Your local building code will have the final say on sizing structural panels. To accommodate heavy loads, choose a panel rated for a higher span. A span rating of 32/16 indicates that the panel is strong enough to sheathe rafters spaced 32 in. on center and studs 16 in. on center and, therefore, can support far greater live loads than a 24/16-rated panel, even though a 32/16 panel is only & in. thicker.
Nailing schedules for different uses of plywood are the same: Nail every 6 in. around the perimeter, not closer than 3з8 in. to the edge; elsewhere, nail every 12 in. For subflooring, annular ring or spiral nails hold best; use hot-dipped galvanized nails for all exterior purposes. An 8d nail is sufficient for h-in. to M-in. plywood. For
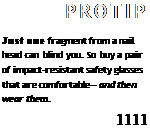
structural shear walls, follow the engineer’s specifications for nailing. Shear walls often require tighter nailing around the edges of the panel— and, sometimes, thicker nails (10d).
Leave a gap of Уи in. between sheets, for expansion; more where humidity is high. (Tongue-and-groove panels may not need gaps.) For greatest strength, run the length of a 4×8 sheet perpendicular to the structural members you are nailing to, and always stagger the butt ends of the sheets. In the intervals between framing, support plywood edges in floors and walls with solid blocking; on roofs, place blocking clips (also called ply-clips or H-clips) between the sheets’ edges unsupported by solid wood.
Pneumatic nailers (also known as nail guns) are widely used to nail down plywood, and they save a lot of time. But one thing a nailer won’t do is "suck up” a piece of plywood to framing. This is worth noting because almost all plywood is warped to some degree. So after you nail down plywood with a pneumatic nailer, go back over the surface and give each nail an additional shot with a 20-oz. framing hammer. The hammer head, being larger than the striker of the nailer, will help drive the plywood down as well.
As important, don’t drive a nail too deeply. If the nailer’s pressure is set too high, the nail may be driven through the face ply, diminishing the shear value and holding capacity of that nail.
Thus set the nailer’s pneumatic pressure a little lower than would be needed to drive the nail flush. Then finish each nail with a hammer blow.
HARDWOOD PLYWOOD
Hardwood plywood is not intended to be structural, but since you may need some during renovation, here’s a brief overview. As with softwood plywood, there’s a great variety, classified by species, face plies (appearance), core material (MDF, LVL, particleboard), and glues. The range of uses is suggested by the many thicknesses— from h6-in. aircraft plywood to 2-in. door stock.
Most hardwood plywood is used indoors, so appearance grading and careful handling are crucial. Be sure to specify the grade of both faces, and check the stock carefully for damage. Because this plywood is extremely expensive, sheets are often used right up to the edges. Thus check to ensure that edges aren’t damaged or frayed. Here’s a list of hardwood grades:
► Specialty. You can special order closely matched flitches (veneer surfaces that can be laid together in sequence) that allow repetitions of face grain for visual effect.
► Premium (A). Grain patterns and colors are matched precisely.
► Good (No. 1). Colors of matched veneers on a face do not vary greatly, but patterns are less closely matched than premium grade.
► Sound (No. 2). Although colors and patterns are not matched, there are no open flaws.
► Utility (No. 3). These may have small flaws, tight knotholes, discoloring, and splits that can be filled, but no rot.
► Backing (No. 4). Defects are allowed as long as they don’t weaken the sheet or prevent its use; the backing side may be from a different tree species than that of the exposed face.