Numerous drainage products are available in steel with protective coatings and in aluminum. These include corrugated pipe, spiral-rib pipe, structural-plate pipe, box culverts, and, where a tunnel is required, tunnel liner plates. Figure 5.24 shows the variety of profiles available for the wall cross-section of steel drainage products. For additional profiles, see “Corrugated Steel Pipe Design Manual,” National Corrugated Steel Pipe Association, 2008. The arc-and-tangent profiles shown with depths of through 1 in (6.5 through 25 mm) are wall profiles for pipe factory-corrugated to the full pipe
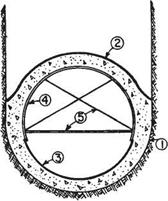
FIGURE 5.23 Cross-section of cast-in-place concrete pipe showing form components. (From Lynch Manual, Cast-in-Place Concrete Process, W. M. Lynch Co., Dixon, Calif., 1990, with permission)
|
cross-section. The 2-in-deep (51-mm) profile, which is used for structural-plate pipe and box culverts, is corrugated and curved into arc segments that can be bolted together in the field. The 552-in-deep (140-mm) profile is a similar product used for longer-span structures. The 54- and 1-in-deep (19- and 25-mm) rectangular profiles are for factory-corrugated spiral-rib pipe. Figure 5.25 illustrates the shapes of the products, the range of sizes available in steel, and common uses. Some corrugation profiles and size ranges vary for aluminum products. The larger sizes of structural-plate products and box culverts in steel or aluminum are often used as replacements for short-span bridges. Factory-made box culverts are available in spans up to 26 ft (7.8 m) and even longer with special designs.
Corrugated Steel. Most of the metal pipes used are corrugated from coils of coated sheet steel. Coatings, which are applied by the continuous hot-dip process in the production of the steel coil, include zinc (galvanizing) and aluminum. In addition, coils are available precoated with a polymer (on one or both sides) to provide extra protection against corrosion and/or abrasion. Most corrugated pipes have a continuous helical lockseam, but some manufacturers use a continuous helical welded seam, or a longitudinal riveted or spot-welded seam. Wall profiles from 1/2 X ^4 in (38 X 6.5 mm) to 5 X 1 in (125 X 25 mm) are factory-corrugated to the full pipe cross-section. The pipe is furnished in lengths (typically 20 ft or 6 m) and joined in the field by coupling bands. Diameters through 120 in (3000 mm) are available, depending on the wall profile. Pipe-arch shapes for installations with low cover are formed to shape from lengths of round pipe.
Corrugated Aluminum. Corrugated aluminum pipe is usually furnished with one of the following wall profiles: 152 X 34 in (38 X 6.5 mm), 253 X 52 in (68 X 13 mm), or 3 X 1 in (75 X 25 mm). The pipe may have a helical lockseam or a riveted seam. It is furnished in lengths similar to steel pipe and joined in the field by coupling bands. Diameters through 120 in (3000 mm) are available, depending on the wall profile, and pipe-arch shapes are formed to shape from lengths of round pipe.
Spiral-Rib Pipe. This is a newer type of steel pipe that is helically corrugated to the rectangular profiles shown in Fig. 5.24. The cross-section profile has been developed so
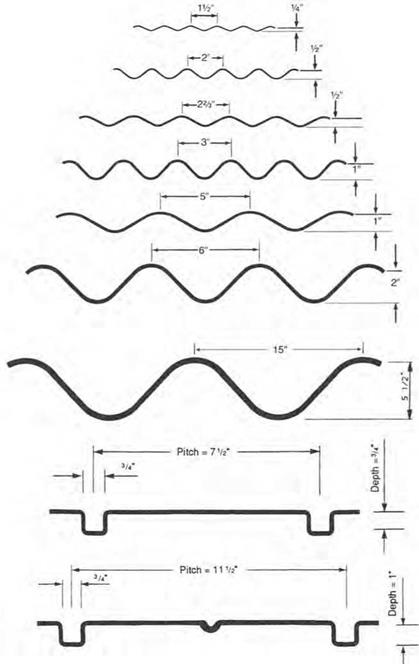
FIGURE 5.24 Profiles for corrugated steel pipe and spiral-rib pipe. Conversion: 1 in = 25.4 mm. (From Handbook of Steel Drainage and Highway Construction Products, American Iron and Steel Institute, 1994, with permission)
|
Shape
|
Range of Sizes
|
Common Uses
|
Round
|
©
|
|
6 in.-26 ft (150 mm-7.9 m)
|
Culverts, subdrains, sewers, service tunnels, etc. All plates same radius. For medium and high fills (or trenches).
