For more than two decades, stone matrix asphalt (SMA), called stone mastic asphalt in Europe, has been taking over the global asphalt paving market at a remarkably high speed. Its fast-growing popularity has been surprising to many people. Although asphalt concrete may have appeared to be the indisputable leading choice for an asphalt layer, increasing vehicle axle loads have forced the application of new and better solutions.
The SMA mix, or Splittmastixasphalt in German, has been known since the mid – 1960s. Dr. Zichner, a German engineer and manager of the Central Laboratory for Road Construction at the Strabag Bau AG, was its inventor. It was an attempt to solve the problem of the damage to wearing courses caused by studded tires. The trend in wearing course mixtures at that time in Germany was to use Gussasphalt (i. e., mastic asphalt) and an asphalt concrete with a low content of coarse aggregates. These types of surfaces were subject to fast wearing by vehicles equipped with studded tires. Both components, the mastic and the fine aggregates, were too weak to provide the mixture with suitable durability. Due to the high cost of pavement rehabilitation, strong demand for a new surface mix that could withstand studded tires was created. This was the impetus for Dr. Zichner’s work.
When we try to picture ourselves in Dr. Zichner’s situation, we would face—as he did—the task of designing an asphalt mixture that is resistant to wearing caused by studs and also is durable enough to have a long service life. He stated that coarse aggregate grains resistant to dynamic fragmentation, or crushing, were those that might guarantee the right wearing resistance. Thus they had to be the major components of prepared mixes to provide the needed wear resistance, whereas a high content of mastic and binder would produce a long service life. So the early idea for SMA consisted of creating a very strong aggregate skeleton of coarse aggregates and filling the spaces between them with mastic (i. e., a mix of binder, filler, and sand). That type of composition of an aggregate blend is typically called a gap-graded mineral mixture.
Initial trial attempts to construct the new mix consisted of spreading a hot mastic layer followed by spreading high-quality coarse aggregates over the mastic, then compacting the surface (with a road roller). The ratio of mastic to coarse aggregates
(by weight) was 30:70. The mastic was made up of 25% B80 or B65 binder,* 35% filler, and 40% crushed sand (RETTENMAIER, 2009a). Based on experiments with such a composition, Dr. Zichner drew up a recipe for production of the mixture in an asphalt plant. The approximate composition of the first large scale production mix was as follows (RETTENMAIER, 2009a):
5/8 mm coarse aggregates 0/2 mm crushed sand Filler
B80 (B65) binder
As we can see, there was none of the 2/5 mm aggregate in that mix that was typically used in other mix types; the absence of this size fraction produces a gap grading, as we shall see later (in Chapter 2).
Then the problem of draining-off the binder from the aggregate was encountered; with such a high binder content and few fines to hold the binder in the mix, the binder tended to flow off the coarse aggregate particles. It was acknowledged, after laboratory tests, that an additive of asbestos fibers would be a good drainage inhibitor (so – called stabilizer). Such a designed mix could be produced, transported, and laid in a traditional way (RETTENMAIER, 2009a).
The mixes were named by Dr. Zichner in 1968 as follows (Zichner, 1972):
• MASTIMAC—the name referring to mixes for layers 2-3 cm thick,
• MASTIPHALT— the name referring to mixes for layers thicker than
3 cm.
Early road sections of MASTIMAC were used on internal roads of asphalt plants belonging to the Strabag/Deutag Consortium, enabling them to gain experience with the new mixture. Eventually a public road was paved with the MASTIMAC mix on July 30, 1968, in Wilhelmshaven, Germany, on Freiligrath Strabe. The result was so encouraging that some other sections were paved with MASTIMAC soon afterward (RETTENMAIER, 2009b). Gradation curves of the new mixtures (Figure 1.1) were presented in a German publication (Zichner, 1972).
The stone mastic composition and its laydown were patented by Dr. Zichner in Germany, the United States, Sweden, France, and Luxembourg.[1] [2]‘ It is interesting how the inventor described his ideas in the U. S. patent text (Zichner, 1971):
the gravel size mixtures are composed…so that the percentage of the coarser size is greater than that of the smaller size. In this manner a relatively great interstitial volume is achieved in the gravel mix on the one hand, and on the other hand a good interfitting

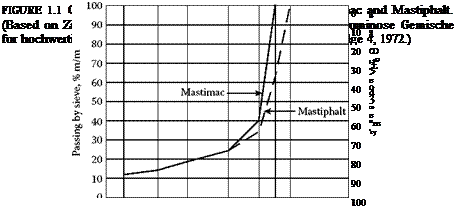
Mastic on grains
Pavement
FIGURE 1.2 First stage of the mix performance according to U. S. patent No. 3797951— after laying.
of the individual pieces [of] gravel is assured….The quantity and fluidity of the mastic is such that during and after the compacting, the mastic flows into the interstices between the stones forming the wearing course as aforesaid, and which the volume of the mastic is less than the interstitial volume of the stones..
In that patent, the approximate percentage of the mix composition was defined as 70% coarse aggregates, 12% filler, 8% binder, and 10% crushed sand. It was also indicated that stabilizing additives may be needed as well. As the reader can see, the mixture described above is similar to the contemporary understanding of an SMA mixture (Figures 1.2 and 1.3).
Today it is generally admitted that the idea of SMA has changed little since its inception. What is SMA today? We can agree on its definition here; SMA is an asphalt mixture containing a gap-graded aggregate mixture, with high contents of coarse aggregate fractions, filler, and binder. Most often a stabilizing additive (drainage inhibitor), which prevents the draindown of the binder from the aggregate, is needed.
Although SMA mix was originally intended only for wearing courses, in some countries it is also applied in binder (intermediate) courses (see Chapter 13). Polymer modified binders were not commonly available in the 1960s and 1970s, so only conventional binders were used. Although the binders were quite soft, it was soon noticed that SMA layers were very durable, and their rut resistance became especially evident.
The SMA mix was not forgotten in 1975 when a ban on the use of studded tires was introduced in Germany (Bellin, 1997). The concept of SMA turned out to be good not only for that kind of damage but also for rutting resistance and durability. Today SMA is regarded as an ideal mixture for heavy-duty asphalt pavements that require the highest resistance to damage and a very long service life. It is a practically synonymous with resistance to rutting.