The first step to passively cooling your home is to stop the heat before it ever comes in. This is where siting and shading come into play. When designing a new house, you have a great opportunity to take advantage of orientation, but it’s also important (and often ignored) when adding to or altering an existing house.
Here in the Northern Hemisphere, a house that faces south is optimal because that is where the sun comes from. Southern orientation makes it easier to control the amount of sunlight that enters the house. Even in the South, designing a house with a long east-west axis (minimal exposure to the east and west, maximum exposure on the north and south) allows you to take the best advantage of the sun. This strategy is associated with passive heating, but passive cooling also benefits from the same type of siting.
When the house faces south, simple overhangs can shade it for the hottest part of the day, generally from 10 a. m. to 2 p. m. The
overhangs need to be sized correctly so that they not only block the sun at its hottest, but also allow light and warmth inside when the sun’s angle changes in the winter, and in the mornings and evenings. Because this factor is based on the latitude where you live, the proper size of the overhang varies from region to region. The latitude where I live in North Carolina is 35 degrees north. That means the sun rises to 78 degrees above the horizon in summer and 30 degrees in winter. Here, a 2-ft. overhang is optimal because it blocks the hottest summer sun but lets the low winter sun shine inside (see the drawing on the facing page). To determine the optimal overhang where you live, see the chart on p. 131.
In the early morning and at sunset, when the summer sun is much lower in the sky, it’s harder to keep heat out of the house, even with overhangs. You can minimize this morning and evening heat gain by minimizing the number of windows on the east and west sides of the house.
Another strategy is to locate shading devices, such as a screened porch, on the east
or west sides of the house to provide protection from the low sun. By keeping the porch away from the south side, you’re not compromising the daylighting and heat benefits available from the south. Other options for shading include pergolas, screens, and plantings. Pergolas, in particular, are a great option; they not only shade the house but also create an outdoor space to enjoy. Growing vines on pergolas can increase the structure’s shading ability. Be sure to select deciduous varieties; they’ll provide maximum shade when fully leafed out in summer, but won’t block sunlight in winter.
Landscaping complements your house visually and also can help to keep it cool. Plant larger plants and trees to the east and west for shade. Plants absorb heat, lowering the temperature of air moving over them, so air that enters your house after traveling over the garden is actually cooler than the surrounding air. Low bushes and plantings also help by minimizing hard surfaces that absorb heat and radiate it back toward the house. These "heat islands"—driveways, walkways, and patios—work against any passive-cooling measures you might have taken, particularly if your house has windows that are low to the ground and capture the hot air that radiates off these surfaces. Lower roofs on porches or bump-outs, especially those covered with asphalt shingles, radiate heat that can enter the house
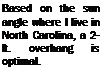


through windows open above them. In these situations, casement windows are the most effective at guiding cool breezes into the house, and they allow less of the heat radiating off the roof to gain access inside. Avoid awning windows, which channel rising hot air into the house.
Enhancing passive cooling through orientation and siting is easiest when designing a new home. But installation of window overhangs and the use of plantings and attached structures can boost the cooling power of existing homes as well.
BLINDS DON’T REALLY HELP
People often use internal shading, such as blinds, to keep the heat out of their homes. While it’s certainly better than letting sunlight stream in unimpeded, it’s really not a good strategy if you look at the science. When sunlight shines through the glass in windows, its wavelength lengthens. These longer wavelengths cannot travel back out through the glass, so the heat gets trapped inside. (This is how greenhouses maintain their warm environments.)
When you put up blinds, you block light from getting into the room. However, the heat from the sun’s rays has already entered through the glass. Because heat always moves from hot to cold areas, the heated air trapped between the window glass and the blind moves into the cooler areas of the house. Blinds may help a bit, but it’s better to invest in exterior shading devices to stop the sun from ever entering the house rather than trying to control it once it’s there.