Binder-absorbing additives are the most popular SMA stabilizing agents. The following properties are required of a stabilizing material:
• Adequate binder absorbing power—this is the most significant property
• Ability to act without weakening the mixture—the stabilizer must not create glide planes and lessen the grain-interlocking strength.
Stabilizers of this type occur in various forms related to the following kinds of raw materials: [18]
• Glass—in the form of threads (like fiberglass wool)
• Others—for example, leather waste products (leather dusts)
The crucial difference among stabilizers is their absorbing power. To date, the most effective of the binder-absorbing stabilizers are cellulose fibers. They have a very high-binder absorption, which results in holding the binder firmly in position.
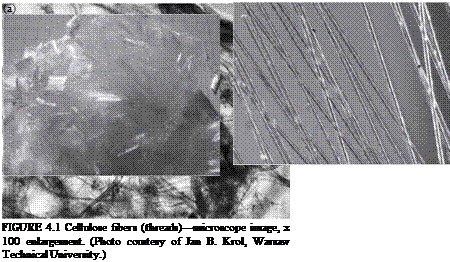
Fiber-free stabilizers have a wide range of binder absorption powers, so any new product should be tested in the laboratory every time (see Chapter 8). One should also remember that stabilizers may have substantially different densities, which are directly translated into their volumes in a mixture. High-density mineral fibers need a higher addition rate at batching, usually on the order of 0.4-0.6% (m/m). The same is true of polypropylene and glass fibers.
FIGURE 4.2 An example of 6-mm long polypropylene fibers: (a) macroscopic view, (b) the same fibers in microscope image, x 100 magnification. (Photo [a] courtesy of Krzysztof BlaZejowski and photo [b] courtesy of Jan B. Krol, Warsaw University of Technology.)
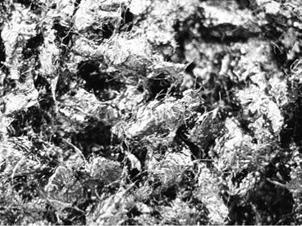
FIGURE 4.3 Plastic fibers can be an SMA stabilizer but must be used at a high-addition rate. The photo shows an SMA mix with 0.6 % (m/m) of polypropylene fibers. (Photo courtesy of Halina Sarlihska.)
|
Furthermore, if a stabilizer does not work efficiently enough, increasing its quantity may improve the draindown performance. However, larger amounts of stabilizers may cause unexpected troubles, such as decreasing mixture workability. For example, plastic fibers (Figure 4.3) are marked by a lower absorption power. Using a high quantity of them (say, about two times more than cellulose fibers) will produce a substantial growth of stiffness and low workability. Small wonder—6 kg of such fibers per 1 metric ton of an SMA translates into a substantial volume; fibers are clearly visible in the mix as shown in Figure 4.3.
The most popular stabilizers—namely, products of cellulose—occur in the following forms:
• Loose fibers—in the form of irregularly shaped cellulose threads
• Pellets—granulated products without a binding agent
• Granulated products—cylinder-shaped granules that consist of threads coated with bituminous binder or another agent (e. g., wax or plastic)