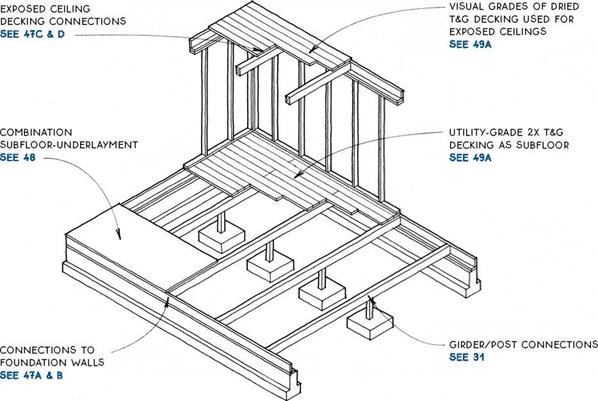
Girder systems may be designed with either dimension or laminated lumber. They are most common in the Northwest, where dimension timber is plentiful. Girder floor systems are similar to joist floor systems except that girders, which are wider than joists, can carry a greater load for a given span and therefore can be spaced at wider intervals than joists. Girders are typically placed on 48-in. centers, so long-spanning subfloor materials such as 2-in. T&G decking or lVs-in. combination subfloor-underlayment are required (see 48).
When used over crawl spaces, girders may be supported directly on posts. Over a basement, a girder system may be supported on posts or may bear on a wall or a beam like a joist system. At upper floor levels, girder systems are often used in conjunction with an
GIRDER SPANS
Size, species, grade, and spacing
|
Span (ft.)
|
4 x 6 Douglas-fir #2 @48 in. o. c.
|
8.6
|
4 x 8 Douglas-fir #2 @48 in. o. c.
|
11.3
|
4 x 10 Douglas-fir #2 @48 in. o. c.
|
14.4
|
4 x 12 Douglas-fir #2 @48 in. o. c.
|
17.6
|
|
exposed T&G decking ceiling. These exposed ceilings can make wiring, plumbing, and ductwork difficult.
This table assumes a 40-psf live load, a 10-psf dead load, and a deflection of L/360. The table is for estimating purposes only. No. 2 Douglas-fir is most prevalent in regions where girder systems are most frequently used.
) GIRDER-FLOOR SYSTEMS
FRAMED WALL
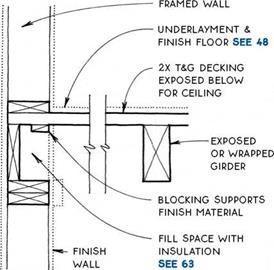
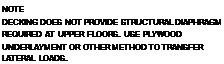

UNDERLAYMENT &
FiNiSH FLOOR SEE 48
2X T&G DECKiNG EXPOSED BELow
for ceiling
exposed or wrapped girder
blocking applied between and to sides of girders supports WALL finish.
note
2X T&G decking may BE SANDED To МАКе FiNiSH floor, but this is advisable only with very dry decking. dust filtration from upper to lower floor & sound transmission between floors MAY occur with THIS DETAIL.

cally plywood, particleboard, or hardboard.
TECHNICAL
INFORMATION
SUBFLOORING & UNDERLAYMENT
Plywood & Non-Veneered Panels
Typical T&G Decking Sections


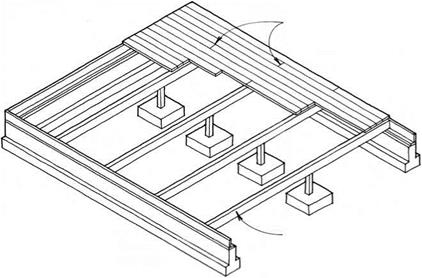
2X6 v-JOINT IS MOST.
commonly used ON
upper FLOORS TO MAKE EXpOSED
ceilings below. most species
WILL SpAN 4 FT.
2X8 uTILITY IS
used primarily as subfloor over crawl spaces
OR BASEMENTS & IS OFTEN INSTALLED GREEN. IT WILL SpAN 4 FT. IN MOST FLOOR SITuATIONS.
3X AND 4X LAMINATED IS uSED MOSTLY AT ROOFS TO MAKE EXpOSED cEILINGS BELOW, BuT ALSO AS FLOORING.
decking is end matched FOR random-length application & IS available pREFINISHED IN 3X6, 3X8, 4X6, & 4X8 sizes. IT SpANS up TO 14 FT. FOR RESIDENTIAL FLOOR LOADS.


