The Affordable Housing Demonstrations show that active participation by local government is essential in encouraging the production of housing at prices opening the market to those needing housing. In establishing a climate supporting the production of affordable housing, local government must:
• Support the concept and specific activities at the highest levels, including elected officials and the principal executives of the participating agencies. Only their active advocacy of the program concepts and their direction to subordinate staff will assure that the message gets to the people who actually administer the various affected programs.
• Reach out to the local home building community, and respond to any overtures from these builders to develop the mutual trust and activities needed to identify old problems, and resolve them.
• Establish contacts with the opinion makers of the community to keep them informed of the goals of affordable housing and the steps being taken to encourage its development.
• Commit itself for the long haul, and assure that there is continuity of interest and action, even through administration changes. Affordable. housing must be a community effort, not just a current "buzz word" to be discarded when fashions change.
• Be willing to evaluate the results of housing projects using affordable housing principles, and to make changes in codes, regulations, and procedures which are suggested by successful projects.
This Chapter will focus on two areas of local government involvement – zoning and subdivision ordinance requirements, and administrative procedures. Details of local government participation in such areas as site planning, streets and rights-of-way, utilities, and stormwater systems are provided in ensuing sections.
Land use is regulated through zoning and subdivision ordinances. In general, zoning ordinances create the broad outlines of such regulation, while more detailed matters are dealt with through subdivision ordinances. Exceptions to zoning ordinances usually require substantial formal procedures, including a public hearing process. By contrast, variances in
subdivision ordinances are often granted by less formal administrative procedures. The actual coverage of the two types of regulation varies from community to community, so that a matter covered in one community by its zoning ordinance may be consigned in another community to subdivision regulation.
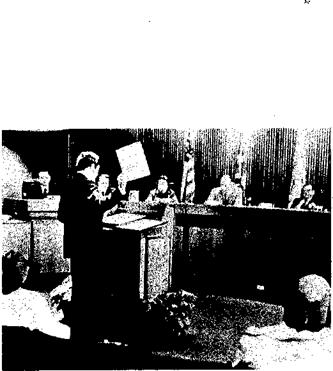
Land values are a central component of housing cost. The relationship of zoning to land value and to housing cost is direct. A recent Urban Land Institute study of the relationship between zoning restrictions and average lot prices showed that in the ten cities rated most restrictive by the Institute in their zoning requirements, the average lot price in 1980 was $24,037. In the ten cities rated least restrictive, the average lot price in 1980 was $14,688.
The reason for this relationship is clear. Restrictive zoning and/or subdivision practices reduce the total supply of land available for housing. When buildable land becomes scarce, one must pay inflated prices for it. Increasingly, persons of moderate means can no longer afford to buy at all.
A key finding that emerged from virtually every project in the JVAH program is that improved zoning and subdivision procedures promote affordable housing. The projects demonstrated conclusively that review and revision of zoning and/or subdivision ordinance requirements to make more effective use of land can bring the cost of housing down. Local governments should:
• Consider the Planned Unit Development (PUD) approach to residential zoning and/ or subdivision regulation described below. Identify specific sites throughout the jurisdiction for this designation.



PLAY ■ FIELDS
• Revise zoning codes and/or sub
division regulations to reduce the land area requirements for Planned Unit Developments, thereby fostering their use. ,
• Conduct a broad general review of zoning and/or subdivision requirements, particularly those that have been in effect for a substantial period of time. Consider revisions that will allow for moderate increases in residential density to accommodate contemporary market conditions. Such modifications can be directed toward the provision of as much land as possible in various density categories, to minimize the impact of land shortage on land prices.
• When and where possible, employ performance standards rather than uniform or arbitrary measurements, as the criteria for zoning and/or subdivision requirements. Performance standards are directed toward matching zoning with the best possible use of the site and its particular features, and employ flexible criteria to achieve this goal.
“The use of performance zoning, or a negotiated approach to land development, allows the most effective balancing of environmental quality against affordable residential construction,” according to state and local planners surveyed by the National Institute of Building Sciences (NIBS).
• Adopt zoning-and/or subdivision regulations that provide an allowance for increased density in exchange for a developer’s commitment to provide open space, landscaping, and other amenities on the proposed development site.
• Increase zoning and/or subdivision flexibility for mixed use development, thereby allowing various _ types of housing, various densities, and in some instances a mixture of residential and light commercial use in areas now covered by less flexible criteria.
•
Allow construction with little or no setback from property lines. Often called zero-lot-line zoning, this type of construction is described in an ensuing section on site planning. It allows the construction of houses on or very close to the property line on one or two sides of small lots, making the available land on such lots more attractive and usable.
• Give favorable consideration to density transfers, particularly on neighboring or contiguous parcels of land in which developers are allowed to exchange lower density rights on one tract for higher density rights on the other tract.
• Allow zoning and/or subdivision variances to build on lots that are currently below the specified minimum size for their locales, and to divide large lots that currently have excess space.
• Consider offering bonus points for affordability to builders who price quality homes below a specified cost that reflects median local prices of comparable housing. The bonus points could be applied to items such as higher density, elimination of sidewalks, reductions of setbacks, and other changes that will reduce the builders’ cost.
In the late 1950s and 1960s home builders and public officials began to use an approach to zoning and subdivision regulation called Planned Unit Development (PUD), also called Planned Residential Development (PRD), Comprehensive Residential Development (CRD), or Community Unit Plan (CUP). Projects developed under this concept usually incorporate a variety of housing types and land uses, higher density, and open space and common land managed by a community association.
PUD land use is characterized by flexibility, and encourages both public and private innovation to a greater extent than is true of more traditional zoning and subdivision controls. On one hand, this flexibility makes it possible for the developer to change long-term development plans to meet current market demands. On the other hand, it gives local authorities the latitude to negotiate with the developer, trading concessions on density, mixed use, and requirements for streets and utilities, for desired _ amenities, open space, and recreational facilities, for example.