|
Vertical ellipse 5% nominal
|
0
|
4-21 ft (1.2-6.4 m) nominal: before elongating
|
Culverts, sewers, service tunnels, recovery tunnels Plates of varying radii, shop fabrication. For appearance and where backfill compaction is only moderate
|
Pipe-arch
|
/ґ
Span
|
~T
Rise
LL
|
Span x Rise 17 in. x 13 in. (430 x 330 mm) to
20 ft 7 in. x 13 ft 2 in.
(6270 x 4010 mm)
|
Where headroom is limited. Has hydraulic advantages at low flows. Corner plate radius, 18 in (457 mm) or 31 in (787 mm) for structural plate.
|
Underpass’
|
P
l-Span-n
|
1
Rise
*
|
Span » Rise 5 ft 8 in x 5 ft 9 into
20 ft 4 in x 17 ft 9 in.
|
For pedestrians, livestock or vehicles (structural plate)
|
. . Rise Arch ( Г
1-—Span -|
|
Span x Rise 6 ft x 1 ft 91/2 in. (1.8 x 0.55 m) to
25 ft x 12 ft 6 in. (7.6 x 3.8 m)
|
For low clearance large waterway opening. and aesthetics (structural olate)
|
Horizontal / Ellipse P
|
— Span—>
|
|
Span 7-40 ft (2.1-12 m)
|
Culverts, grade separations, storm sewers, tunnels.
|
Pear
|
0 —Span —
|
|
Span 25-30 ft (7.6-9.1 m)
|
Grade separations, culverts, storm sewers, tunnels.
|
High Profile i Arch
|
______________ l
— Span —-
|
|
Span 20-45 ft (6.1-14 m)
|
Culverts, grade separations storm sewers, tunnels Ammunition magazines, earth covered storage.
|
Low Profile / Arch 4
|
■ Span ■
|
|r
|
Span 20-50 ft
(6.1-15 m)
|
Low-Wide waterway enclosures, culverts, storm sewers.
|
Во» Culverts
|
cn
– Span —4
|
|
Span 8-26 ft (2.4-7.9 m)
|
Low-wide waterway enclosures, culverts, storm sewers
|
Specials
|
Various
|
For lining old structures or other special purposes. Special fabrication.
|
‘For equal area or clearance, the round snape is generally more economical and simpler to assemble
|
FIGURE 5.25 Shapes, range of sizes, and common uses of corrugated steel drainage products. Conversions: 1 in = 25.4 mm, 1 ft = 0.305 m. (From Handbook of Steel Drainage and Highway Construction Products, American Iron and Steel Institute, 1994, with permission)
|
that flow characteristics are similar to that of a smooth-walled pipe. It is available in either coated steel or aluminum, as either round pipe through 108-in (2700-mm) diameter, or as pipe-arch.
Structural-Plate Pipe. This product type is available in either zinc-coated steel or aluminum.
Steel. The 6- X 2-in (152- X 51-mm) profile used for structural-plate pipe and box culverts is corrugated and curved into arc segments. The segments provide an arc length of up to about 86 in (2184 mm), in lengths of 10 or 12 ft (3.0 to 3.7 m). The segments are joined together with high-strength bolts in a sequential manner during construction. All of the shapes illustrated in Fig. 5.25 can be constructed with this product. The 15- X 5L-in (381- X 140-mm) profile can be used for the larger structures. With spans up to about 50 ft (15 m), structural-plate structures can provide an economical alternative for replacing short-span bridges. Field coatings can be applied to enhance durability.
Aluminum. The 9-in-wide (230-mm) by 2i2-in-deep (64-mm) profile is used for the aluminum structural-plate pipe and box culvert structures. Product characteristics are generally similar to those of the steel product.