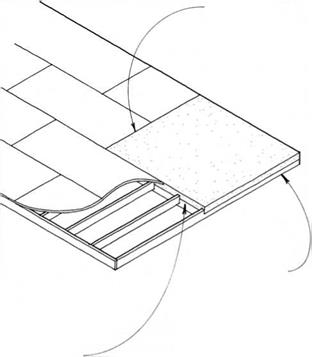
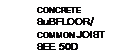

A small part of the subfloor may need to be concrete to support tiles or for a passive-solar mass floor at a south edge. The structure under the concrete must be lowered in order to accommodate the extra thickness of the concrete, typically 2Yi in. to 3 in. Use plywood that is rated to cany the load of wet concrete, usually 3/4 in. (min.).
In the case of a tiled floor, the complications of adjusting the structure to accommodate a thick concrete subfloor may be avoided by using a Vw in. thick glass-fiber-reinforced cement board over the surface of the typical wood subfloor. Check with the tile manufacturer for recommendations.
concrete
SuBFLOOR/HEADER
JOIST
SEE 51A & B
|
|
NOTE:
FOR THIN-MASS FLOORS SEE 510 & D
|
|
|



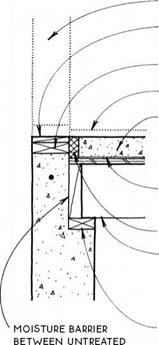
FRAMED WALL
FURRiNG SAME THiCKNESS AS WOOD SUBFLOOR
P. T. MUDSiLL
FiNiSH Floor
concrete subfloor ON
3A-iN. PLYWOOD BASE; LEVEL AND THiCKNESS VARY WiTH FiNiSH MATERiAL.
30-LB. FELT OR OTHER MOiSTURE BARRiER
iNSULATiON
JOiSTS BEAR ON LEDGE iN FOUNDATiON WALL OR ON LEDGER OR PONY WALL SEE 12D
FURRiNG SAME THiCKNESS AS WOOD SUBFLOOR
DOUBLE RiM JOiSTS FiNiSH FLOOR
CONCRETE SUBFLOOR ON 3A-IN. PLYWOOD BASE;
LEVEL AND THiCKNESS VARY WiTH FiNiSH MATERiAL.
30-LB. FELT OR OTHER MOiSTURE BARRiER
JOiSTS HUNG FROM P. T. HEADER JOiST RiPPED TO BEAR ON FOUNDATiON WALL.
SPACER BLOCKS AT 16 iN. O. C.
MOiSTURE BARRiER BETWEEN UNTREATED JOiSTS & FOUNDATiON
insulation

CONCRETE SUBFLOOR AT EXTERIOR
Full-Depth Joists below Mudsill
CONCRETE SUBFLOOR AT EXTERIOR
Full-Depth Joists/Alternative
NOTE
FOR CONDITION AT EXTERIOR WALL SEE 50A & B.
|
|
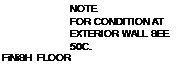 |
|
FURRiNG SAME THiCKNESS AS WOOD SUBFLOOR
FURRiNG
FiNiSH FLOOR
CONCRETE SUBFLOOR ON 3A-1N. PLYWOOD BASE;
LEVEL AND THiCKNESS VARY WiTH FiNiSH MATERiAL.
30-LB. FELT OR OTHER MOiSTURE BARRiER
JOiSTS CUT OR SIZED DOWN TO ACCOMMODATE DEPTH OF CONCRETE SUBFLOOR
INSULATION
|
|
PLYWOOD OR OTHER WOOD SUBFLOOR
TYPICAL JOiSTS
|
|
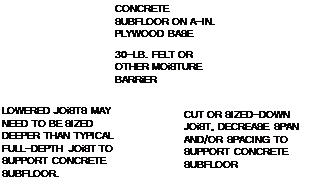 |
NOTE
DECREASE SPAN AND/OR SPACING OF SIZED-DOWN JOiSTS SUPPORTING CONCRETE.
|
|
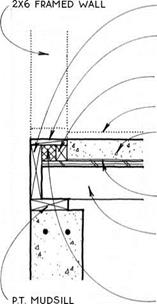

