Ladders and scaffolding are essential for many painting jobs. For more on them, see Chapter 3.
MASKS AND CARTRIDGES
Disposable paper masks will keep out sanding dust, but you need a filtered mask when spraying paints or applying chemical strippers. For any task involving leaded paint, wear a full-face respirator mask with replaceable HEPA (purple) cartridges. For most paint applications, a half-face mask with replaceable organic vapor cartridges will be adequate. Masks vary, so pick one that fits your face snugly. To test the fit, when you cover cartridge openings and inhale, no air should enter the mask.
Cartridge life varies according to the chemical you’re using, the type of filter specified for that chemical, ventilation in your workspace, and the care you take to keep cartridges “alive” in storage. Change the cartridges whenever you smell fumes or whenever it becomes difficult to breath through the mask. Manufacturers suggest their own change schedules. For example, when filtering epoxy-based paints (very toxic) or urethanes, filters can become loaded in 8 hours. Whereas, filters for latex-based paints typically have a much longer change schedule—for example, 30 days or 40 working hours, whichever comes first.
BRUSHES
The bristles of high-quality brushes are flagged, meaning the bristle ends are split and of varying lengths, enabling them to hold more paint.
As you shop for brushes, pull lightly on bristles. Are they well attached to the metal ferrule on the handle? Then, when you gently press the bristles as though painting, they should spread evenly and have a springy, resilient feel. Avoid brushes with stiff bristles.
Bristle types. Bristles are either natural (hog bristles, for example) or synthetic (usually nylon). Use natural bristles for oil-based paints, varnishes, shellacs, and solvent-thinned polyurethanes. Use synthetic bristles for latexes. Nylon bristles may dissolve in oil-based paints; whereas natural bristles tend to swell and clog when used with the water-base of latex. Although some synthetic bristles work with either painting
Quality bristles fan out as you apply paint. Here, the tapered bristles of а 2’Л-іп. angled sash brush “cut" a straight edge where walls meet trim.
|
|
Heavy paper or cardboard covers help bristles keep their shape.
|
|
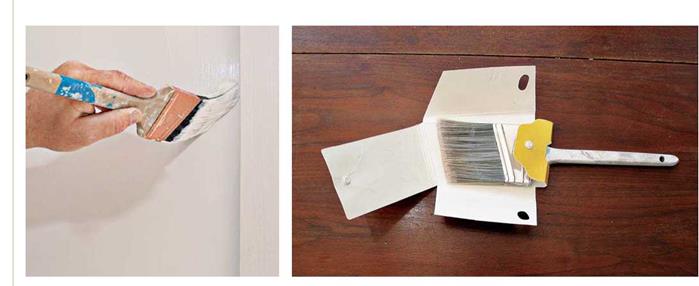
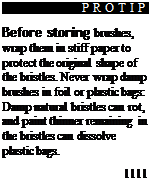
medium, once you’ve used a brush for a particular type of paint, continue using it for that type.
The width of the brush should depend on the amount of paint to be applied. Because rollers and spray guns are best for large surfaces, spend your brush money on smaller, better brushes. Many pros praise the 21/2-in. angled sash brush as the most versatile brush in their arsenal; it’s wide enough to smooth out paint on baseboard trim, yet slim enough to "cut an edge” at corners and along window casings. If you own only one brush, this should be it. But if you’ll be painting many narrow window muntins, also buy a 1 ’/2-in. sash brush.
Brush care. Brush care begins with proper use. Don’t stab bristles into tight spots. Instead, stroke the paint on. When you take a coffee break, leave a moderate amount of paint on the bristles so your bristles don’t dry out.
Clean brushes immediately after you finish painting for the day. Remove excess paint from the bristles by drawing them over a straightedge, not over the edge of the paint can. Brush the remaining paint onto old newspapers. Clean the brush in an appropriate solution: paint thinner for oil-based paints, soap and water for latexes.
Wear disposable gloves during brush cleaning, and use your fingers to work the solution into bristles and all the way to the ferrule. After giving each brush a thorough initial wash, rinse it in a fresh batch of solution. When the brushes are clean, shake and brush out the excess solution. Rinse with warm water, shake out the excess, and comb the bristles. (Solvent-cleaned brushes require an intermediate cleaning with soap and warm water.) Don’t use hot water when cleaning brushes because it splits the bristles.
ROLLERS, PANS, POLES, AND PADS
Rollers enable you to paint large areas quickly and evenly. In addition to the familiar 9-in. cylinder type, there are also 6-in. "hot-dog” rollers for tight spaces, such as inside cabinets, and beveled corner rollers that resemble a pointed wheel. There are also textured rollers, including stippled, faux finish, and distressed.
Choosing a roller cover. The surface and paint should determine the type of roller cover, also called a sleeve. For example, if you’re painting smooth walls, use a short-nap cover (/4 in. to И in.). Whereas, concrete block and stucco need a long nap (1 in. to 1й in.). Most covers are synthetic and work either with oil-based or latex paints. However, for fine finishes with glossy oil-based paints, use a fine-nap natural-fiber cover. For an ultra-smooth finish when rolling enamels, varnish, or polyurethane, use a fine-nap mohair cover.
Don’t buy cheap cardboard-backed roller covers unless you intend to paint a single room with latex and throw the cover away. (Never use cheap roller covers with oil-based paint. The oil will pluck the fibers from the cylinders and leave them sticking to your wall.) Quality roller covers have plastic sleeves that survive repeated cleanings. As you do with brushes, use a roller cover for only one type of paint, whether oil-based or latex.
Roller pans. Ramped metal or plastic roller pans are routinely sold in packages that include a roller frame and a cover or two, but pros rarely use roller pans. Occasionally, pros may use a pan to hold a small amount of paint for decorative painting. But when pros roll multiple rooms, they prefer a ramp of expanded-metal inside a 5-gal.
paint bucket about half full. This ramp gives you room to load the roller and remove excess paint quickly—so you can keep painting, rather than repeatedly filling a roller pan.
Paint pads. Pads for paint are about the size of a small kitchen sponge and have a short nap. Generally, they are used to paint hard-to-reach spots such as insides of cabinets. They’re also
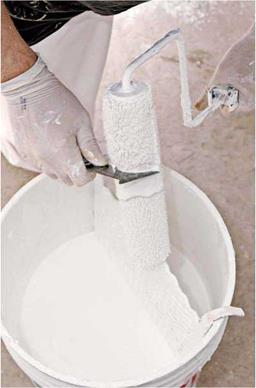
Before washing roller covers, use this painter’s 5-in-1 tool to remove the excess paint.
|
used for applying clear finishes such as polyurethanes to flat surfaces.
Extension poles. Whether sectioned or telescoping, extension poles are indispensable for reaching ceilings and upper parts of walls with rollers or pads. Because the poles tax mainly your shoulder and back, rather than your wrist and arm, they enable you to work longer with less fatigue. Another advantage: By painting with an extension pole, you don’t need to stand immediately under the drizzle, known as "paint rain.”
Roller-cover care. If you buy quality roller covers, clean them as soon as you finish a job.
For this, wear disposable gloves. Before washing a cover, use a 5-in-1 painter’s tool shown below to remove excess paint. Then slide the cover off the metal roller frame and wash the cover in the paint-appropriate cleaner, working out the paint with your gloved fingers. Repeat the procedure with fresh cleaner. Then wash with soap and water. Blot the excess moisture with a paper towel or a clean rag. Air-dry the cover by sliding it onto a hanger somewhere; don’t let it lie on its nap while drying. Store the dried cover or pad in a paper bag or foil. If a cover or pad wasn’t cleaned properly and has become crusty, throw it away.