In the Comite Europeen de Normalisation, or European Committee for Standardization (CEN), the member states’ requirements for aggregates designed for asphalt mixtures have been unified in the EN 13043 standard entitled Aggregates for Bituminous Mixtures and Surface Treatments for Roads, Airfields, and Other Trafficked Areas. It provides a set of aggregate properties and a series of requirement levels (categories) for each property.
Each CEN member state adopting this standard has defined its own national requirements, considering such issues as local climatic conditions and experience of engineering, from among the alternative properties and categories provided in the standard.
The requirements for SMA aggregates according to the EN 13043 standard are displayed in Tables 5.1 and 5.2. The following is an explanation of records in the Tables 5.2 through 5.4: [20]
• No requirement category (NR), which means that in a given country’s national specification, the requirement for this property is not used, e. g., MBFNR
• Fractions of aggregates are described as d/D (e. g., 2/5 mm) where:
• D means nominal upper limit of gradation (oversized grains are allowed)
• d means nominal lower limit of gradation (undersized grains are allowed)
Some additional explanations are provided in Table 5.1, but details can be found in EN 13043. An example of a similar type of EN standard is described in Chapter 14.
Tables 5.2 through 5.4 present the requirements from selected European countries. The substantial differences among these countries may be confusing. In the most important properties, the demanded level is more or less similar, e. g., LA index is from 20 to 25% or flat and elongated content is usually as high as 20-25%.
Although it is the same SMA mixture, the requirements for components or aggregates, depend on the following factors:
• Materials available in a specified place—countries specify their requirements based on long-term experience with aggregates, test results, and research. Requirements also depend on accessible sources of aggregate— countries in which sufficient amounts of very good quality materials exist are able to limit the number of required properties. One example of such a situation are the Nordic (Scandinavian) countries. However, several countries have quite a wide range of aggregates with very different qualities. There is a need to balance the technical requirements with a view toward economics.
• Technology and previous experiences with materials also have an impact on the set of requirements. For example, using hydrated lime (in mixed filler) is not very popular in Europe, therefore only a few countries put them into their specifications (filler category Ka).
• Test methods in EN 13043 come from different national practices, as described in Chapter 14, hence many countries do not use some of them in practice. For example, the LA method has not been commonly used in Germany, and the same can be said for Rigden’s method in Poland, Aggregate Abrasion Value (AAV) outside the United Kingdom, and the Nordic abrasion value outside Scandinavian countries. Many countries use declared categories because without past experiences it was hard to establish any reasonable requirement.
• In specified number of countries, production of aggregates for asphalt layers is regulated with precisely prescribed fractions and their individual gradation limits. Such a situation, in which all producers of aggregates make the same fractions and with very similar gradation, is very comfortable for asphalt mix producers. At the same time any additional
TABLE 5.1
Comments on System of Requirements Based on EN 13043

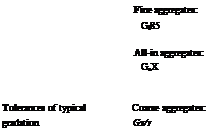
comments
Gradation of aggregate fractions after EN 13043 are labeled as GXY category; the numbers describe allowable amounts of oversized (X) and undersized (Y) material, e. g. Gc90/15 means that only 10% of oversized and 15% of undersized material is allowed, similarly GC85/15 means that only 15% of oversized and 15% of undersized material is allowed; category Gc90/10 is the highest possible choice and GC85/35 is the lowest.
There is only one category for fine aggregate,
GF85, which means the limit for oversized grains (>2 mm) is 15% by mass.
When all-in aggregates are used one of two GaX categories, can be used Ga90 and Ga85, where maximum limits for oversized material are 10% and 15% (by mass), respectively.
