stiff as temperatures approach freezing. Shrinkage is negligible. They’re great for skylight flashing and metal roofs. And they can be painted. Also, they’re easier to work than silicones, even though solvent based.
► Disadvantages: Polyurethanes have poor UV resistance, though additives or painting can improve that dramatically. While they are a good all-purpose caulk, they don’t have the durability or shelf life of silicones.
Latex acrylics are a good balance of performance, price, and workability.
► Advantages: Latex acrylics are water based, hence nontoxic, largely odor free, and
very easy to apply (you can shape caulk joints with your finger). They clean up with soap and water. They adhere well to a range of materials, have good UV resistance, and can be painted. Durable once cured, they are best used in protected areas in temperate climates. They are paintable.
► Disadvantages: Expect significant shrinkage (up to 30 percent) and long curing times. Although good as bedding caulk under door or window casing, they’re iffy as exterior caulk or shower and tub caulk. Properties vary widely from product to product. Although some manufacturers tout spectacular performance specs, check out on-line contractor chat groups for real-life performance ratings.

30-lb. Live Load 10-lb. Dead Load L/360
Span (feet and inches)
2×6 2×8 2×10 2×12
Spacing on Center
or Group
|
Grade
|
12in.
|
16 in.
|
19.2 in.
|
24 in.
|
12 in.
|
16 in.
|
19.2 in.
|
24 in.
|
12 in.
|
16 in.
|
19.2 in.
|
24 in.
|
12 in.
|
16 in.
|
19.2 in.
|
24 in.
|
Douglas
|
Sel. Struc.
|
12-6
|
11-4
|
10-8
|
9-11
|
16-6
|
15-0
|
14-1
|
13-1
|
21-0
|
19-1
|
18-0
|
16-8
|
25-7
|
23-3
|
21-10
|
20-3
|
fir-
|
No. 1 & Btr
|
. 12-3
|
11-2
|
10-6
|
9-9
|
16-2
|
14-8
|
13-10
|
12-10
|
20-8
|
18-9
|
17-8
|
16-5
|
25-1
|
22-10
|
21-4
|
19-1
|
larch
|
No. 1
|
12-0
|
10-11
|
10-4
|
9-7
|
15-10
|
14-5
|
13-7
|
12-4
|
20-3
|
18-5
|
16-9
|
15-0
|
24-8
|
21-4
|
19-6
|
17-5
|
|
No. 2
|
11-10
|
10-9
|
10-1
|
9-3
|
15-7
|
14-2
|
13-0
|
11-8
|
19-10
|
17-5
|
15-11
|
14-3
|
23-4
|
20-3
|
18-6
|
16-6
|
|
No. 3
|
9-11
|
8-7
|
7-10
|
7-0
|
12-7
|
10-11
|
10-0
|
8-11
|
15-5
|
13-4
|
12-2
|
10-11
|
17-10
|
15-5
|
14-1
|
12-7
|
Douglas
|
Sel. Struc.
|
11-3
|
10-3
|
9-8
|
8-11
|
14-11
|
13-6
|
12-9
|
11-10
|
19-0
|
17-3
|
16-3
|
15-1
|
23-1
|
21-0
|
19-9
|
18-4
|
fir
|
No. 1
|
11-0
|
10-0
|
9-5
|
8-9
|
14-6
|
13-2
|
12-5
|
11-6
|
18-6
|
16-10
|
15-10
|
14-5
|
22-6
|
20-6
|
18-9
|
16-9
|
(South)
|
No. 2
|
10-9
|
9-9
|
9-2
|
8-6
|
14-2
|
12-10
|
12-1
|
11-3
|
18-0
|
16-5
|
15-5
|
13-10
|
21-11
|
19-8
|
17-11
|
16-1
|
|
No. 3
|
9-8
|
8-5
|
7-8
|
6-10
|
12-4
|
10-8
|
9-9
|
8-8
|
15-0
|
13-0
|
11-10
|
10-7
|
17-5
|
15-1
|
13-9
|
12-4
|
Hem-fir
|
Sel. Struc.
