This two-family Victorian house (circa 1860) was difficult to upgrade because we weren’t allowed to remove siding, replace the windows, or dig into the slate roof.
The historic commission did, however, allow us to remove and replace the siding and windows on one wall where the siding was damaged and needed replacement, so we injected open-cell foam, added house – wrap and furring strips, and replaced the siding on that wall.
Historic commissions all over the country favor historical authenticity over durability and energy efficiency with regard
Tar-paper baffle connects wall and roof insulation.
|
|
|
Drywall is a code-required fire block.
|
|
3/4-in. furring strips
Wood
siding
|
|
Open-cell spray foam (R-40 in the rafters; – R-14 in the walls)
|
|
|
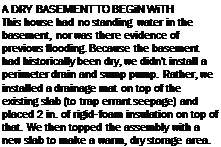

How Much Insulation Do You Need?
ecause the earth is such a great buffer to heat loss and gain, the insulation needs in a house grow as you get farther from the ground. Naturally, they’re greatest at the roof, which is baked by the sun all day and chilled by the sky at night.
We specify significantly higher levels of insulation than are required by the International Energy Conservation Code, and we think it is money well spent. When you’re attempting to approach net-zero energy use in homes, energy that isn’t used is always the cheapest energy.
R-10 under the Basement Slab
It is easy to add 2 in. or 3 in. of extruded (or expanded) polystyrene under a new slab before pouring the concrete. This could cut into headroom a bit, but the benefits outweigh the cost.
R-20 Basement Walls
Warming basement walls is often the best protection you can get from mold growth. Additional living space is an added benefit. Energy codes in most cold climates call for at least R-10, but if you can afford the additional insulation at this time, it is well worth it. Both closed-cell spray foam and rigid-foam insulation are good choices.
R-40 in the Walls
By warming above-grade walls, you eliminate chilly convection currents inside a room, which can increase your actual living space because furniture no longer needs to be moved away from exterior walls. While the building code asks for at least R-19 in most cold climates, it is worthwhile to use as much insulation as you can afford.
R-60 in the Roof
Adding insulation to the roof (rather than the attic floor) brings extra living and storage space into the home at little cost. It also reduces summer cooling loads. It’s often easy to provide more than the code minimums because of deep rafter cavities. If you’re reroofing the house, consider putting rigid-foam board insulation on top of the sheathing as we did in two of the case studies here. After judging the performance of the first two houses, we increased our recommendation from R-40 to R-60.
n— 1 ■
|
|
П.
|
■1
|
wm
Iа
1
|
І
|
|
ji
|
і
в
|
|
|
|
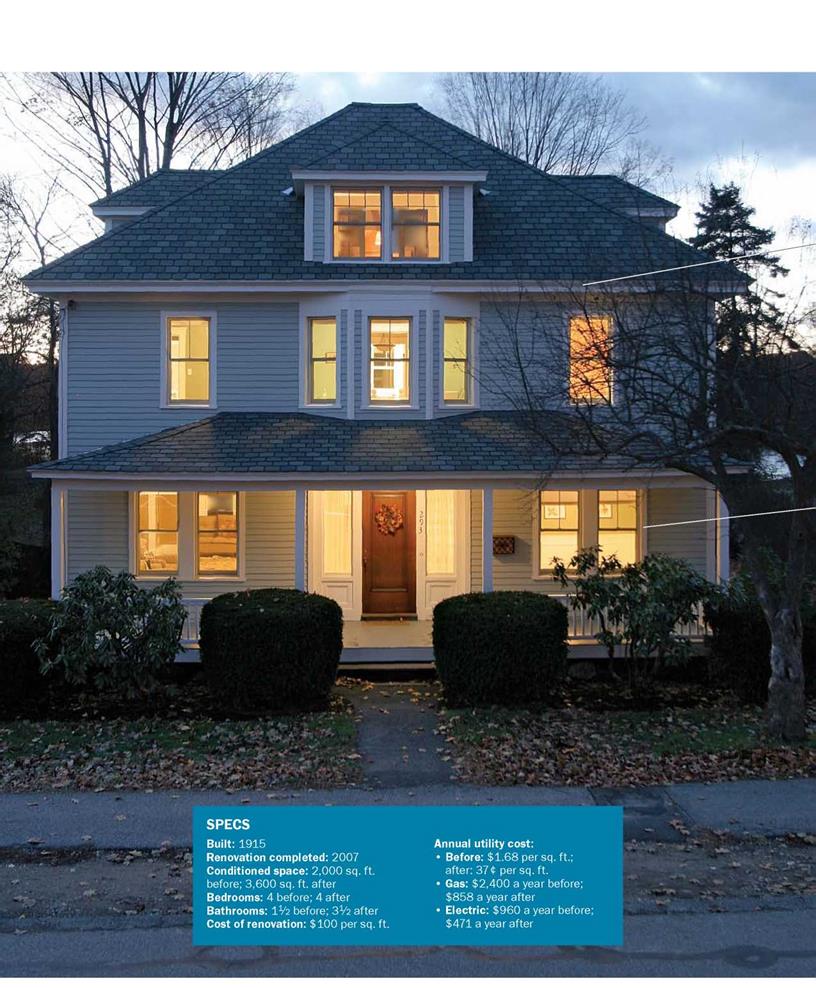
Third Time Is a Charm
This 1915 foursquare is an American classic found in almost every town in the country. Interior plaster was in great shape, the layout was excellent, and there was no structural damage to speak of. Other than adding a few new windows to the back (for better views to a pond) and updating the kitchen, we didn’t disrupt the interior too much. By insulating the basement and roof, we almost doubled the living space of this house without adding an inch to the footprint. And the utility bills were cut by 60%.
Better windows would be the next place to reduce energy loads in this house. A triple-glazed unit with heat-mirror technology might further reduce the heating load, allowing us to get closer to zero.
Betsy Pettit, FAIA, is an architect and a principal of Building Science Corp., now located in the Victorian house featured here.