The idea of this type control is based on a requirement that the producer will document and declare the typical gradation of any produced aggregate fraction; tolerances of typical gradation, labeled as GX/Y, are used for gradation control within the fraction; depending on the D/d coefficient, the control sieve is chosen as D/2 or D/1.4; the number x means x—overall limits of amount of material passing by control sieve (20 means 20-70% by mass; 25 means 25-80% by mass), and the number y means y – tolerances for typical gradation on control sieve declared by aggregate’s producer (15 means ±15%; 17.5 means ±17.5%); example category G25/15 means that on sieve D/2 or D/1.4 overall limits are 25-80% and the tolerance from the declared value is ±15%
This requirement applies to tolerance of percentage of grains passing by sieves D, D/2, and d compared with the gradation declared by producer;
category Gtc10 mean tolerances on sieves: D ±5%, D/2 ±10%, d ±3%,
category Gtc20 mean tolerances on sieves: D ±5%, D/2 ±20%, d ±3%,
Comments on System of Requirements Based on EN 13043
TABLE 5.1 (CONTINUED)
properties
|
Label of category
|
comments
|
Fines content, according to EN 933-1
|
fx
|
Amount of grains passing by 0.063-mm sieve, where x in fx category means maximum allowable content of fines
|
Fines quality, according to EN 933-9 (methylene blue test); in fine and all-in aggregates
|
MBFX
|
Control of harmful fines (e. g., swelling clay); category MBFX means that maximum X methylene blue value (g/kg) is allowed in fines; used only if fines content is between 3% and 10% by mass of material; if fines content >10%, requirement for filler applies
|
Angularity of fine aggregates according to
EN 933-6, p.8
|
EcsX
|
Flow coefficient of fine aggegates, labeled with EcsX category, where X means minimum time of flow in seconds
|
Shape of coarse aggregate (Flakiness Index EN 933-3, Shape Index EN 933-4)
|
SIX or FIX
|
FI or SI could be used for determination of grains’ shape; labeled as SIX and FIX, where maximum allowable amount of flat and elongated particles is marked as X (% by mass)
|
Percentage of crushed and broken surfaces in coarse aggregates, according to EN 933-5
|
CXY
|
Percentage of crushed and broken surfaces labeled as Cxy, where X means percentage of completely broken particles (by mass) and Y means percentage of completely rounded particles (by mass); so a requirement to use only crushed coarse aggregates is described in category СЮ0/0. Category C95/1 allows up to 1% of noncrushed particles in aggregates.
|
Resistance to fragmentation (crushing), according to EN 1097-2 clause 5
|
LAX
|
Resistance to crushing (fragmentation) with LA method; labeled as LAX, where maximum allowable LA coefficient is marked as X (%)
|
Resistance to fragmentation (crushing), according to EN 1097-2 clause 6
|
SZx
|
Resistance to crushing (fragmentation) with German Schlagzertrummerungswert method (impact test); labeled as SZX where maximum allowable SZ coefficient is marked as X (%)
|
Resistance to polishing according to EN 1097-8
|
PSVx
|
PSV; labeled as PSVx, where X means required minimum PSV value
|
Resistance to surface abrasion, according to EN 1097-8 Annex A
|
AAVx
|
AAV; labeled as AAV# where X means maximum allowable AAV value
|
Resistance to wear, according to EN 1097-1
|
MDEX
|
Micro-Deval coefficient; labeled Mdex, where X means maximum allowable Micro- Deval value
|
Resistance to abrasion from studded tires, according to EN 1097-9
|
ANX
|
Nordic abrasion value; labeled as ANx, where X means maximum allowable value
|
|
TABLE 5.1 (CONTINUED)
Comments on System of Requirements
Properties Label of category
Water absorption, Wcm0.5
according to EN 1097-6 WA24X
Resistance to freezing and Fx
thawing, according to EN 1367-1
Resistance to freezing and MSx
thawing, according to EN 1367-2
Resistance to thermal —
shock, according to EN 1367-5:
Affinity of coarse —
aggregates to bituminous binders, according to EN 12697-11
“Sonnenbrand” of basalt, SBSz or SBla
according to EN 1367-3 and EN 1097-2
Coarse lightweight ^lpcX
contaminators, according to EN 1744-1, p.14.2
based on EN 13043
comments
The method of testing is chosen depending upon the size of the aggregate:
• Using EN 1097-6 clause 7 refers to category WA24X, where X means maximum allowable percentage absorption by mass.