|
11-10
|
10-9
|
10-1
|
9-4
|
15-7
|
14-2
|
13-4
|
12-4
|
19-10
|
18-0
|
17-0
|
15-9
|
24-2
|
21-11
|
20-8
|
19-2
|
|
No. 1 & Btr
|
. 11-7
|
10-6
|
9-10
|
9-2
|
15-3
|
13-10
|
13-0
|
12-1
|
19-5
|
17-8
|
16-7
|
15-5
|
23-7
|
21-6
|
20-2
|
18-3
|
|
No. 1
|
11-7
|
10-6
|
9-10
|
9-2
|
15-3
|
13-10
|
13-0
|
12-1
|
19-5
|
17-8
|
16-7
|
14-10
|
23-7
|
21-1
|
19-3
|
17-2
|
|
No. 2
|
11-0
|
10-0
|
9-5
|
8-9
|
14-6
|
13-2
|
12-5
|
11-4
|
18-6
|
16-10
|
15-6
|
13-10
|
22-6
|
19-8
|
17-11
|
16-1
|
|
No. 3
|
9-8
|
8-5
|
7-8
|
6-10
|
12-4
|
10-8
|
9-9
|
8-8
|
15-0
|
13-0
|
11-10
|
10-7
|
17-5
|
15-1
|
13-9
|
12-4
|
Spruce-
|
Sel. Struc.
|
11-0
|
10-0
|
9-5
|
8-9
|
14-6
|
13-2
|
12-5
|
11-6
|
18-6
|
16-10
|
15-10
|
14-8
|
22-6
|
20-6
|
19-3
|
17-11
|
pine-fir
|
No. 1
|
10-9
|
9-9
|
9-2
|
8-6
|
14-2
|
12-10
|
12-1
|
11-3
|
18-0
|
16-5
|
15-5
|
14-1
|
21-11
|
19-11
|
18-3
|
16-3
|
(South)
|
No. 2
|
10-5
|
9-6
|
8-11
|
8-3
|
13-9
|
12-6
|
11-9
|
10-10
|
17-6
|
15-11
|
14-9
|
13-3
|
21-4
|
18-9
|
17-2
|
15-4
|
|
No. 3
|
9-3
|
8-0
|
7-3
|
6-6
|
11-8
|
10-1
|
9-3
|
8-3
|
14-3
|
12-4
|
11-3
|
10-1
|
16-6
|
14-4
|
13-1
|
11-8
|
Western
|
Sel. Struc.
|
10-9
|
9-9
|
9-2
|
8-6
|
14-2
|
12-10
|
12-1
|
11-3
|
18-0
|
16-5
|
15-5
|
14-3
|
21-11
|
19-11
|
18-6
|
16-6
|
woods
|
No. 1
|
10-5
|
9-6
|
8-11
|
8-0
|
13-9
|
12-4
|
11-4
|
10-1
|
17-5
|
15-1
|
13-10
|
12-4
|
20-3
|
17-6
|
16-0
|
14-4
|
|
No. 2
|
10-1
|
9-2
|
8-8
|
8-0
|
13-4
|
12-1
|
11-4
|
10-1
|
17-0
|
15-1
|
13-10
|
12-4
|
20-3
|
17-6
|
16-0
|
14-4
|
|
No. 3
|
8-5
|
7-3
|
6-8
|
5-11
|
10-8
|
9-3
|
8-5
|
7-6
|
13-0
|
11-3
|
10-3
|
9-2
|
15-1
|
13-1
|
11-11
|
10-8
|
* Design Criteria: Strength – 30 lbs. per sq. ft. live load, plus 10 lbs. per sq. ft. dead load. Deflection – Limited in span in inches divided by 360 for live load only. This table is used courtesy of Western Wood Products Association (www. wwpa. org) and is excerpted from Western Lumber Span Tables of Floor and Ceiling Joists and Roof Rafters. For more information about lumber grades, see pp. 47 and 48.
|