Because humans do not have the ability to withstand the natural elements, we wear clothes and build shelters. In cold climates we heat those shelters. Many systems have been invented for heating the home, but not all systems are created equal. After examining the criteria that create health and a comfortable indoor climate, I chose to focus my career on the creation of Kachelofens, or masonry oven heating systems, because of their superior quality and performance. A Kachelofen-Masonry Heater is an individually designed, technically calculated, thermal mass wood-fired heating system.
From a Building Biology point of view, let us examine the criteria for creating a comfortable and healthy indoor environment and discover why the Masonry Heater is one of the best heating systems for meeting these criteria.
1. Type of Heat: A heating system should create radiant heat, like the heat from the sun. With a radiant heat source, the room air temperature can stay relatively low at 18 to 20 degrees Celsius (64 to 68 degrees Fahrenheit) and still be comfortably warm because, unlike the convection heat from a forced-air source, radiant
heat warms walls, floors, and ceilings as well as furniture and bodies and not the room air. Therefore the room air is barely moving, or moving only at low speed, which means no electrostatic charge, no dust circulation, and no transfer of odors. Kachelofens-Masonry Heaters release about 60 to 70 percent radiant heat and only about 30 to 40 percent convection heat, an output not attainable with any other heating system.
2. Temperature: The quality of a heating system should not be measured by high room-air temperatures but rather by low differences between the room-air temperature and the temperatures of the walls, ceilings, and floors, as shown in the sketches.
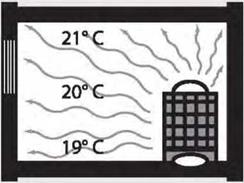
Kachelofen-Masonry Heater
|
vacuums should have true HEPA filtration or be exhausted to the outside. No chemicals shall be used in the process.
• Prior to occupancy, the air distribution system shall be tested for leakage by a qualified third party or in the presence of the owner or architect. Any leakage greater than 3 percent shall be remedied by the contractor at no additional expense to the owner.
Once the ducts are in place, a regular maintenance program is essential to maintaining a healthy system. Identify a professional maintenance company that uses high-powered duct cleaning equipment. Avoid the use of chemical cleaners.
Masonry Ovens
From a Building Biology perspective, the ideal heating system would have the following features:
• It would be a radiant source.
• It would not rob the air of negative ions. (When air is forced through metal ductwork, negative ions will be attracted to the ductwork and room air ions will be depleted.)
• The appliance would not be hot enough to fry dust.
• It would not create “temperature monotony” (having all rooms the same temperature, which Building Biology considers unhealthy) or drafts.
discharge are major irritants to mucous membranes and cause many chronic illnesses and allergies. Since the surface temperatures of Kachelofens-Masonry Heaters are below no degrees Celsius, dust circulation, combustion of dust, and electric discharge of the room air do not occur.
4. Humidity: Room air should have a relative humidity of approximately 50 to 60 percent, which can be achieved only by radiant heat. Heating systems operating with mainly convection heat will bring the relative humidity in a room down to 30 percent. To compensate, some forced-air systems have built-in humidifiers, but these can cause condensation and mold buildup in the ductwork.
5. Temperature gradients: Convection heat creates horizontal layers of air in a room, with temperature differences up to 10 degrees Celsius from floor to ceiling, resulting in hot heads and cold feet. The temperature differences in rooms with radiant heat from Kachelofens – Masonry Heaters are only 1 to 2 degrees Celsius, meaning the room is evenly heated.
6. Electromagnetic fields: Heating systems with mainly convection heat (electric and hot – water baseboard heaters and hot-water radiators) create electromagnetic fields that cause electric stress. Permanent electric stress can be the cause of illnesses. Kachelofens-Masonry Heaters do not cause electromagnetic fields or electric stress.
7. Ionization of room air: Wood fire creates a negative ionization of the room air. Why is this important? An ion has either a positive or a negative charge. We have positive and negative ions in our body, but when we run, walk, work, or just generally move we lose negative ions. We are left with positive ions, or a positive charge in our body, and we need to find a source of negative ions to balance our positive charge. Wood fire is one of the best sources to recharge our body with negative ions.
8. Noise:The only noise created by Kachelofens – Masonry Heaters is the cozy crackling of the wood fire.
9. Environmental impact: Of all heating systems, the Kachelofen-Masonry Heater has the lowest overall impact on our environment, from production of the building materials to installation, to the amount of fuel required and pollution generated, to disposal after a lifetime of at least 80 years. Unlike a woodstove, which in cold climates must burn wood constantly to heat a home, a masonry oven is fired only for a short duration, fully burning the combustion gases and storing heat in its mass walls. It therefore uses far less wood than a woodstove and creates very little pollution in the form of smoke.
A study of Kachelofens-Masonry Heaters conducted by the Technical University of Vienna showed the following:
• There would be minimal byproducts of combustion.
Wood heat distributed through a masonry oven can fulfill these criteria. The masonry oven, not to be confused with other types of “fireplaces” or woodburning stoves, is designed to burn wood so that the gases are completely combusted. The generated heat circulates through multiple chambers within the oven and is distributed into the ovens massive walls before the relatively clean and cool
Criteria
|
Ideal
|
Kachelofen
|
Room Temperature
|
18 to 20° C
|
18 to 20° C
|
Temperature gradient
|
1 to 2° C
|
2 to 4° C
|
Wall temperature
|
20 to 22° C
|
18 to 20° C
|
Humidity
|
40 to 60 %
|
40 to 60 %
|
Air movement
|
<0.1 m/s
|
<0.1 m/s
|
Dust circulation
|
no
|
low
|
Odors
|
no
|
low and pleasant
|
Ionization
|
natural
|
natural
|
Noise
|
no/pleasant
|
no/pleasant
|
Design
|
individual
|
individual
|
The Baubiologische Institut Rosenheim (Germany) graded the various heating systems based on the criteria discussed above and came up with the following results:
Forced air/fuel oil 7 points
Hot water in floor/fuel oil 19 points
Wood-fired iron stove 21 points
Kachelofen-Masonry Heater 66 points
The masonry oven and its health, comfort, and ecological benefits are little known in North America, where forced-air heating is the norm. If you are interested in heating your home in this time – tested manner you will need to seek out a mason trained in the art of masonry oven building and installation. To find a certified mason in your vicinity you can refer to the member directory of The Masonry Heater Association of North America at mha-net. org.
Ernst Kiesling, an Austrian-educated structural engineer, has had a lifelong attraction to healthy living and green building methods. He has been involved with Kachelofens-Masonry Heaters for 31 years, starting out as a teacherfor the profession at a vocational school in Austria and then going into business building individually designed Kachelofens-Masonry Heaters. After immigrating to Nova Scotia, Canada, he started Kiesling Construction Ltd. to bring the goodness of the Kachelofen – Masonry Heaterto Canada. He can be contacted at Canadian Kachelofen, ermared@ns. sympatico. ca.
exhaust goes up the chimney. Most countries in northern Europe have developed this type of heating to perfection and masonry ovens are common there. There are many masons in the US trained in the art of masonry oven building. The Masonry Heater Association of North America has an informative website that lists trained and certified heater masons by location.