• Using EN 1097-6 Annex B refers to category Wcm^-5, where 0.5 means maximum allowable percentage absorption by mass (there is only one category <0.5%).
Additionally EN 13043 connects water absorption and resistance to freeze-thaw of aggregates; aggregates with small absorption are assumed to be freeze-thaw resistant.
Category Fx is used, where X means maximum allowable percentage loss of mass; test can be conducted in water, salt solution, or urea.
Category MSx is used, where X means maximum allowable percentage loss of mass; test is conducted with magnesium sulfate.
Test of aggregate resistance for high temperature; results are declared
Test of binder adhesion to aggregate; results are declared
This is to check for basalt rock decay, which results in lowering aggregate strength and in most cases in very low freeze-thaw resistance of basalt aggregate; categories SBsz and SBla mean that after test (boiling for 36 hrs) and crushing (in SZ or LA, respectively), the aggregate must meet required values:
• Loss of mass after boiling: max 1.0% (and)
• Increase of impact value: max 5.0% (SBsZ) (or)
• Increase of LA coefficient: max 8.0% (SBla) The content of coarse lightweight organic
contaminants larger than 2 mm should be maximum X% by mass.
Comments on System of Requirements Based on EN 13043
TABLE 5.1 (CONTINUED)
properties
|
Label of category
|
comments
|
Dicalcium silicate
|
Resistance
|
Slag aggregate will be free from dicalcium silicate
|
disintegration of air-cooled blastfurnace slag, according to EN 1744-1, p. 19.1
|
required
|
disintegration, the results are declared.
|
Iron disintegration of
|
Resistance
|
Slag aggregate will be free from iron
|
air-cooled blast furnace slag, according to EN 1744-1, p. 19.2
|
required
|
disintegration; the results are declared.
|
Volume stability of steel slag aggregate, according to EN 1744-1, p. 19.3
|
Vx
|
Test applied to basic oxygen furnace slag and electric arc furnace slag; category Vx, where X mean maximum allowed expansion by volume percentage
|
Water content (added filler), according to EN
1097-5, %
|
|
Mass content of water in added filler (commercially produced) is fixed and will be maximum 1%.
|
Stiffening properties: Voids of dry compacted filler (Rigden), according to EN 1097-4
|
Vx/Y
|
The range of Rigden voids in dry compacted filler; categories are labeled as VX/y, where X is a lower limit and Y is an upper limit of voids; note that these are voids according to Rigden’s method not Rigden’s method modified by Anderson
|
Stiffening properties: Delta ring and ball, according to EN 13179-1:
|
Ar&bX/Y
|
The range of increase of softening point (SP) with ring-and-ball method; categories are labeled as Ar&bX/Y, where X is a lower limit and Y is an upper limit of SP increase
|
Water solubility, according to EN 1744-1
|
WSx
|
The water solubility is labeled as WSx, where X is a maximum allowed percentage (by mass).
|
Water susceptibility, according to EN 1744-4
|
—
|
No specified limits; the results are declared
|
Calcium carbonate content of limestone filler aggregate, according to EN 196-21
|
CCX
|
Calcium carbonate content is labeled as CCx, where X is a minimum required percentage (by mass) of CaCO3.
|
Calcium hydroxide content of mixed filler according to EN 459-2
|
KaX
|
Calcium hydroxide (hydrated lime) content is labeled as KaX, where X is a minimum required percentage (by mass) of Ca(OH)2.
|
Bitumen number of added filler, according to EN 13179-2
|
BNx/y
|
The range of bitumen number; categories are labeled as BNx/y where X is a lower limit and Y is an upper limit
|
|
Note: AAV = Aggregate abrasion value; FI = flakiness index; LA = Los Angeles; PSV = polished stone value; SZ = Schlagzertrummerungswert; SI = shape index.