Long-Span Structures. Long-span structural-plate structures are defined as having either special shapes that involve a relatively large radius in the crown or side plates, or a span that exceeds certain structural design criteria as specified in AASHTO Standard Specifications for Highway Bridges. These structures generally have spans in the range of 20 to 50 ft (6 to 15 m). They are advantageous where headroom is restricted and can often provide the required waterway area at a lower cost than building a short-span bridge. Long-span structures are made up of a structural-plate barrel of coated steel or aluminum and integral special features that enable the structure to reach long spans. Special features include either (1) continuous longitudinal stiffeners of metal and/or reinforced concrete attached to the plates at the sides of the top arc, or (2) circumferential reinforcing ribs curved from structural shapes and attached to the plates to provide additional stiffness. Typical sections of each are illustrated in Fig. 5.26. They may be constructed to most of the shapes shown in Fig. 5.25 except box culverts.
Box Culverts. This product type is available in either zinc-coated steel or aluminum.
Steel. Box culverts are available in three types, including (1) 6- X 2-in (152- X 51-mm) corrugated plate shell with 6- X 3-in (152- X 76-mm) corrugated rib stiffeners (inside, outside, or both), (2) 6- X 2-in (152- X 51-mm) corrugated plate shell with 3- X 5-in (76- X 127-mm) hot rolled angle rib stiffeners, and (3) 15- X 5.5-in (381- X 140-mm) corrugated plate shell without stiffeners. Sizes range as shown in Fig. 5.25. The structures usually have an open bottom and are supported on a base channel or corrugated footing pads, on either a concrete footing or compacted soil, depending on size and other factors. They are also available with full invert plates.
Aluminum. Box culverts have a 9- X 2i2-in (230- X 64-mm) corrugated shell plate with extruded bulb angle rib stiffeners. Size ranges are similar to those for steel box culverts. Figure 5.27 shows a typical section and rib cross-sections. Stronger ribs, including a box-section rib, are available.
Tunnel Liners. Tunnel liners are press-formed from steel in an arc segment 16 or 18 in (400 or 450 mm) long. A corrugated profile is pressed in to make the wall crosssection, and flanges are formed on the sides. Two styles are available: (1) two-flange plates that are bolted through the flanges on the two longitudinal sides and lap-bolted
Concrete Thrust Beam
Thrust Beam to be made integral with Headwall
Span
Structural member attached to structural
plate corrugation
Staggered joints except at radius change
Span
FIGURE 5.26 Typical sections of long-span structural-plate structures. (a) Longitudinally stiffened with concrete thrust beam. (b) Transversely stiffened with structural members. (From Highway Design Manual, California Department of Transportation, with permission)
on the other two sides, and (2) four-flange plates that are bolted together through flanges on all four sides. Installation and assembly can be done entirely from the inside as the tunnel is constructed. The assembled liner plates may then act as a temporary structure that is lined by concrete, or may act alone as a permanent conduit. In addition to tunneling, the liner plates can be used in rehabilitation work, such as for lining a deteriorated culvert.
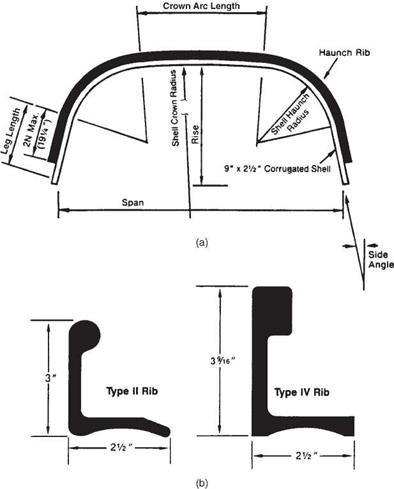
FIGURE 5.27 Corrugated aluminum box culvert. (a) Typical cross-section. (b) Details of stiffening ribs. Conversion: 1 in = 25.4 mm. (From Aluminum Box Culverts, Contech Construction Products, with permission)
|
5.6.2 Plastic Pipe
Both high-density polyethylene (HDPE) and polyvinyl chloride (PVC) are used for drainage pipe. HDPE pipe may be single-wall corrugated, smooth-wall (double-wall), or ribbed. Common diameters are 4 to 24 in (100 to 600 mm) for single wall, 4 to 60 in (100 to 1500 mm) for double wall, and 18 to 96 in (450 to 2400 mm) for ribbed pipe. Single-wall pipe has a deep corrugation, whereas a smooth internal liner is added for doublewall pipe. Wall profile details vary with the manufacturer. PVC pipe may be either smooth-wall or ribbed, with diameters ranging up to 54 in (1350 mm). Plastic pipe is furnished in lengths (typically about 20 ft (6 m) for HDPE and 13 ft (4 m) for PVC) and joined in the field by coupling bands. It is available only as round pipe.