Wood insulated concrete forms (WICFs) were invented of necessity in Europe following World War II. Massive rebuilding was required and there was a shortage of conventional building materials. Waste wood was plentiful, and insulating forms made by mixing mineralized (clay impregnated) wood chips with cement proved to be a good way to conserve both precious fuel and scarce concrete. These wood and cement masonry units had many excellent building properties. They were lightweight and noncombustible, had a high strength-to-weight ratio, and were dimensionally stable, insulative, and resistant to freeze-thaw, rot, insects, and fungus growth. The resulting structures were more durable, energy efficient, and economical than structures built by prewar methods. In continuous use since the 1940s under various brand names, WICFs are still a preferred method of construction throughout Europe.
In North America, WICFs are available through Durisol, Faswall, and Healthy Buildings Made Easy. They come as interlocking hollow blocks similar to cinder or masonry unit blocks. They are dry-stacked (without mortar) and filled with concrete and reinforcing steel. Durisol produces special thermal units that can incorporate mineral fiber insulation inserts to reach an R-value of 28. Faswall is a shorter, heavier block with thicker walls that can incorporate different in sulation inserts to produce an R-value of 26.
Although all the cores are usually filled with concrete, a more ecological application is to use concrete only in the cores where steel rebar is required and to fill the other cores with natural insulation or earth. WICFs are considered to be a form of vapor diffusible or breathing wall construction.
Aerated Autoclaved Concrete
Aerated autoclaved concrete (AAC) was first developed by a Swedish engineer between 1920 and 1932. It has since been refined into a concrete-based block material with high insulation used for both load – and non-loadbearing walls. AAC is manufactured from quartz sand, lime and/or cement as the binding agent, aluminum powder, and water. The aluminum powder reacts with calcium hydroxide and water to form tiny hydrogen gas bubbles. At the end of the foaming process the hydrogen escapes into the atmosphere and reacts with air to form water, and air replaces the hydrogen in the formed bubbles. The finished block does not contain aluminum. The final block form is autoclaved under heat and pressure to reach full strength.
AAC block construction uses standard masonry skills and is installed in a manner similar to regular cinder block, using a thinset instead of a cement mortar. Where reinforcing is required by code, special units with bored cylindrical holes can be vertically stacked and filled with rebar and cement grout, thus
£ОДМ& Ft И [ЭН
£*ТРГ fATF
AAc/ctHcpFTC fcO/SP №/SW
l©" hJWCH№> Л&ЕЛТЄ О CCNC – fHocf= whlL
P£i/4TOf^e№f,4r
<peu.
VEfTVAL c^fSEL №HN R^EWENT
OAX F^££P PlASTpC
|
LIN^- FL(4ST^P’ SfcA^P
PrtNfe^^P Gc**r. pooT! N6>
|
minimizing the use of cement. No blocking is required, and shelving and other attachments can be screwed directly into the walls. The blocks can be sawn, cut and shaped with woodworking tools. The solid, lightweight walls combine thermal mass and high insulation values. They have outstanding seismic, acoustic, and fire performance. The walls can be plastered inside and out and are inert and stable, with no toxic outgassing. This system has worked well for people with chemical sen
sitivities, but sensitive individuals should pretest the thinset mortars for acceptability. In North America, aerated autoclaved concrete is manufactured by Aercon, Contec, Huma – built HumaBlock, and TruStone.
Conclusion
A variety of natural materials can be used to create heirloom quality buildings that are ecologically sound, promote health, and have
outstanding energy efficiency. In short, natural building materials may be superior in all these respects to the standard building systems prevalent in industrial countries. An owner choosing to use a natural alternative building system is a pioneer who may be well rewarded for an adventuresome spirit. Regional factors such as drainage, rainfall, temperature, humidity, freeze and thaw cycles, and the availability of natural materials will make some natural building systems more suitable for certain locations than others.
When planning to build with alternative materials, make careful inquiry to determine the status of these materials with local building authorities to ensure that the alternative you choose will be permitted in your jurisdiction. Each of the model building codes used in the United States has a provision for alternative methods and materials. Building officials of the jurisdiction in which a project is located have the authority to approve any building they deem adequately meets the intentions
and provisions of the code. It may be necessary to educate a building official about the materials you intend to use, and it is worthwhile to gather information about code approvals that have been granted elsewhere for the same materials. If a building official is unable to make a determination about the alternative material you are presenting, it may be possible to move forward with approvals by creating a legal document holding the building department harmless. DCAT is a nonprofit organization dedicated to addressing the challenge of institutional barriers to sustainable building and development found in building codes.
