More efficient cooking saves energy and money directly, of course, but by keeping waste heat out of the kitchen, it also saves on air-conditioning. Although this impact might not be huge in a typical home, it can make a difference. As a rule, electric cooking appliances are more efficient than gas-fueled ones. But the relative price of natural gas versus electricity often makes natural-gas- fueled appliances a more economical choice. Gas cooktops also afford better heat control than their electric counterparts.
Because their functions are so different, it’s important to consider cooktops and ovens separately, even though they might be combined in a stand-alone kitchen range.
Gas Ovens Draw Electricity, Too
With ovens, rapid heat-up and cooldown aren’t as important as with cooktops, making electric ovens more competitive with gas, even for serious cooks. In fact, it is not uncommon for high-end ranges to have a gas cooktop and an electric oven. Again, electric models are more efficient: Electric ovens are 1.8 to 3.5 times as efficient as gas ovens, according to U. S. Department of Energy (DOE) data. Cost efficiency, however, largely depends on which type of fuel costs the least in your area.
Most gas ovens also use a lot of electricity while operating. In nearly all gas ovens today, when the gas burner is operating, an electric glow-bar igniter (sometimes called a "gas oven igniter") is on, drawing about 375w. (Interestingly, at a recent International Builders’ Show, not one kitchen-appliance salesperson who was asked seemed aware of this fact.) Found in all self-cleaning models, the glow bar ignites the gas when the oven is turned on and reignites it as it cycles off and on during the cooking or self-cleaning process. Those 375w (or even as much as 500w in some ovens) are a significant amount of electricity. If low electricity use is a priority in your home, consider a model without a glow bar, such as ranges made by the Peerless-Premier Appliance Co. (www. premierrange. com), which operate with a pilot or a spark ignition.
Cooktops & Ovens: Electric Wins over Gas
Cooktop efficiency is difficult to measure, and relatively little attention has been paid to it, primarily because stovetop cooking accounts for a small percentage of household energy use—about 5%, according to the American Council for an Energy Efficient Economy. My research shows that electric cooktops are the most efficient, and gas the worst. The section below ranks the most common cooktop technologies in order of efficiency based on the energy factor, which is the ratio of the amount of energy conveyed to an item being heated to the device’s overall energy consumption. Expressed as a decimal, it reflects the proportion of energy used that actually contributes to the cooking of food.
COOKTOP TYPES
Induction Although induction technology initially failed to take off when introduced a decade or so ago, it’s back, with more high – end induction cooktops entering the market. On an induction cooktop, electrical energy is transferred directly to ferrous-metal cookware through magnetic induction. Efficiency is the highest of any cooktop (about 84%) because the cookware is heated directly. It’s also a safer way to cook: The cooking surface does not heat up, enabling photos like the one at top left on facing page, where water boils in a cutaway pan while ice cubes rest intact on the "burner’s" surface. Induction
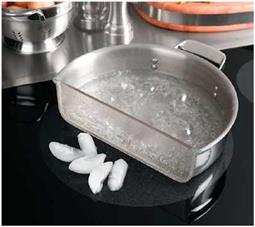
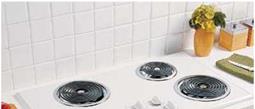
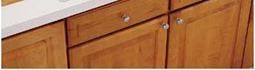
ELECTRiC COiL
Energy Factor: 0.737
RADiANT
Energy Factor: 0.742
cooktops also heat up and cool down quickly, providing precise controllability. Downsides include high cost and the fact that only certain cookware can be used. Cast-iron, enameled cast iron, and some stainless-steel cookware work. Test yours to make sure a magnet sticks to it, or look for a label.
Radiant ceramic The most common mid – to high-end electric cooktop today, it has relatively fast-heating radiant elements under ceramic glass, providing a sleek, easy-to-clean stovetop surface. Flat-bottom cookware is needed for good surface contact; older – style cast-iron pans are not recommended because burrs on the metal can scratch the glass surface. Radiant-ceramic cooktops heat faster than electric coils and are nearly equal in energy efficiency.
GAS, NO PiLOT
Energy Factor: 0.399
GAs, piLOT
Energy Factor: 0.156
Electric coil Available on low-cost ranges and cooktops, these old-fashioned open-coil elements are slow to heat up and difficult to clean, but fairly efficient at transferring electric energy to the pot.
Gas (natural or propane) Cooks prefer gas burners for speed and controllability, but indoor-air-quality experts often recommend against gas for health reasons. Although gas cooktops rate worst in terms of energy efficiency, they are usually more cost-efficient because the price of natural gas is typically a lot lower than electricity. Gas cooktops use only about 40% of the energy produced, and if there’s a continuously burning pilot light, the overall efficiency is far lower (about 16%). In some areas, propane is nearly as expensive as electricity per unit of delivered
energy, making electric cooktops a more ecoOvens and Oven Fans nomical option. The efficiency of natural gas
and propane is essentially the same.
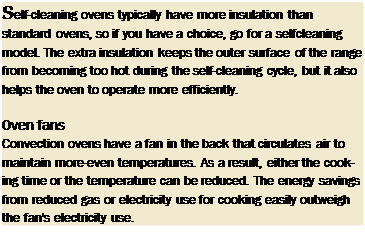
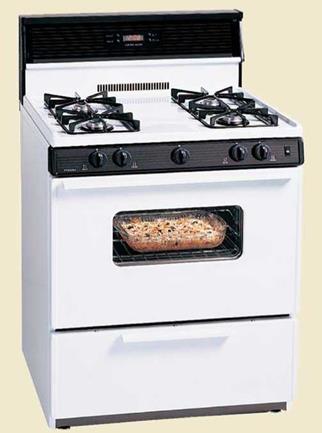
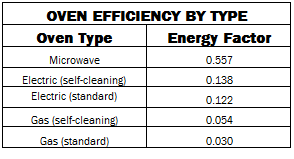