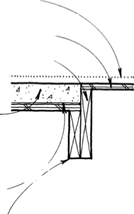

CONCRETE SUBFLOOR AT EXTERIOR
Cut-Down Joists on Mudsill
CONCRETE SUBFLOOR AT INTERIOR
Edge Parallel to Joists/2 Details
NOTE
FOR CONDiTiON AT EXTERiOR WALL SEE 50A OR B.
|
|
FiNiSH FLOOR
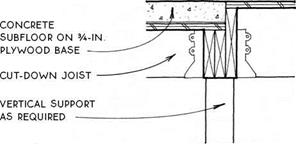
|
|
 |
|
FiNiSH FLOOR
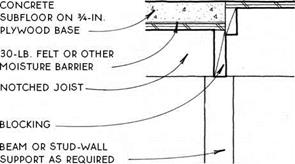
|
|
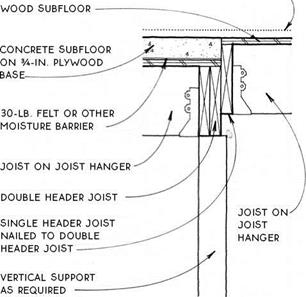

д) CONCRETE SUBFLOOR AT INTERIOR
Edge Perpendicular to Joists
CONCRETE SUBFLOOR AT INTERIOR
Edge Perpendicular to Joists: Alternative Details
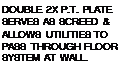
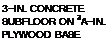
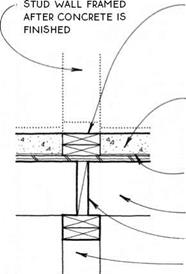
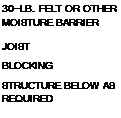
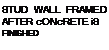
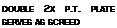
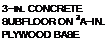
30-LB. FELT OR OTHER MOISTURE BARRIER
JOIST
P. T. MUDSILL (OR TOP PLATE IF THIN-MASS SUBFLOOR IS AT UPPER STORY)
NOTE
THIS DETAIL IS USED TO PROVIDE MASS TO A LARGE AREA OF FLOOR FOR SOLAR GAIN.
NOTE
IF THE CONCRETE IS TO BE EXPOSED, THE DOUBLE PLATE MAY BE OMITTED FOR EASE OF TROWELING. THE STUD WALL MAY THEN BE SHOT TO CONCRETE SEE 24C
THIN-MASS SUBFLOOR
THIN-MASS SUBFLOOR
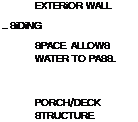
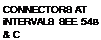
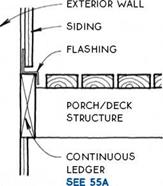
Porches and decks are traditional and useful additions to wood-frame structures. They provide a transition between indoors and out, allowing people to pause upon entering or leaving, and they extend the building to include the out-of-doors. Porch and deck floors must be constructed differently from interior floors in order to withstand the weather. The connection between porch and deck floors and the building itself is especially critical in keeping moisture out of the main structure. Because of constant exposure to the weather, this connection must be detailed in such a way that it can be repaired or replaced.
The floors of porches and decks can be grouped into two major types: those that are waterproof and thus act as a roof protecting the area below, and those that are open and allow water to pass through.
Waterproof
Porch/Deck
Floor
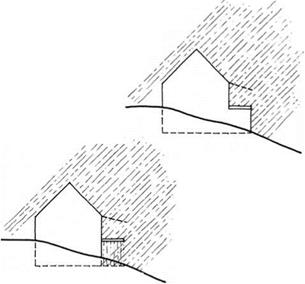
Open
Porch/Deck
Floor
|
Waterproof porch—A waterproof porch or deck floor can be treated like a flat roof. As shown in the drawing below, flashing (or the roofing material itself) must be tucked under the siding to catch water running down the side of the building, and the floor (roof) surface must be sloped away from the building (see 56A). The framing for waterproof decks over living spaces needs proper ventilation (see 205A).
Open porch—In an
open porch or deck floor, the parts that connect it to the main structure are exposed to the weather, yet need to penetrate the skin of the wall. This connection can be accomplished by keeping the porch/ deck structure away from the exterior wall and attaching it only at intervals with spaced connectors (see 54B & C).
Alternatively, a continuous ledger may be bolted to the wall and flashed (see 55A & B).
(g) PORCHES & DECKS

