The setting process anchors the windows and doors in their final positions. Complete installation happens later, when we move inside the house and work on the interior trim. The windows and doors used in affordable housing are mainly vinyl and vinyl clad, though aluminum-clad frames are still installed in some areas. Some codes require that window frames be clad with white vinyl; check with your local building department. Dark-colored vinyl absorbs more solar heat and, as a result, tends to deteriorate faster. On the other hand, dark-colored aluminum cladding holds up well in sunny areas.
Both vinyl and aluminum-clad windows come with a nailing flange on the outside of the window frame; the flange greatly simplifies the installation process. The most popular styles are single hung (the bottom sash moves up and down), double hung (both sashes move up and down), and sliding (one sash slides to the side). Windows with a built-in 1-channel, or channel surround, make it easy to hide the ends of vinyl and other siding without the use of extra trim.
Windows in affordable houses should definitely be double-glazed. The heat loss and gain through single-glazed windows is considerable. In very cold or very hot climates, windows with low-E coatings offer even more energy savings. For more information on energy-efficient glazing, see Resources on p. 278.
Setting a window
Flanged windows are the easiest windows to install, but windows that come with exterior trim instead of flanges are fairly easy as well. The main difference is that you nail through the exterior trim instead of through the flanges. No matter which type of window you use, its good to have two people for this job—one inside the house and one outside. There are three basic steps involved in setting a window:

1. Caulk the flange. Squeeze a generous bead of exterior caulk or sealant on the back of each window flange (see the left photo on p. 156).
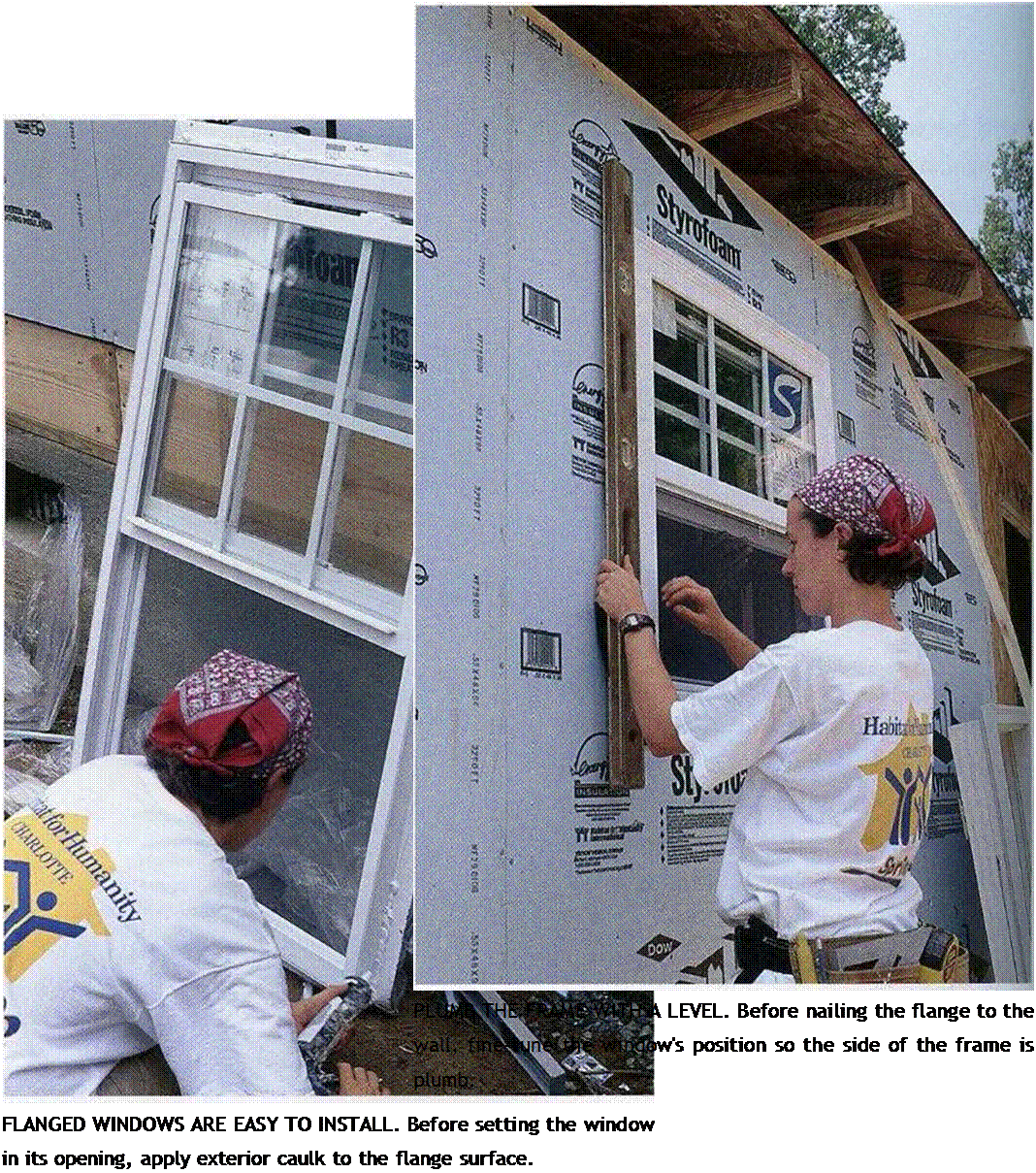
3 • Nail the flange to the wall. Secure the window by driving іИ-in.-long galvanized roofing nails at each corner of the window flange and every 8 in. elsewhere. Be careful not to damage the vinyl frame by hitting it with your hammer. When I’m building in rainy climates, I make one more seal all around the windows by running a strip of waterproof tape over the flange and onto the housewrap. It may be overkill, but who wants to tear off siding to repair a leaky window in the middle of a rainstorm?
