Choosing a Foundation
FOUNDATION TYPES VARY by region. When deciding which type of foundation to use, consider the cost, climate, and local preferences. The three major foundation types are discussed below. |
rough or finished floor for the first level of the building. This explains why slab foundations are less expensive than other types. Because concrete has poor insulativc qualities, slab foundations are often insulated with rigid foam. Plumbing waste lines are typically cast into the slab, so thev must be carefulIv laid out 4 4 and installed first. Plumbing supply – lines and tubes for radiant floor heating can also be cast into a slab. Types of Slab Foundations Concrete slabs can be poured inside stem walls that bear on conventional footings. Another construction method is to form and pour the floor and footing together. With this type of slab, the floor is simply thickened at the perimeter of the house (and beneath any load-bearing walls or interior posts) to form the footing. As with other foundations, the footing should extend below the frost line. Crawl Space Crawl-space foundations are very compatible with affordable housing. In humid, high-moisture areas (such as the Southeast and Pacific Northwest), this type of foundation raises the living space off the ground, a wav from wet soil. A house built on floor joists over a crawl space |
SLAB WITH INTEGRAL |
PT |
sill |
4-in. (minimum) reinforced stab, continuous |
Termite shield Anchor bolt Insulation board |
Concrete Slab Slab foundations are popular throughout southern sections of the country and in regions where winter temperatures are mild. A concrete slab is more than a foundation; the slab also serves as the |
Footing Moisture extends barrier below frost line. |
4 in. (minimum) of compacted gravel |
SLAB WITH SEPARATE FOOTING & STEM WALL |
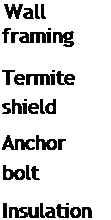
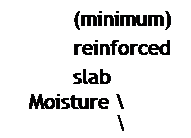
PT sill / / |
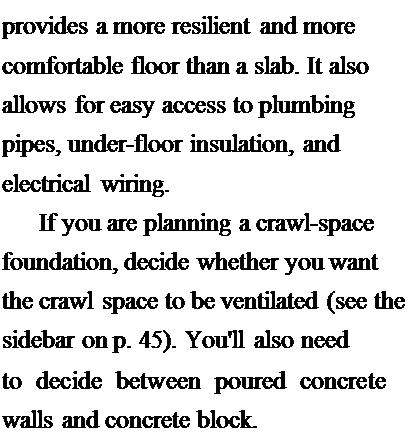
Basement Building a house on a full basement provides all the advantages of crawl space construction with the added |
4 in. (minimum) of compacted qravel under slab |
Foundation wall f Footing |
benefit of extra room below the main living area. Of course* basement foundations are more expensive than other types, and the living space they provide can be damp and lacking in natural light. To overcome these disadvantages, some basements incorporate window wells—windows located just below grade level—surrounded by a metal or concrete retaining wall on the outside of the foundation. When a basement will he used as a living space, the foundation walls must be waterproofed on the outside, insulated on the outside or on the inside, and finished on the inside. Today, many basement foundations are built with poured concrete walls. Other builders construct basement foundations with concrete block.
Concrete Block vs. Poured Concrete Walls
If you have a large crew, like we do on most Habitat projects, it makes sense to build foundation walls with concrete block. All you need are a couple of experienced masons and enough volunteers to keep them supplied with blocks and mortar as they work their way around and up, course by course. A crawl-space foundation can be completed in just a couple of days. When building walls with concrete block, it’s
easy to form beam pockets and openings for vents, doors, and windows. And by switching to a smaller block just below the planned grade level, you can create a ledge for brick veneer.
If you want a full basement and you don’t have a Habitat-size crew, poured concrete is the way to go. Most basement foundations are built with poured concrete walls that are formed and poured by foundation contractors.
This can exert tremendous pressure on a foundation. I have seen how this expansive action moves footings, cracks slabs, and causes extensive damage to a house. When builders are aware of the potential problems with day soil, they can take precautions to avoid damaging effects. (See the drainage guidelines discussed in the sidebar below.) I have worked on sites where several feet of clav soil were removed and replaced with nonexpansive soil, which was then compacted before the footings were poured.
Foam forms are worth considering
If vou haven’t done so already, take a look at the possibilities offered by insulated concrete forms (ICFs). These lightweight foam forms are easv to handle and assemble, and they stay in place to provide wall insulation after the foundation wall is poured (see the sidebar on the facing page). With an ICT system, laying up foundation walls doesn’t demand back-breaking labor. Even so, many homebuilders still prefer to hire a foundation contractor to take on this phase of the construe-