Porches and decks are exposed directly to the weather in ways that the main part of the structure is not. Consequently, the wood used in porches and decks is much more susceptible to expansion and contraction, twisting, checking, and rotting. A special strategy for building porches and decks is therefore appropriate.
Weather resistance – Elements of porches and decks that are likely to get wet should be constructed of weather-resistant materials. Virtually all the material required to make a new porch or deck is now available in pressure-treated lumber. Weather-resistant woods like cedar or redwood are also appropriate.
Connectors – At least once a year, joints that are exposed to the weather will shrink and swell, causing nails to withdraw and joints to weaken. Joints made with screws or bolts will therefore outlast those made with nails. For joist connections, use joist hangers or angle clips.
Joist hangers are made of galvanized steel, which should not be adversely affected by exposure to the weather. Galvanized steel deteriorates relatively quickly, however, when combined with pressure – treated lumber, especially when moisture is added to the mix. Therefore, always use connectors with the longer-lasting hot-dip galvanized finish. Also, consider the use of weather-resistant wood species for use with galvanized hangers.
Fasteners such as nails and deck screws should be galvanized. Stainless steel screws are also available and will give the longest life.
Framing—Areas between adjacent wood members collect moisture and are especially prone to rot. Even pressure-treated lumber can rot in this situation. Avoid doubling up members in exposed situations. It is better to use a single large timber where extra strength is required, as shown in the drawing at right.
Where wood must touch another surface, make the area of contact as small as possible and allow for air circulation around the joint.
Wood decking—Because decking is oriented horizontally, it has a relatively large exposed surface to collect and absorb moisture. This moisture will tend to make the decking cup. Most references suggest installing flat – grain wood decking (and rail caps) with the bark side down because boards will cup in the right direction to shed water as they season.
Unseasoned (wet) Seasoned (dry) Wet
However, if dry (seasoned) decking is installed with the bark side down, the boards will cup in the wrong direction when they get wet. Therefore, dry decking boards should be installed with the bark side up so that the boards will shed water if they cup.

Seasoned Wet
|
Synthetic decking—There is a new generation of synthetic decking made of reclaimed hardwood and recycled plastic. This material holds up in exposed conditions, is not harmed by rot or insects, and is extremely consistent and stable. The decking is not as stiff as sawn lumber, so it requires closer joist spacing. It can be fastened to framing with conventional methods and is available in standard sizes from 1×6 to 2×8.
Because the decking does not absorb water, thermal expansion is more of a concern than warping or cupping. The decking requires no sealers or preservatives and is manufactured with a nonskid surface. It is disposable (no toxins).
Painting—Sealers and preservatives will extend the life of porches and decks. Special attention should be given to end grain and to areas likely to hold moisture. Stains will outlast paints. Special porch and deck paints are available for use where exposure to the weather is not severe.
@ PORCH & DECK CONSTRUCTION
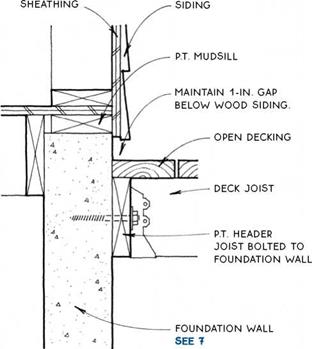
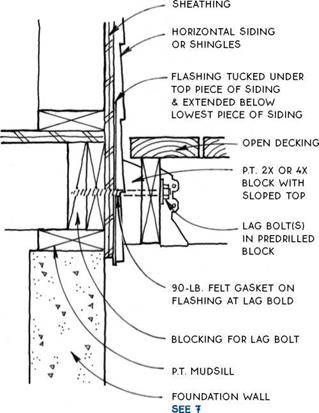

