Because HVAC system design is complex, judgement on system type, size, and location of ducts is often left to the expert – the HVAC subcontractor. But the builder should understand some basic facts to insure that the most efficient, cost-effective system available is being installed.
Select the most appropriate economical system according to home design, local climate, fuel availability, and market ^reference. If a ducted system is to be used, a concise guide is available тот the National Association of Home : Builders, 15th & M Streets, NW, Washington, DC 20005. Titled Residential Duct Systems, this guide describes the most efficient duct methods according to fuel, type of equipment, operating efficiencies, and relative cost.
Design starts with accurate heat loss calculations (and heat gain for cooling). This is the only real basis for selecting equipment and designing the system. Too often equipment is selected based on past experience and judgement.
But, since each home design is unique, the HVAC system should be tailor made for that home. Guidelines on how calculations are made are presented in the Residential Duct Systems manual mentioned above as well as in the Insulation Manual for Homes and Apartments, also available from NAHB.
The standard calculation procedure used in the HVAC trade is in Manual J. Load Calculation for Residential Winter and Summer Air Conditioning available from Air Conditioning Contractors of America, 1228 – 17th Street, NW, Washington, DC 20036.
Avoid the tendency to oversize HVAC equipment. Some believe that if a certain size equipment is adequate based on proper calculations, a size larger will be even more desirable. Since the incremental cost of upsizing appears not too excessive, it is tempting to oversize. However, equipment based on sound heat loss-gain calculations is almost always more efficient and uniform in heating and cooling than oversized units. Also, be aware of unit efficiency.
For each 1 /2-ton heatpump or air conditioning reduction, equipment and duct costs can be reduced by about $275. Wiring costs may also be reduced since a lighter circuit may be possible.
Downsized or redesigned duct systems will be possible in energy-efficient homes where HVAC equipment is smaller. In addition, the system will perform better since proper velocity and air flow will be maintained. Another standard guide for residential duct design is Manual D – Duct Design for Residential Winter and Summer Air Conditioning, from the Air Conditioning Contractors of America, 1228 17th Street, NW, Washington, DC 20036.
In small, single-story homes with a central hall that abuts all living areas, consider using a dropped-hall ceiling plenum system. In this system, the hall ceiling and walls are drywalled as usual. Then another ceiling, dropped 6 inches to 8 inches below the conventional ceiling, is framed and drywalled, thus providing a plenum for air distribution.
High inside wall registers to each adjoining room are connected to the plenum by a short sheet metal boot through the wall. Although the system described has worked well in many installations, some local inspectors insist on sheet metal ducts within the ceiling cavity. If so, the system is still more cost effective than most.
The CABO One and Two Family Dwelling Code permits such "gypsum ducts" up to 125 degrees F., which would accommodate low output temperature equipment such as most heat pumps or electric furnaces. Fossil fueled equipment generally exceed this temperature limit.
Radial duct systems are often the simplest duct systems to install.
Branch ducts connect directly to the equipment plenum without trunks. Radial systems are typically installed where it is not necessary to conceal the duct work and where the equipment is centrally located. The basic simplicity of the system provides cost savings through reduced materials and less labor.
In smaller, well-insulated homes where central air conditioning is not required, electric baseboard heat with individual room thermostats offers significant construction cost savings, and depending on comparative fuel costs and availability, may offer operating cost savings because of the ability to "zone" heat the house.
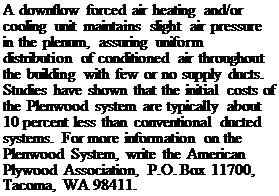
One very innovative heating/cooling system that has enjoyed some regional success is the underfloor heating/cooling plenum, being marketed by the wood industry under the name "Plenwood." Instead of using heating and cooling ducts, the entire underfloor space is used as a sealed – plenum chamber to distribute warm or cool air to floor registers in the rooms above.
Several of the JVAH builders used innovative HVAC systems to reduce costs. In Santa Fe and Phoenix, bathroom ventilation fans were eliminated, saving about $150 per unit in ventilation ana electrical wiring.
In Crittenden County, Arkansas, the builder used the ductless dropped ceiling approach to air distribution in homes with central air conditioning.
In Christian County, Kentucky, a radial duct system was used instead of one large trunk line throughout the center of the crawl space with lateral ducts. This system saved an average of $125 per house.
The most innovative HVAC system built in the JVAH program was in Tulsa, Oklahoma, where the Plenwood system described earlier was installed. Wayne Hood used the underfloor area as a ductless return air plenum (See Footings and Foundation Section) with a pressure treated wood foundation. Hood estimated that foundation, floor and heating/cooling costs were reduced by a total of $1,470 per unit.
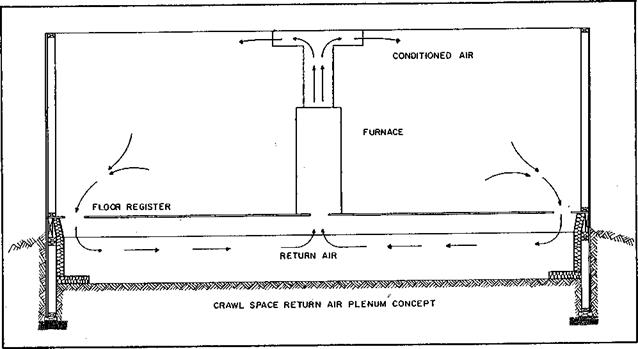