TABLE 5.2
Requirements for SMA Coarse Aggregate according to EN 13043 in Selected CEN-Member Countries, Aggregates for SMA at the Highest Traffic Level (Reference Mixture SMA 0/11)
List of Categories by Country
Austria
Germany ONORM В
|
TL Gestein StB 04 Anhang F
and TL Asphalt StB 07
|
Slovakia KLK 1/2009
|
3584:2006 RVS 08.97.05:2007 (Class G1)
|
Switzerland SN 670130a: 2005
|
Poland
WT-1 Kruszywa 2008
|
Properties3
|
1
|
2
|
3
|
4
|
5
|
Grading, according to EN 933-1
|
Gc90/10 for (2/5 mm) Gc90/15 for (2/5, 5/8, 8/11 mm)
|
Gc90/10
|
Gc90/15
|
Gc85/15
|
Gc90/15
|
Tolerances of typical
|
—
|
Declared
|
—
|
f-^20/15
|
f-^25/15
|
gradation
|
Fines content, according to
|
Fractions 2/5 to 8/11
|
/1
|
/1
|
/1
|
/2
|
EN 933-1
|
mm:/2 (max 2%)
|
(max 1%)
|
(max 1%)
|
(max 1%)
|
(max 2%)
|
Fines quality, according to EN 933-9—methylene blue
|
Declared
(value to be reported)
|
—
|
—
|
—
|
—
|
test
|
Shape of coarse aggregate
|
SI’20 ОГ ^20
|
SI’20 ОГ ^20
|
SI15
|
FI25
|
SI2o or FI20
|
(Flakiness Index EN 933-3,
|
(max 20%)
|
(max 20%)
|
(max 15%)
|
(max 25%)
|
(max 20%)
|
(Continued)
List of Categories by Country
TABLE 5.2 (CONTINUED)
Requirements for SMA Coarse Aggregate according to EN 13043 in Selected CEN-Member Countries, Aggregates for SMA at the Highest Traffic Level (Reference Mixture SMA 0/11)
|
|
|
Austria
|
|
|
|
Germany
|
|
ONORM В
|
|
|
|
TL Gestein StB 04
|
|
3584:2006
|
Switzerland
|
Poland
|
|
Anhang F
|
Slovakia
|
RVS 08.97.05:2007
|
SN 670130a:
|
WT-1 Kruszywa
|
|
and TL Asphalt StB 07
|
KLK 1/2009
|
(Class C1)
|
2005
|
2008
|
Properties3
|
1
|
2
|
3
|
4
|
5
|
Percentage of crushed and
|
Qoo/o,
|
C100/0
|
Qoo/o
|
C95/1
|
Qoo/o
|
broken surfaces in coarse
|
C95/1,
|
|
|
|
|
aggregates, according to EN 933-5
|
Q0/1
|
|
|
|
|
Resistance to fragmentation
|
LA20
|
LA 25
|
LA 20
|
4/8 mm—LA 2 .