(g) OPEN DECK/FOUNDATION WALL
pN OPEN DECK/WOOD WALL
Floor : Horizontal Siding or Shingles
NOTES
FLASHiNG EXTENDS 8-iN. MiNiMUM PAST BOTH SiDES OF BLOCK SPACERS.
iNSTALL Spacer BLocKS SiMULTANEOUSLУ with SiDiNG & FLASHING, Then iNSTALL Deck.
opEN DEcKiNG LAID DiAGONALLУ AcRoSS JoiST sysTEM acts as a DiAPHRAGM, wHicH мау eliminate the need for bracing porch supports.
DETAILS show level of DEcK SLiGHTLy BELow level of FiNiSH floor. iN SNow couNTRy, adjust deck level and flashing height to account for snow buildup.
spaced decking is often used for the floor of a screened porch. in this case, the decking must be installed over insect screening.
OPEN DECK/WOOD WALL
2nd Floor: Horizontal Siding or Shingles
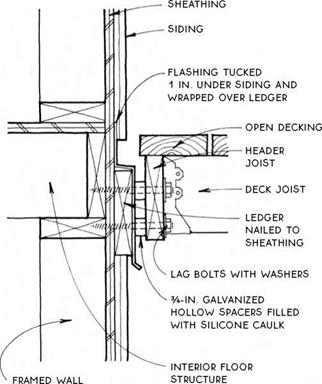
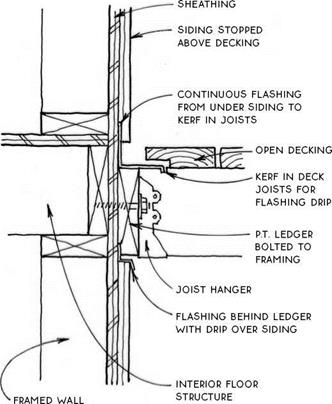
(g) OPEN DECK/WOOD WALL
OPEN DECK/WOOD WALL
Alternative Detail
OPEN RAiLiNG BOLTED TO JOiSTS OR AS EXTENSiON OF VERTiCAL SUPPORT SEE 59A
|
|
SOLID RAILING Of STuDS & SIDING SEE 55A
|
|
|
|
DEcK JOiST
supported ву
JOiST HANGER ON HEADER JOiST
|
|
DECK JOiST SUPPORTED ВУ JOiST HANGER ON HEADER JOiST
|
|
HEADER JOiST BOLTED TO STuDS
|
|
HEADER JOIST SCREWED OR BOLTED TO VERTICAL SUPPORTS
|
|
FLASHING TucKED 1 in. under SIDING AND BEHIND HEADER JOiST
|
|
|
stud wall, wood
POST, OR Other
vertical support
|
|
stud WALL, WOOD POST, OR OTHER
vertical support
|
|

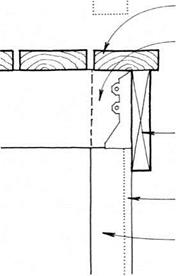
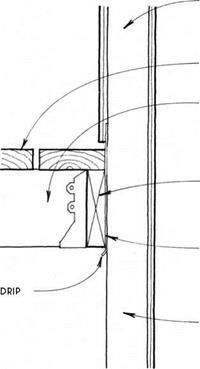
OPEN DECK/OPEN RAILING
OPEN DECK/SOLID RAILING
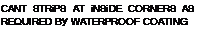

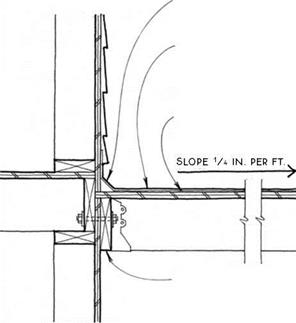
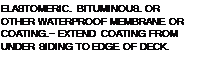
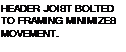
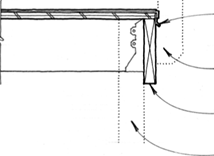