Earlier in the 20th century it was incumbent upon industrial manufacturers to prove to code officials that their products performed as well as their preindustrial counterparts. The powerful forces of industry, with their financial capability to test manufactured products, have now completely reversed the situation to the point where nonproprietary materials and methods of construction are viewed as inferior.
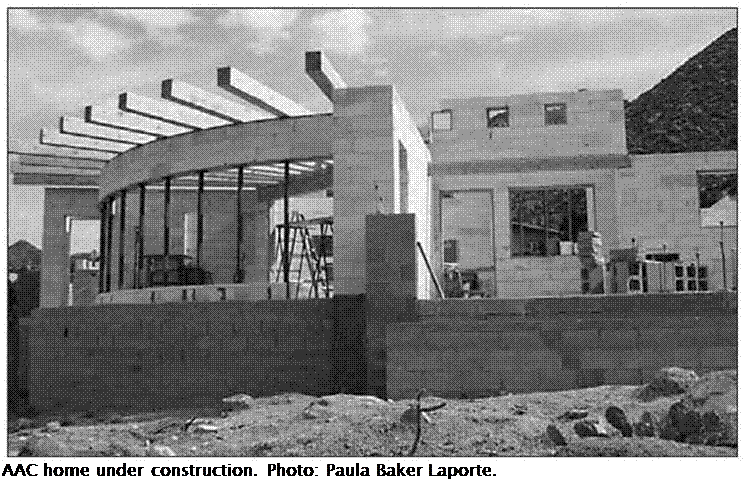 |
Ironically, this is so in spite of the thousands of years of research and development that have gone into the refinement of natural building techniques. In order to gain more widespread acceptance into mainstream building venues in this country, each example of natural building mustbe well-conceived, well-documented, and based on a sound knowledge of the laws of nature. In fact, a thorough understanding of building science is even more important for designers and builders using these alternative systems because of the high degree of experimentation involved in adapting ancient techniques to modern comfort and performance demands.
We would like to emphasize that the use of natural construction materials does not automatically create a healthy home. The material used in the buildings walls is only one of many components that go into creating a home environment. However, when the alternative systems described in this chapter are
used in conjunction with the other principles of healthy building outlined in this book, it is possible to produce buildings of exceptional vitality.
Further Reading
Baker-Laporte, Paula and Robert Laporte. EcoNest: Creating Sustainable Sanctuaries of Clay, Straw and Timber. Gibbs Smith, Publisher, 2005. Chiras, Daniel D. The Natural House. Chelsea Green Publishing Company, 2000.
Cob Cottage Company Earth Building and Cob Revival: A Reader. 3rd ed., Cob Cottage Company, 1996.
Easton, David. The Rammed Earth House. Chelsea Green Publishing Company, 1996.
Elizabeth, Lynne and Cassandra Adams, eds. Alternative Construction: Contemporary Natural Building Methods. John Wiley and Sons, 2000. Evans, Ianto et al. The Hand Sculpted House. Chelsea Green Publshing Company, 2002.
Kennedy, Joseph et al., eds. The Art of Natural Building. New Society Publishers, 2002.
King, Bruce. Buildings of Earth and Straw. Solar Living Center, 1996.
The Last Straw: Vie International Quarterly Journal of Straw Bale and Natural Building. See thelast straw. org.
MacDonald, S. O, and Matts Myhrman. Build It With Bales: A Step-by-Step Guide to Straw-Bale Construction. Treasure Chest Books, 1997.
McHenry, Paul G. Adobe: Build It Yourself University of Arizona Press, 1985.
Minke, Gernot. Earth Construction Handbook: The Building Ma terial Earth in Modern Architecture. WIT Press, 2000.
Roodman, David Malin and Nicholas K. Lenssen.
A Building Revolution: How Ecology and Health Concerns Are Transforming Construction. Worldwatch Paper 124,1995.
Steen, Athena Swentzell et al. The Straw Bale House.
Chelsea Green Publishing Company, 1994.
Steen, Bill et al. Built by Hand. Gibbs Smith, Publisher, 2003.
Wanek, Catherine. Vie New Straw Bale Home. Gibbs Smith, Publisher, 2003.
Weismann, Adam and Katy Bryce. Building with Cob: A Step-by-Step Guide. Green Books, 2006.