Setting a prehung exterior door
Exterior doors are often prehung units that include jambs, a threshold, and wood exterior trim. I buy doors predrilled for both the house lockset and the deadbolt. Given the option, I also choose a door with a double-glazed glass window to bring more light into the house.
Take note of which way the plans say the door should open, and make sure the door you ordered swings the right way (see the illustration at bottom right). Most exterior doors open inward. Also, make sure the door jamb is the proper width for the wall. A 2×6 wall takes a wider jamb than a 2×4 wall does. There are four basic steps involved in setting a prehung door:
1. Flash the doorsill. The sides and top of the rough opening can be flashed in the same way as a window. With an exterior door, sill flashing is essential if you want to prevent rot beneath the threshold. I prefer to use 12-in.- wide aluminum flashing for this application.
Cut the flashing about 6 in. longer than the width of the rough opening so it can cover the threshold area completely and extend several inches up each trimmer stud. Cut the flashing as necessary to create ears that fold onto the subfloor and over the exterior wall sheathing. You can keep the flashing in place with a few galvanized roofing nails.
2. Test-fit the door. When working with a prehung door, your primary concern is to set itsothat it opens and closes with ease. Fortunately, this is pretty easy to do. Once you’ve removed any materials used to protect the door during shipping and any device used to hold the door secure in its jamb, check the fit of the door in its opening. It should fit easily see the photo on p. 158).
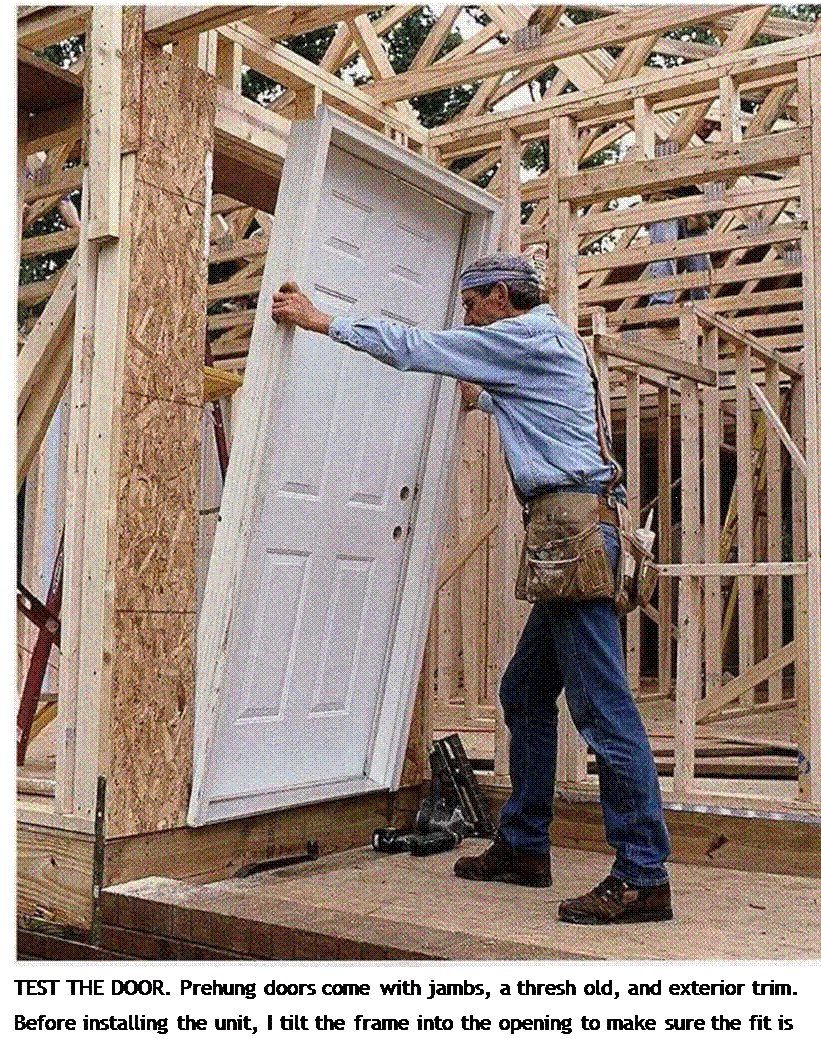
3. Set the door in place. Run a bead of sealant on the back of the door trim and a couple of heavy beads across the bottom of the rough opening on the flashing where the threshold will sit. Then set the frame in its opening. From the inside, adjust the frame so that there’s a gap of about A in. all the way around the door. This will allow the weatherstripping on the door frame to seal properly. Secure the door in the opening by driving a 16d finish nail through each corner of the exterior trim and into the sheathing and studs. (Alternatively, you can drive З-in.-long trim-head screws.)
4# Finish fastening the door. Check the door again to see that it opens and closes with ease. If it does, then drive more 16d finish nails (or screws) 2 ft. o. c. all the way around the trim. Set all nails or screws about A in. below the
surface of the wood so they can be hidden by putty and covered with paint. Drive 8d finish nails or 2-in.-long screws through the hinge side of the jamb and into the trimmer near each hinge. If the jamb is not tight against the trimmer, slip in a shim to prevent the jamb from bowing. Shim and nail through the jamb on the lock side next, but be sure to keep nails away from the lock and deadbolt area. Finally, drive the long screws that are included with the door frame through the hinges and the jamb and into the trimmer. These help hold the entire assembly in place.