|
LA2o or LA 25
|
(crushing), according to EN
|
(max 20%)
|
(max 25%)
|
(max 20%)
|
8/11 mm— LA20
|
depending on
|
1097-2 clause 5 (LA
|
|
|
|
11/16 mm— LA25
|
petrographic type
|
method)
|
|
|
|
|
of aggregate
|
Resistance to fragmentation
|
SZI8
|
—
|
—
|
—
|
—
|
(crushing), according to EN 1097-2 clause 6 (German SchlagzertrUmmemngswert)
|
(max 18%)
|
|
|
|
|
Resistance to polishing,
|
PSV51
|
psvx
|
PSV50
|
PSV50
|
PSV50
|
according to EN 1097-8
|
(min 51)
|
(min 56)
|
(min 50)
|
(min 50)
|
(min 50)
|
Resistance to surface
|
—
|
—
|
—
|
—
|
—
|
abrasion, according to EN 1097-8 Annex A
|
|
|
|
|
|
|
|
 |
Resistance to wear (Micro – Deval), according to EN 1097-1
|
|
Mde20 (max 20%)
|
Resistance to abrasion from studded tires, according to
EN 1097-9
|
|
|
Water absorption according
|
Wcm0.5
|
WA241
|
to EN 1097-6
|
(max 0.5%)
|
Wcn.0.5
|
Resistance to freezing and
|
F,
|
F2
|
thawing, according to EN 1367-1 (in water or salt solution)
|
(max 1.0%)
|
(max 2.0%)
|
Resistance to freezing and thawing, according to EN 1367-2
|
|
MSla
(max 18%)
|
Resistance to thermal shock, according to EN 1367-5
|
Declared
|
—
|
Affinity of coarse aggregates to bituminous binders, according to EN 12697-11
|
Declared
|
|
“Sonnenbrand” of basalt, according to EN 1367-3 and EN 1097-2
|
SBsz (SBLA)
|
|
Coarse lightweight
|
^lpcA 1
|
mlpcO.1
|
contaminators according to
|
(max 0.1%)
|
(max 0.1%)
|
 |
WA241
|
Declared WA241 Wcn,0.5
|
F,
|
^NaCl^
|
(max 1.0%)
|
(max 7% in 1% NaCl solution)
|
|
|
Min 85%
|
Declared —
|
method В
|
|
SBLA
|
– SBLA
|
—
|
mlpcO.1 mLPC0.1 (max 0.1 %) (max 0.1 %)
|
|
|
|
TABLE 5.2 (CONTINUED)
Requirements for SMA Coarse Aggregate according to EN 13043 in Selected CEN-Member Countries, Aggregates for SMA at the Highest Traffic Level (Reference Mixture SMA 0/11)
List of Categories by Country
|
Germany TL Gestein StB 04 Anhang F
and TL Asphalt StB 07
|
Slovakia KLK 1/2009
|
Austria ONORM В 3584:2006 RVS 08.97.05:2007 (Class C1)
|
Switzerland SN 670130a: 2005
|
Poland
WT-1 Kruszywa 2008
|
Properties3
|
1
|
2
|
3
|
4
|
5
|
Dicalcium silicate disintegration of air-cooled blast furnace slag, according
|
Resistance required
|
|
Resistance required
|
According to other
regulations
|
Resistance required
|
toEN 1744-1, p. 19.1
|
Iron disintegration of air-cooled blast furnace slag, according to EN
|
Resistance required
|
|
Resistance required
|
According to other
regulations
|
Resistance required
|
1744-1, p. 19.2
|
Volume stability of steel slag
|
^3.5
|
^3.5
|
^3.5
|
According to
|
^3.5
|
aggregate, according to EN 1744-1, p. 19.3
|
(max 3.5%)
|
(max 3.5%)
|
(max 3.5%)
|
other
regulations
|
(max 3.5%)
|
Note: Cells with — mean no requirement (NR) category; FI = flakiness index; LA = Los Angeles; SI = shape index. a Names of properties after EN 13043
TABLE 5.3
Requirements for SMA Fine Aggregate according to EN 13043 in Selected CEN-Member Countries, Aggregates for SMA at the Highest Traffic Level
Properties
|
і
|
2
|
3
|
4
|
5
|
Grading, according to EN 933-1
|
GF85
|
GF85
|
Gf85
|
Gf85
|
Gp 85
|
Tolerances of typical gradation
|
GrcNR
|
GTC 20
|
GTC 20
|
Grc10
|
О
7
0
|
Fines content, according to EN
|
Declared
|
fio
|
/іб
|
/22
|
/16
|
933-1
|
|
(max 10%)
|
(max 16%)
|
(max 22%)
|
(max 16%)
|
Fines quality, according to EN
|
Declared
|
MBplO
|
—
|
—
|
MBF10
|
933-9
|
|
(max 10 g/kg)
|
|
|
(max 10 g/kg)
|
Angularity, according to EN
|