NOTES
WATERPROOFiNG CAN BE PROTECTED FROM ABRASiON ВУ ADDiTiON OF WOOD OR CONCRETE-PAVER SURFACE, SEE 57A, в & C
slope may BE ACHiEvED By SLOpING JOiSTS OR,
where a level surface is required below, ву ripping joists or adding furring strips.
EDGE flashing WITH DRip extends 4 in. under waterproofing.
attachment of railings see 58 & 59
rim joist deeper than
DECK JOISTS TO FORM DRip
stud wall, WOOD post, OR other vertical support
NOTE
if rail is solid, slope
CONCRETE TO SCuppERS FROM ALL DIRECTIONS. see 57D
NOTE
alternative flashing detail below will provide A FORM FOR EDGE OF CONCRETE.
EDGE FLASHING WITH DRip
extends 4 in. under waterproof membrane.
rim joist deeper than deck
JOISTS TO FORM DRip
stud wall, WOOD post, OR other vertical support

LIGHTWEIGHT-CONCRETE PORCH DECK
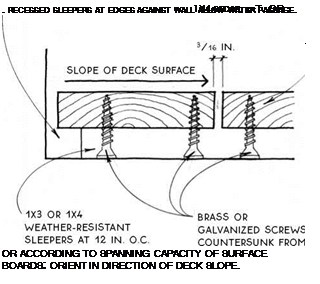 |
|
NOTE
DUCKBOARD DECKS ARE GENERALLY HELD iN PLACE ВУ GRAViTY. THEY SHOULD NOT BE USED iN AREAS OF EXTREMELY HiGH WiNDS.
|
|


DUCKBOARD DECK
Open Rail Shown
DUCKBOARD DECK
Detail
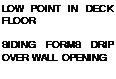
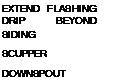
NOTE j
THIS DETAIL IS NOT SCUPPER THROUGH
RECOMMENDED IN SOLID RAIL SEE 57D У
AREAS OF SEVERE FREEZING WEATHER.


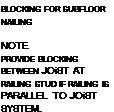
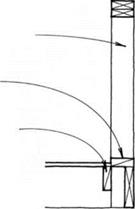


Because they make continuous contact with the porch or deck floor, solid railings are relatively simple to design and construct to resist overturning due to lateral force. For short railing spans (up to 8 ft. long) supported at both ends by a column, a wall, or a corner, the simplest framing (see the drawing below) will suffice because the top edge may be made stiff enough to span between the two rigid ends.
Longer railings or railings with one or both ends unsupported must be designed to resist lateral forces by means of a series of vertical supports firmly secured
to the porch or deck floor framing (see the drawing below). This means, of course, that the porch floor framing itself must be solidly constructed.
DOUBLE TOP PLATE, SUPPORTED AT BOTH ENDS, MAY BE STiFFENED FURTHER BY RAiL CAP. —-
SOLE PLATE NAiLED TO SiMPLE DECK CONSTRUCTiON
cONTiNuOuS RAiLiNG STuD notched over Rim JOiST & NAiLED TO JOiST System RESiSTS OvERTuRNING.
The same results may be achieved in a porch or deck built over a living space by using a balloon frame system with porch-rail studs continuous through to the wall below.
Waterproof deck with solid railing—Waterproof decks surrounded by a solid railing must be sloped to an opening in the railing. This opening can be a flashed hole in the wall, or scupper, as shown here, or it can be a gap in the wall that accommodates a stairway or walk. (Avoid directing water to walkways in climates with freezing temperatures.) The opening should be located away from the main structure of the building, and the floor should pitch toward the opening from all directions. In some cases, a second opening or overflow should be provided to guarantee that water won’t build up if the primary drain clogs.
wall/deck
connection
IS SAME AS
railing/deck connection see
DRAWINGS AT LEFT
Open deck with solid railing—Open decks surrounded by a solid railing are simple to drain since water will pass through the floor surface (see 55D). Care should be taken to provide adequate drainage from any surface below the deck.
