In areas where the termites are especially hungry (Hawaii and some southern states), entire house frames can be built of pressure – treated wood. Pressure-treatment technology was developed to repel termites and inhibit rot, and it does so effectively. During the treatment process, a preservative compound is forced under pressure into raw lumber, penetrating deeply into each board.
For many years the main ingredient used in treated wood was arsenic. A dangerous poison, arsenic was effective in repelling termites but also harmed the workers who manufactured and used these construction materials. The EPA eventually banned the use of arsenic in PT wood, and suppliers replaced the arsenic with copper and other less harmful chemicals. Copper is what gives PT lumber its distinctive green or brown color. Because copper is quite corrosive, nails and metal fasteners had to be redesigned. It’s best to used hot-dipped galvanized nails (rather than regular steel nails) when working with pressure-treated wood. Always check with your supplier to make sure you use nails and metal fasteners that won’t corrode easily.
To avoid injury when handling and cutting PT lumber, it’s important to follow these safety precautions:
■ Use gloves when working with PT wood.
■ If you handle PT wood with bare hands, wash your hands before eating.
■ Don’t burn scrap PT lumber in your woodstove or anywhere else.
■ When cutting more than a few PT boards, wear a dust mask.
Posts, girders, and beams
Posts are vertical supports for horizontal pieces, which are called girders or beams. These major horizontal members support floor joists. Posts that sit on concrete piers are often made of PT wood.
Joists
Typically spaced 16 in. or 24 in. o. c., joists are installed parallel to each other and support the subfloor and rough plumbing. They span the entire house, running from one outside sill, across any interior girders, to the other
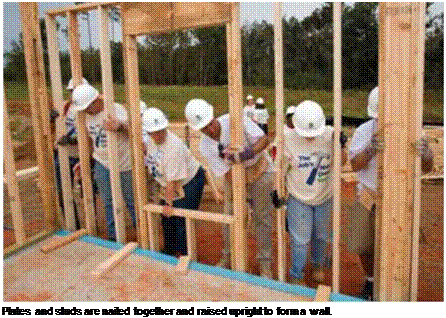
outside sill. Most often they are made from 2x-dimension lumber (such as 2x8s, 2x10s, or 2 x12s) or from manufactured, wooden I-beam joists.
Floor sheathing
Floors are usually sheathed with 5/8-in.- or 3/4-in.-thick, 4-ft. by 8-ft. sheets of tongue – and-groove plywood or oriented strand board (OSB). Better sheets have their edges treated with paint to inhibit moisture absorption in wet weather.
Wall plates
These are the 2×4 or 2×6 horizontal members that hold together the parts of a wall. Each wall has three plates—one on the bottom and two on the top. The two uppermost plates are called the top plate and the double top (or cap) plate. When framing on a concrete slab, the bottom plate is made of PT wood.
Studs
Studs are the vertical wall members nailed to the plates, and they are typically spaced either 16 in. or 24 in. o. c. The standard, precut stud length in many parts of the country is 92/4 in. That stud, along with three F/2-in.- thick wall plates (one on the bottom and two at the top), creates a framed wall that is 963/4 in. high. That leaves room for /Tin. or 3/8-in. drywall on the ceiling and full 8-ft. sheets on the walls. In addition to solid 2x lumber, you may also encounter finger-jointed studs, which are manufactured from shorter pieces of wood glued end to end. Some houses are being built with metal studs.
Materials matter. Builder’s felt, sometimes called tar paper, is rolled over the roof sheathing before asphalt shingles are installed.
![PRESSURE-TREATED LUMBER Подпись: Make sure that every window and door has proper flashing and caulking before setting them in place. [Photo by Don Charles Blom]](/img/1312/image130_0.gif)
Headers, trimmers, and cripples
The weight from above a window or door opening is transferred around the hole by a header nailed horizontally between studs. Trimmers nailed to the studs at both ends of the header support the header. Cripples, or jack studs, extend from the top of a header to the top plate, as well as from the bottom plate to the underside of rough windowsills.
Roof trusses
Each of these factory-made assemblies typically consists of a bottom chord (or joist chord), a top chord (rafter or rafter chord), and interior webbing. Trusses are often engineered to carry the entire weight of a roof’s load, transferring it to the exterior walls. That load can be considerable in snowy parts of the country. Trusses allow roof construction to be done quickly and easily. Most trusses for residential construction are spaced 24 in. o. c.
Fascia and gutter boards
These terms are often used interchangeably, but a gutter board is technically distinct from a fascia board. Both parts are installed over the ends of the rafter tails. A gutter board is nailed directly to the rafter tails, and it is covered by aluminum or vinyl cladding or by a fascia board that serves as the finished exterior’s trim surface. For more details, see Chapter 6.
Roof and wall sheathing
Roofs and walls are usually sheathed with V2-in.- or 5/8-in.-thick OSB. In some parts of the country, exterior walls, along with their gable trusses, are sheathed before they are raised upright. In earthquake and high wind areas, you are often required to sheathe some interior walls to help withstand lateral forces that can tear buildings apart. Take a look at the damage caused by Hurricane Katrina in the Gulf states and you begin to get the picture.
Housewrap and felt paper
Housewrap or felt paper is placed under siding
and shingles to prevent wind and water from entering stud cavities or the attic. You can also use a rain screen behind siding to help prevent moisture from getting trapped in these areas, which can cause mold.
Sealants
Construction adhesives, caulk, and other sealants are ever present on job sites. Most of those products come in cylindrical cartridges that fit inside a caulking gun, which is used to apply the caulk or sealant. Construction adhesives can be used to bond different materials together—floor sheathing to floor joists, for example. To prevent water leakage, caulks are used to seal around windows and doorframes, at siding joints, and where a bathtub meets the floor. They can be used under wall plates and around pipe holes to block out cold air. Gaps between baseboards and walls or door casings can be filled with caulk before painting. Be sure to buy the right type of caulk. Don’t use a basic latex painter’s caulk around exterior doors and windows, for example. Silicone caulks offer much better protection in these areas.
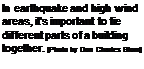
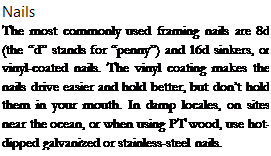
Screws
Drywall screws are the most universally used screws in house construction. But thanks to the popularity of cordless drill-drivers, all kinds of screws are now being used to build houses. Corrosion-resistant screws are available for deck construction and other outdoor applications. Other types of screws are used to install cabinets, built-ins, and hardware. Screws are typically described by head type (main types include flat, round, pan, and hex); length (given in inches); gauge, or shank, diameter (usually between 4 and 10); and typical use (drywall, wood, sheet metal, and so on). Although popular for general-purpose use, drywall screws aren’t strong enough to support heavy loads, such as wall cabinets.
Other fasteners
Toggle bolts, molly bolts, hollow-wall anchors, and other fasteners are used to help secure items, such as wire shelving to drywall panels. When fastening materials to a masonry surface