Ecs 35
|
—
|
Ecs 35
|
Declared
|
Ecs30
|
933-6, p.8
|
(min 35 sec)
|
|
(min 35 sec)
|
|
(min 30 sec)
|
Coarse lightweight contaminators,
|
mLPC0.1
|
—
|
—
|
—
|
тьрС0Д
|
according to EN 1744-1, p.14.2
|
(max 0.1%)
|
|
|
|
(max 0.1%)
|
TABLE 5.4
Requirements for SMA Filler according to EN 13043 in Selected CEN-Member Countries, Aggregates for SMA at the Highest Traffic Level
List of Categories by Country
|
Germany TL Gestein StB 04
|
Slovakia
|
Austria ONORM В
|
Switzerland
|
Poland
WT-1
|
|
Anhang F
|
KLK
|
3584:2006
|
SN 670130a:
|
Kruszywa
|
Properties
|
and TL Asphalt StB 07
|
1/2009 RVS 08.97.05:2007
|
2005
|
2008
|
Grading, according to EN 933-10 Harmful fines (fines quality),
|
Declared
|
According to Table 24 of standard: Sieve 2.0 mm = 100% passing Sieve 0.125 mm = 85-100% passing Sieve 0.063 mm = 70-100% passing
|
|
MBF10
|
according to EN 933-9 Water content (added filler), according
|
<%
|
<i%
|
<1%
|
<1%
|
(max 10 g/kg) <1%
|
to EN 1097-5, %
Stiffening properties: voids of dry
|
^28/45
|
_
|
^28/38
|
T28/45
|
T28/45
|
compacted filler (Rigden), according
|
(min 28%,
|
|
(min 28%,
|
(min 28%,
|
(min 28%,
|
to EN 1097-4
|
max 45%)
|
|
max 38%)
|
max 45%)
|
max 45%)
|
Stiffening properties: “Delta ring and
|
Ar&r8/25
|
Ar&b8/16
|
—
|
Ar&b8/25
|
Ar&r8/25
|
ball,” according to EN 13179-1
|
(min 8°C,
|
(min 8°C,
|
|
(min 8°C,
|
(min 8°C,
|
|
max 25°C)
|
max 16°C)
|
|
max 25°C)
|
max 25°C)
|
|
|
 |
Water solubility, according to EN Н7>10
1744-1 (max 10%)
Water susceptibility, according to EN Declared
1744-4
Calcium carbonate content of CC70
limestone filler aggregate, according (min 70%)
to EN 196-21
Calcium hydroxide content of mixed Declared
filler, according to EN 459-2 Bitumen number of added filler, —

according to EN 13179-2
Declared
— Declared
CC80 Declared
(min 80%)
Ka20 To be established
(min 20%) in contract
ПМ _
Dn 28/39
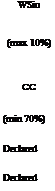
(min 28 max 39)
requirement for tolerance of gradation is not necessary; this is the situation in Germany, Switzerland, and a few other countries. In Poland, where limits for gradation during aggregate production do not exist, it was necessary to put such a requirement (categories G and GTC) in the national specifications.
• Legal systems and approaches to the requirements’ system also play roles.
In Europe, aggregates for asphalt mixtures are construction products and are produced and placed on the market according to Construction Product Directive[21] regulations. Internal regulations of each country have to be consistent with this directive. The product (aggregates) must fulfill specified requirements for intended use; countries are free to determine how they specify the system of requirements (only a few properties are indispensable). When we see Tables 5.2 through 5.4, it is obvious that some countries built a very broad system and established more detailed specifications than others. The reason is most likely in the existing approach to the requirements for components. In some countries only a few properties are specified because the final mixture (e. g., SMA) features are treated as the most important and a large degree of freedom is left for asphalt mix producers as long as they meet the final desired properties. In other countries everything is specified—both components and final mixture properties as well, which can ultimately lead to overspecification.